Supplier outlines corrosion challenges for long-lead items
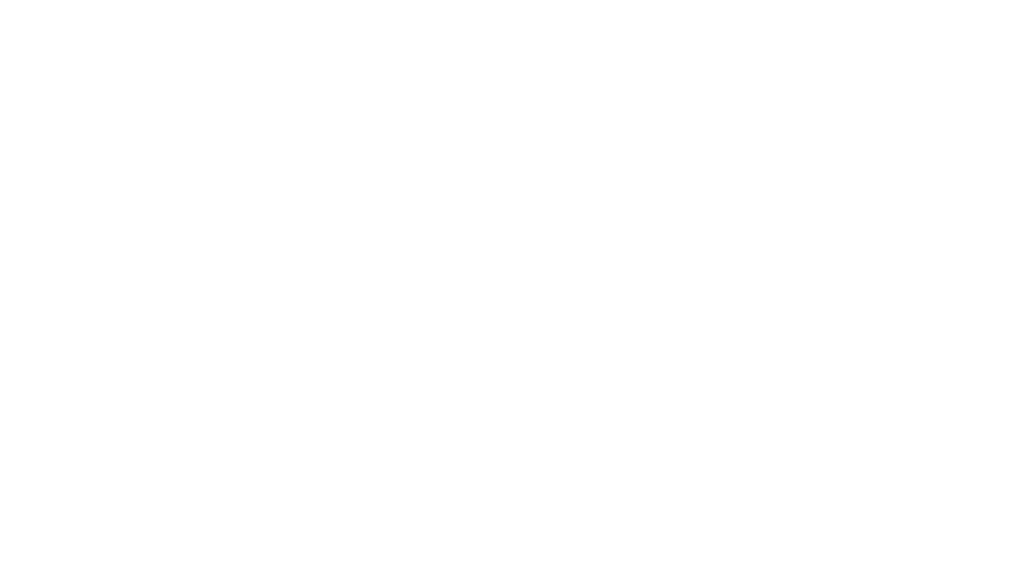
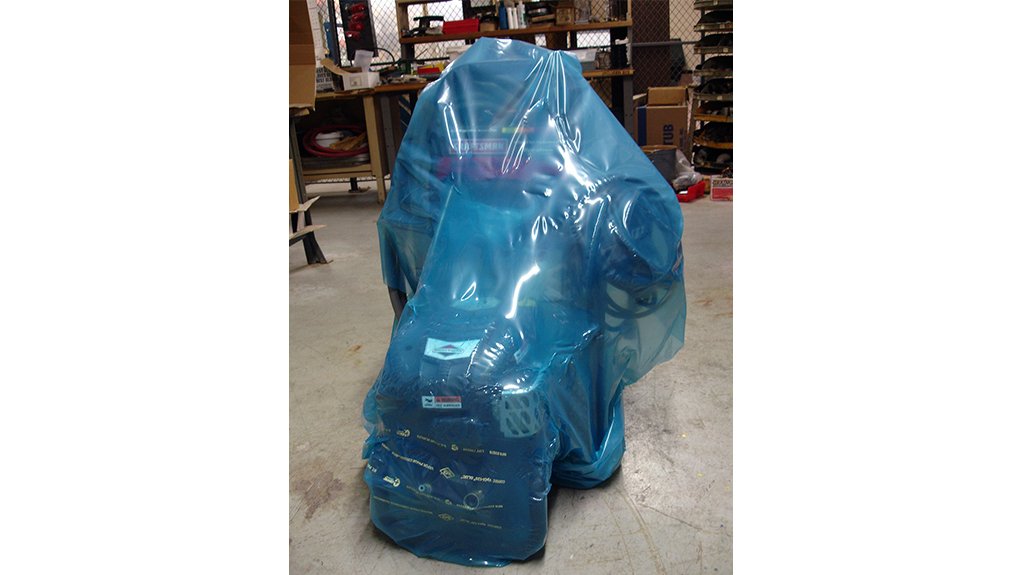
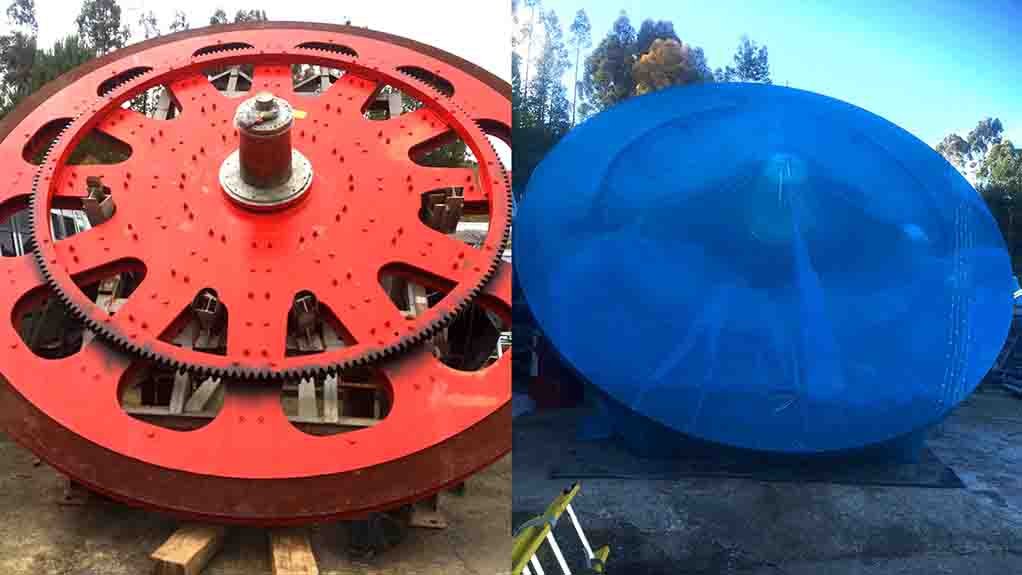
IN GOOD ORDER Goods receipt, which is often overlooked because of speed and cost considerations, has become a critical factor in the detection of corrosion or mechanical damage in the transported equipment
PROPER PREPARATION Proper preservation material selection is the best first step
Oil and gas facility owners and operators face numerous challenges regarding effective corrosion protection that can directly impact on their operating a profitable, safe and compliant facility, says corrosion technologies developer Cortec.
Oil and gas facilities are inherently complex operations requiring highly engineered, high-cost spares, as well as “low dollar value, but high dollar risk parts”, explains Cortec integrity management and preservation solutions VP Bob Boyle.
As these facilities are often situated in remote locations that necessitate long-lead times and thousands of line items to allow for the continuous operation of critical systems, companies cannot rely on ‘just-in-time’ manufacturing or logistics processes.
“This results in the standard original equipment manufacturer- (OEM-) based transit protection being insufficient for oil and gas facilities . . . OEMs design for easier locations and lack the knowledge, experience or ability to customise their methods for the lead-time challenges posed by, for example, offshore oil and gas facilities,” he elaborates.
Supply Chain Issues
The supply chain has multiple handoff points, making it very challenging for many traditional methods of corrosion control to remain intact and effective through transitions – from OEMs; freight forwarders; engineering, procurement and construction (EPC) contractors; and materials handling at goods receipt, to storage on the shelf.
Goods receipt, which is often overlooked because of speed and cost considerations, has become a critical factor in the detection of corrosion or mechanical damage in the transported equipment.
It is often a liability from a handoff perspective because it is usually staffed by personnel who are not expected to thoroughly inspect or identify the spares, and often only count and move the items to stockholding facilities.
Goods receipt processes can, however, involve spare parts being inspected competently, as opposed to OEM preservation measures involving packaging and crating products designed only to deliver to the site, not for an extended period beyond.
According to Boyle the only way to restore a preservation period would involve essentially repairing the damage, replacing the desiccant and pulling a vacuum again – which is often more expensive and requires materials and tools that are often not located in the goods receipt area.
“Some clients have, therefore, shifted to preservation and goods receipt co-existing, so the right competency is located where it is needed – and 100% quality control can be attained for any items destined for the shelf.”
He adds that, in other cases, preservation is pushed back to suppliers and carefully specified so that the preservation methods can withstand comprehensive inspection processes.
“Proper preservation material selection is the best first step. The material selection and specification process should be specific to the desired ‘pick-and-pull’ strategy, allowing for goods receipt for nonoperating maintenance, audits, inspections on the shelf and staging.”
Noting that it is not always an option to push the corrosion mitigation back onto the supplier. Boyle advises that oil and gas facilities should implement effective financial accountability processes, as well as an on-site corrosion mitigation programme that could be co-located with the preservation area.
“When done well, this allows for robust protection that harmonises with the various touch points for not only goods receipt for material movements or staging for turnaround, but also issuance to operations and return to stock.”
He adds that goods receipts are an opportunity to reject or return items – which is often an important and “perhaps difficult choice” guided by cost, lead time and immediate demand – and often does not allow for an effective solution for the operational side of the plant.
Further, with oil and gas facility downtime being “staggeringly expensive”, planned and unplanned downtime and outages form part of an “incredibly tight supply and maintenance schedule”.
Therefore, any part that cannot be installed because of corrosion can cost “thousands in shipping or hotshot costs, and disrupt the even more expensive repair schedule”, he says.
Cortec collaborates with suppliers, project owners and site operators to design the proper specifications that are practical and cost effective within cost and operation constraints.
Often, the first decision that immediately delivers operational savings is simply having a conversation with subject matter experts, such as Cortec, says Boyle.
Oil and gas facilities are still subject to engrained habits in some cases, such as their relying on OEMs and freight forwarders operating well outside of their expertise.
“The primary risk we run into is fear of change, showing up as the “blame game” between OEM and [a] facility.”
Harmonising with OEMs, as well as having a proper preservation philosophy and preservation plans from departments in place, will ensure the preservation programme is effective, Boyle concludes.
Comments
Press Office
Announcements
What's On
Subscribe to improve your user experience...
Option 1 (equivalent of R125 a month):
Receive a weekly copy of Creamer Media's Engineering News & Mining Weekly magazine
(print copy for those in South Africa and e-magazine for those outside of South Africa)
Receive daily email newsletters
Access to full search results
Access archive of magazine back copies
Access to Projects in Progress
Access to ONE Research Report of your choice in PDF format
Option 2 (equivalent of R375 a month):
All benefits from Option 1
PLUS
Access to Creamer Media's Research Channel Africa for ALL Research Reports, in PDF format, on various industrial and mining sectors
including Electricity; Water; Energy Transition; Hydrogen; Roads, Rail and Ports; Coal; Gold; Platinum; Battery Metals; etc.
Already a subscriber?
Forgotten your password?
Receive weekly copy of Creamer Media's Engineering News & Mining Weekly magazine (print copy for those in South Africa and e-magazine for those outside of South Africa)
➕
Recieve daily email newsletters
➕
Access to full search results
➕
Access archive of magazine back copies
➕
Access to Projects in Progress
➕
Access to ONE Research Report of your choice in PDF format
RESEARCH CHANNEL AFRICA
R4500 (equivalent of R375 a month)
SUBSCRIBEAll benefits from Option 1
➕
Access to Creamer Media's Research Channel Africa for ALL Research Reports on various industrial and mining sectors, in PDF format, including on:
Electricity
➕
Water
➕
Energy Transition
➕
Hydrogen
➕
Roads, Rail and Ports
➕
Coal
➕
Gold
➕
Platinum
➕
Battery Metals
➕
etc.
Receive all benefits from Option 1 or Option 2 delivered to numerous people at your company
➕
Multiple User names and Passwords for simultaneous log-ins
➕
Intranet integration access to all in your organisation