Sector initiating strategies to decarbonise by 2050
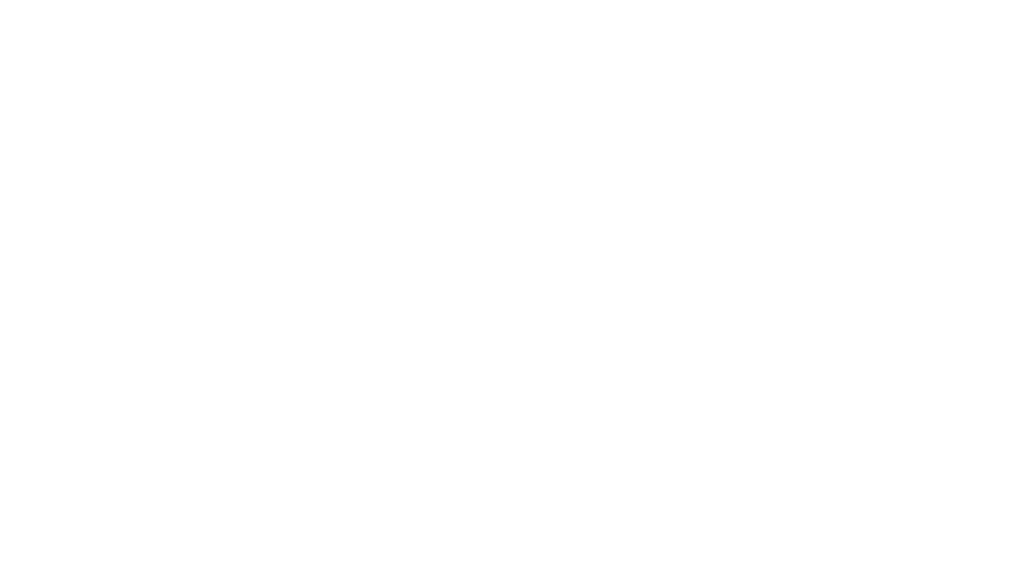
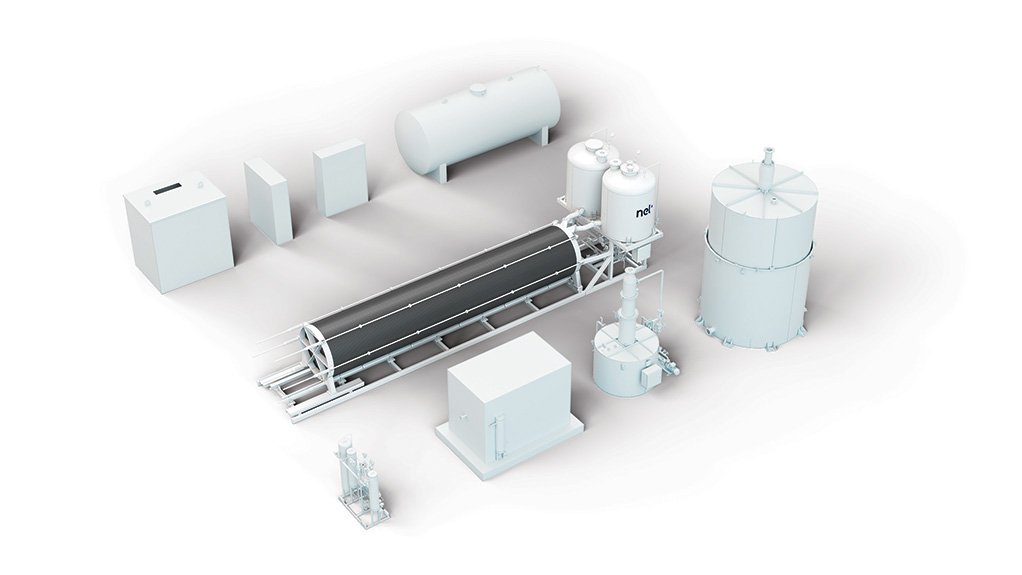
GO GREEN OR GO HOME Water electrolysis uses electricity to split water into hydrogen and oxygen, without releasing carbon emissions
To achieve carbon-neutrality by 2050, all sectors are initiating strategies to help reduce their carbon footprint, and this includes the stainless steel sector.
As the stainless steel sector depends on the steel industry for product input, the sector depends on the steel industry to set the pace for carbon reduction, says global hydrogen company Nel Hydrogen territory manager David Wolff.
The steel industry is a major contributor to carbon emissions, he notes, with the World Steel Association predicting that steelmaking globally contributes about 8% of carbon emissions every year.
In the near term, Wolff suggests that it is practical to incentivise and mandate that steel mills reduce their carbon emissions from their existing facilities.
Steelmaking has several options for decarbonisation, including some that are mutually exclusive, and others that can be combined for additional benefits, he says.
Recycled Steel
Wolff says while the long-term conversion from blast furnace steelmaking to electric arc furnace (EAF) steelmaking will help reduce carbon emissions substantially, EAFs require a rich iron feedstock, which is typically recycled steel.
Coal-based direct reduced iron (DRI) EAF feedstock can be replaced over time with natural gas-based DRI feedstock and, potentially in the future, hydrogen-based DRI. The transition from coal to natural gas to hydrogen reduces the carbon emissions of the reducing gas atmosphere of steel raw material production, allowing for the full decarbonisation of ore upgrading for EAF feedstock.
Meanwhile, new technology by energy transformation company Boston Metals is considering options for direct electrochemical ironmaking. This would be an example of an entirely new approach to ore upgrading.
Wolff notes that the commercial progress of this technology to date has been slow, owing to its relatively low technology-readiness level, huge investments and the demand for large amounts of electricity.
Progress towards decarbonisation could be accelerated by a more robust and capable system of carbon accounting. Wolff says interest at present is bifurcated – either steel is seen to be ordinary or undistinguished relating to carbon intensity, or it is zero carbon, selling for a major price markup.
“Why can’t there be ‘flavours’ of carbon reduction to enable steel users to select the degree of carbon reduction that they can pay for?” he questions.
Green hydrogen will replace grey hydrogen (hydrogen made from hydrocarbons) in annealing and rolling applications and, at current natural gas prices, this substitution is cost effective in the near term, says Wolff.
The substitution of green hydrogen for carbon monoxide used as atmosphere constituent in DRI manufacturing will also reduce carbon emissions to make iron units for EAF steelmaking.
Wolff says large quantities of hydrogen are needed to keep up with required iron units for steel production, and the economics are “quite challenging” with green hydrogen being more expensive than reformed natural gas.
Hydrogen as Heating Fuel
Wolff states that hydrogen is a powerful chemical reducing gas, and that use of hydrogen creates only water vapour, with essentially zero greenhouse-gas activity.
To date, the oxy-fuel combustion of coal has been the standard heating fuel for basic oxygen furnace steelmaking, while EAFs have used electricity. It is expected that the use of electricity in the EAF will continue, however, green steel will require that the plant electricity supply would need to be green – not currently the case at most sites, he adds.
Hydrogen as a heating fuel has some challenges, Wolff comments. It has a very low gas heating value per unit of volume, high flame speed and low flame luminosity.
The most challenging aspect of implementing hydrogen steelmaking may be accessing sufficient volumes of cost-effective green hydrogen. Today’s reducing gas produced on site through the partial combustion of coal or natural gas to make carbon monoxide and some volumes of hydrogen, uses raw materials coal by rail or natural gas by pipeline. The green generation of hydrogen at a site will require massive additional electricity infrastructure, and the green electricity to deliver through the additional wires.
Wolff says the most accepted approach for green hydrogen generation in the production of steel and stainless steel is water electrolysis, which uses electricity to split water into hydrogen and oxygen, without releasing carbon emissions.
However, while water electrolysis does not make or release any carbon emissions, many sources of electricity generation are carbon intensive. Using high carbon electricity to electrolyse water creates hydrogen that cannot be called green because the carbon emissions are high.
There are many options to eventually achieve net-zero emissions; however, owing to the complexity and massive investments required for implementation to be feasible, it will be achievable only in the next few years, Wolff concludes.
Comments
Press Office
Announcements
What's On
Subscribe to improve your user experience...
Option 1 (equivalent of R125 a month):
Receive a weekly copy of Creamer Media's Engineering News & Mining Weekly magazine
(print copy for those in South Africa and e-magazine for those outside of South Africa)
Receive daily email newsletters
Access to full search results
Access archive of magazine back copies
Access to Projects in Progress
Access to ONE Research Report of your choice in PDF format
Option 2 (equivalent of R375 a month):
All benefits from Option 1
PLUS
Access to Creamer Media's Research Channel Africa for ALL Research Reports, in PDF format, on various industrial and mining sectors
including Electricity; Water; Energy Transition; Hydrogen; Roads, Rail and Ports; Coal; Gold; Platinum; Battery Metals; etc.
Already a subscriber?
Forgotten your password?
Receive weekly copy of Creamer Media's Engineering News & Mining Weekly magazine (print copy for those in South Africa and e-magazine for those outside of South Africa)
➕
Recieve daily email newsletters
➕
Access to full search results
➕
Access archive of magazine back copies
➕
Access to Projects in Progress
➕
Access to ONE Research Report of your choice in PDF format
RESEARCH CHANNEL AFRICA
R4500 (equivalent of R375 a month)
SUBSCRIBEAll benefits from Option 1
➕
Access to Creamer Media's Research Channel Africa for ALL Research Reports on various industrial and mining sectors, in PDF format, including on:
Electricity
➕
Water
➕
Energy Transition
➕
Hydrogen
➕
Roads, Rail and Ports
➕
Coal
➕
Gold
➕
Platinum
➕
Battery Metals
➕
etc.
Receive all benefits from Option 1 or Option 2 delivered to numerous people at your company
➕
Multiple User names and Passwords for simultaneous log-ins
➕
Intranet integration access to all in your organisation