New chute design mitigates materials transfer problems
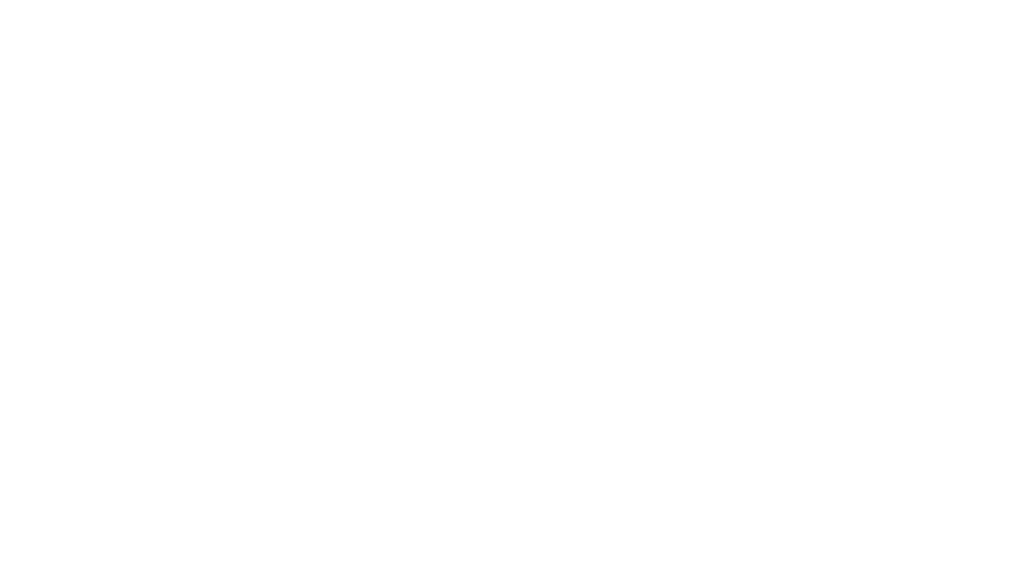
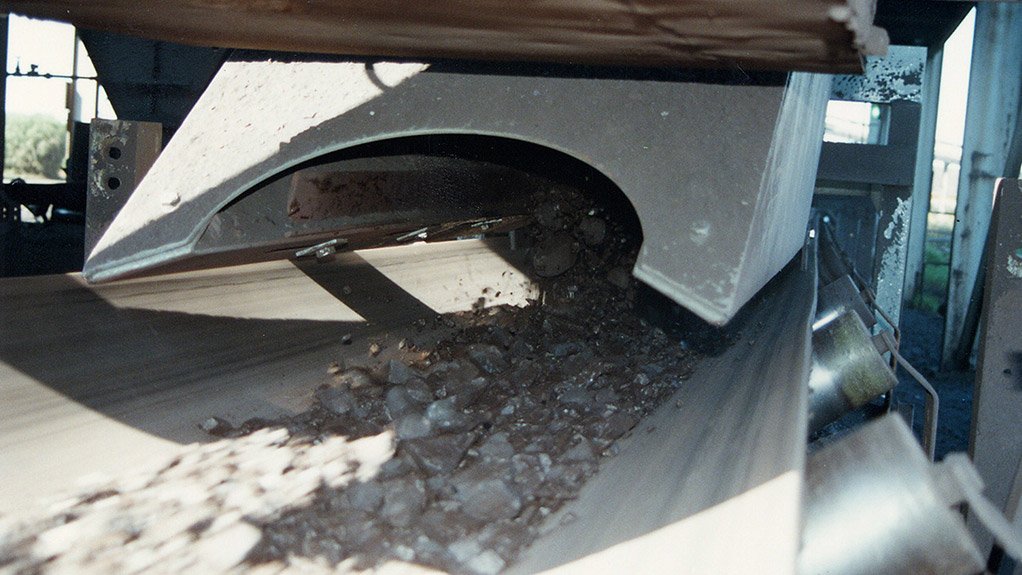
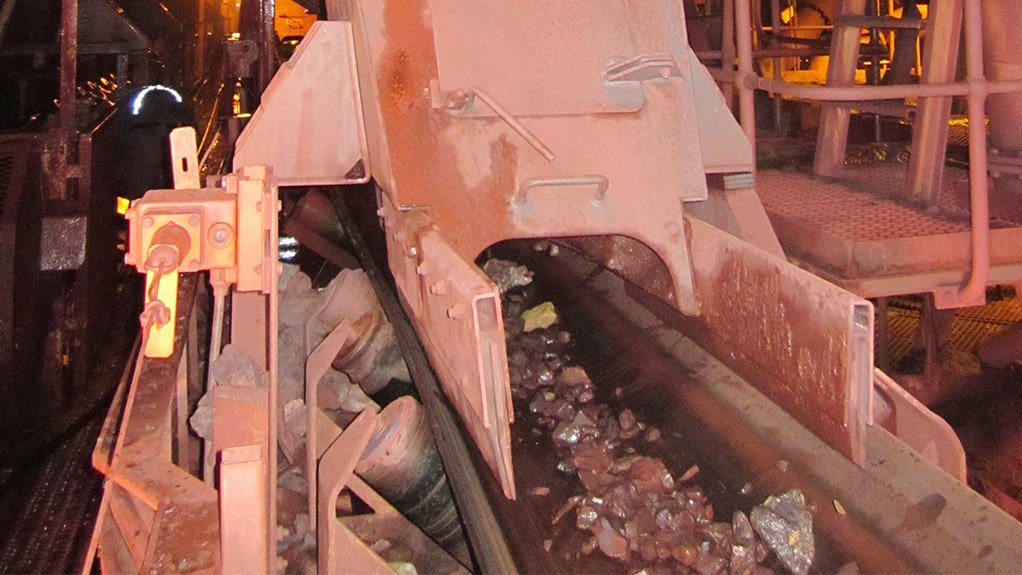
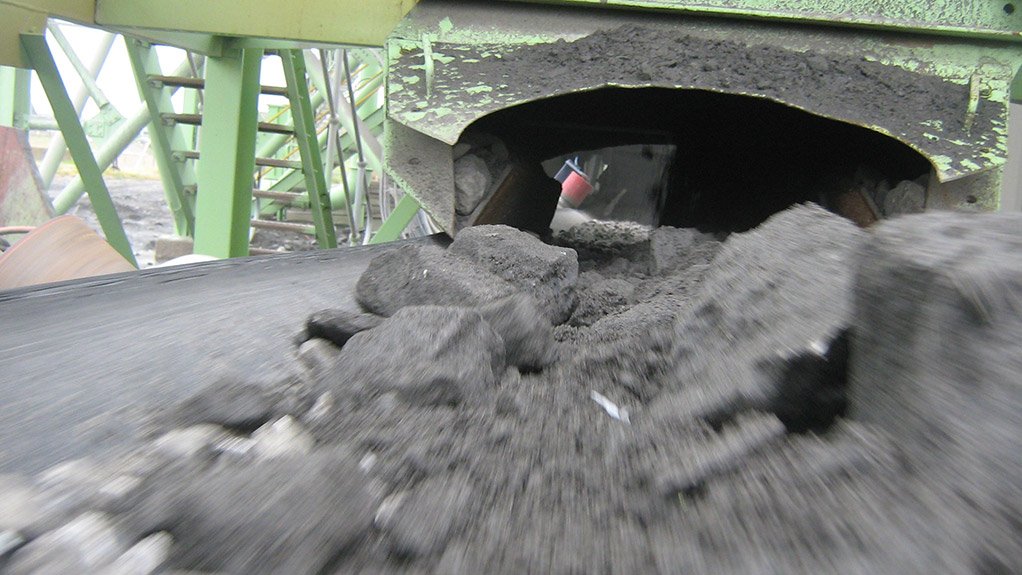
MATERIAL TRANSFER PROBLEMS Individual Weba Chute systems are configured to control the direction, flow and velocity of the calculated volume and type of material processed
TRANSFER POINT Chutes control material in a transfer point resulting in major advantages
SUBSTANTIAL REDUCTION The correct use of Weba Chute’s approach to the dynamics of bulk materials handling has reduced the problems associated with conventional transfer chutes
Considering basic chute specifications and design could mitigate material transfer problems, though this necessitates a thorough knowledge of transfer point design, as well as the ability to determine best practice for specific applications and the ability to customise each design accordingly, says chute systems company Weba Chute Systems MD Mark Baller.
He notes that the company’s system takes all these factors into account and is based on the lined ‘super tube’ or cascade system, which is necessary when material runs on material.
“Numerous successful installations of Weba Chute’s systems have proved that the correct application of our scientific approach to the dynamics of bulk materials handling can completely eliminate the problems associated with conventional transfer chutes, resulting in significant cost savings,” he adds.
To date, the company has engineered more than 4 000 transfer chutes, which are operating successfully throughout the global mining industry. “We consider a holistic design that not only focuses on the entry and exit points, but which also incorporates the control of the flow, volume and velocity of the material being transferred, at all times,” notes Baller.
By custom designing each transfer point, individual Weba Chute systems can be configured to control the direction, flow and velocity of the calculated volume and type of material processed in a particular application. “The end result is a transfer point that substantially reduces expendi- ture in minerals processing,” he says. This is achieved by increased productivity and adherence to environmental regulations, in addition to decreased replacement and maintenance costs.
“Conventional chute design is often associated with the uncontrolled discharge of bulk materials, which is linked to escalated maintenance and replacement costs. In addition, the presence of dust with conventional transfer points is an aggravating factor,” says Baller. Therefore, stringent environmental regulations have to be put in place to control dust emissions.
System design is undertaken using sophisticated three-dimensional computer software, in addition to the relevant data received from the client. Weba Chute’s systems are manufactured in an ISO 9001-accredited facility, which ensures quality manufacture. Performance is guaranteed in accordance with operational and application parameters, ensuring the provision of a chute solution that works for every application.
Reducing Conveyor Costs
Weba Chute Systems says a conveyor belt can account for up to 60% of the maintenance cost of a bulk materials handling plant. This means that the cost implications of constant replacement owing to wear can be significantly higher than the original investment.
“Maintenance outlay in the minerals processing sector can be reduced substantially by applying an innovative concept, such as a Weba Chute System transfer point,” notes Baller.
He adds that transfer points can contribute to some of the highest maintenance costs on a mine. “However, many engineers often do not view transfer systems as a critical element of the minerals processing system.”
However, Baller says the company believes that transfer points should be accorded the same level of importance as any other machinery in the minerals processing cycle.
The uncontrolled discharge of bulk materials through conventional chutes results in increased maintenance and replacement costs. “All of this adds up to unneces- sary expenditure and a headache for the engineers concerned,” says Baller, noting that the correct use of a streamlined, scientific approach to the dynamics of bulk materials handling greatly reduces the problems associated with conventional transfer chutes, resulting in significant cost savings.
Comments
Press Office
Announcements
What's On
Subscribe to improve your user experience...
Option 1 (equivalent of R125 a month):
Receive a weekly copy of Creamer Media's Engineering News & Mining Weekly magazine
(print copy for those in South Africa and e-magazine for those outside of South Africa)
Receive daily email newsletters
Access to full search results
Access archive of magazine back copies
Access to Projects in Progress
Access to ONE Research Report of your choice in PDF format
Option 2 (equivalent of R375 a month):
All benefits from Option 1
PLUS
Access to Creamer Media's Research Channel Africa for ALL Research Reports, in PDF format, on various industrial and mining sectors
including Electricity; Water; Energy Transition; Hydrogen; Roads, Rail and Ports; Coal; Gold; Platinum; Battery Metals; etc.
Already a subscriber?
Forgotten your password?
Receive weekly copy of Creamer Media's Engineering News & Mining Weekly magazine (print copy for those in South Africa and e-magazine for those outside of South Africa)
➕
Recieve daily email newsletters
➕
Access to full search results
➕
Access archive of magazine back copies
➕
Access to Projects in Progress
➕
Access to ONE Research Report of your choice in PDF format
RESEARCH CHANNEL AFRICA
R4500 (equivalent of R375 a month)
SUBSCRIBEAll benefits from Option 1
➕
Access to Creamer Media's Research Channel Africa for ALL Research Reports on various industrial and mining sectors, in PDF format, including on:
Electricity
➕
Water
➕
Energy Transition
➕
Hydrogen
➕
Roads, Rail and Ports
➕
Coal
➕
Gold
➕
Platinum
➕
Battery Metals
➕
etc.
Receive all benefits from Option 1 or Option 2 delivered to numerous people at your company
➕
Multiple User names and Passwords for simultaneous log-ins
➕
Intranet integration access to all in your organisation