Mintek’s AMAZEMET acquisition to support SA’s additive manufacturing ambitions
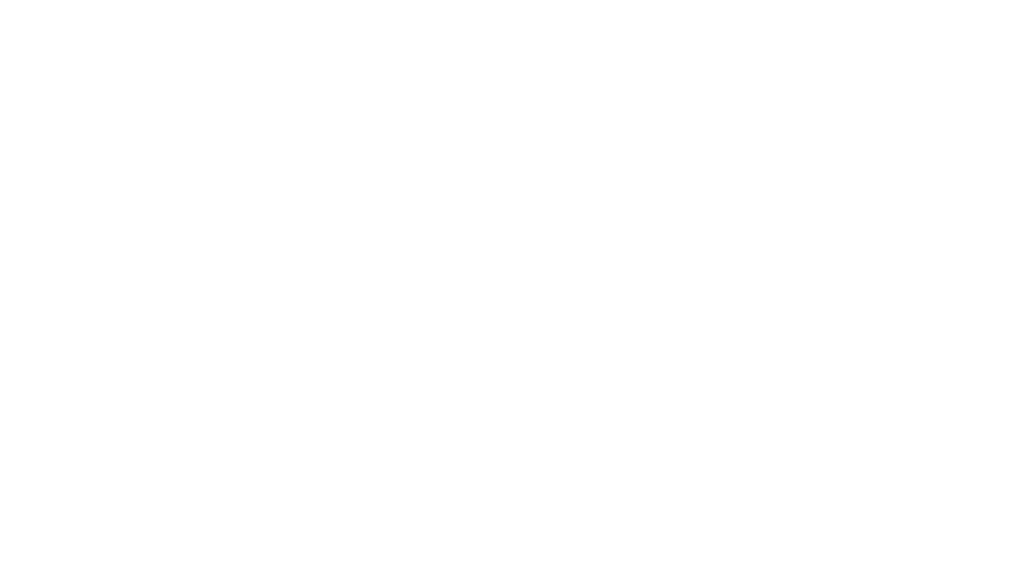
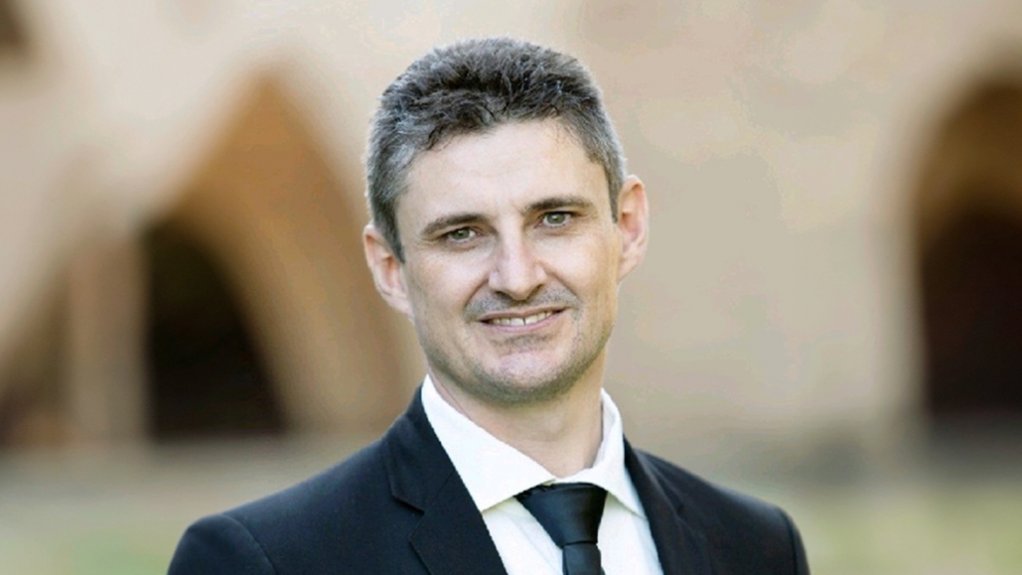
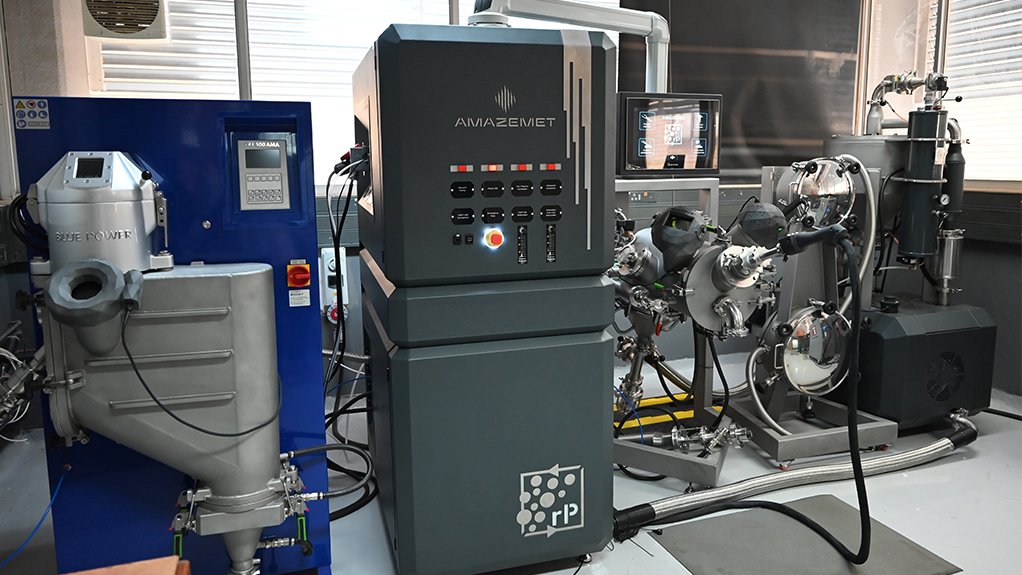
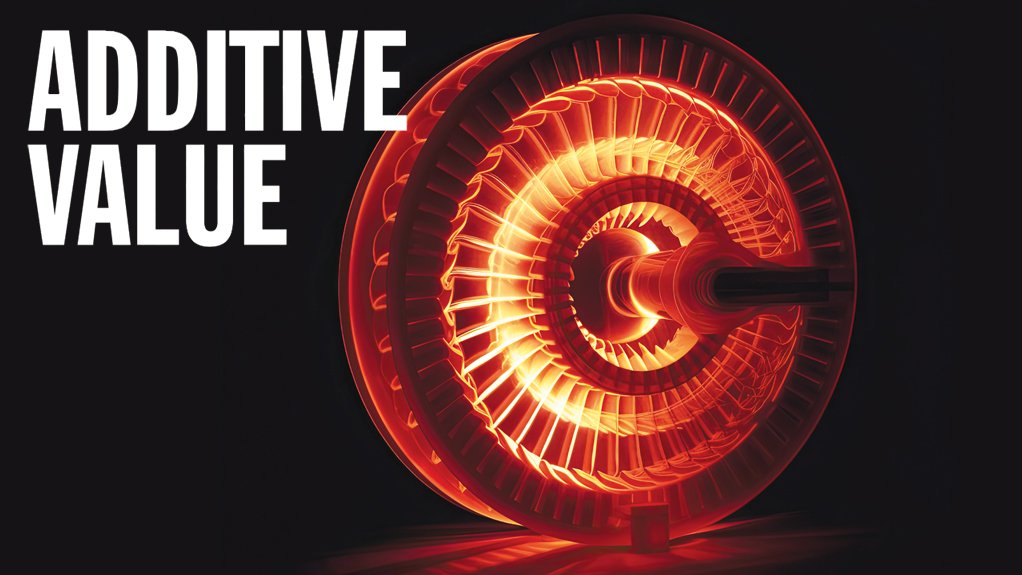
HEIN MOLLER We have a very active metal 3D printing community in South Africa, but we don’t have the infrastructure to produce the powders
The AMAZEMET machine
Mintek’s latest technological acquisition, the AMAZEMET rePowder ultrasonic atomisation and alloy development machine, is an extremely advanced piece of equipment that is expected to strengthen and bolster the country’s minerals-based and three-dimensional (3D) printing industries.
The machine also aligns with the national mineral processing and metallurgical research council’s goal of providing critical infrastructure for South Africa’s industrial development.
Mintek is, thus, acquiring a 3D metal printing machine to complement the AMAZEMET system and hopes to receive it by the end of this month, Mintek chief engineer Dr Hein Moller tells Engineering News & Mining Weekly.
Mintek presented the AMAZEMET machine to delegates from various industries in September, following a rigorous procurement process spanning several years; it has now been commissioned at the entity’s Johannesburg premises.
Moller says the equipment can be used to make metal powders and button castings, the latter of which can be used to verify the experimental modelling of novel alloys.
The rePowder machine can process almost any material, ranging from alloys with low melting points to those with high melting thresholds.
It produces high-quality metal powder with “outstanding particle-size distribution and flowability”, comparable to a level of quality that, historically, has only been found in powders imported from abroad.
Moller says the spherical and very homogenous powder particles allow for further processing, such as for 3D metal printing.
The acquisition represents a “pioneering achievement” for the country, as it did not previously have ultrasonic atomisers – only gas and water atomisers – and can now manufacture castings, unlike gas atomisers.
The ultrasonic atomiser can use very small quantities of metals, unlike the gas atomisers, which is especially important for research and development requiring precious metal resources and other expensive commodities, adds Moller.
When Moller has to coordinate the country’s precious materials development network, a considerable challenge is sourcing material for experimental work, owing to the expense of the metals.
However, the equipment can use different types of feedstock material, as opposed to other ultrasonic atomisation systems than can use only wire or rods, which “gives you the flexibility of not having to convert your material to wire or rod form which, again, assists [in] . . . working with expensive materials”, Moller elaborates.
3D Metal Printing
The benefits of this acquisition include strengthening and diversifying the country’s 3D metal printing industry.
While the 3D printing industry is “in a very healthy state”, with many universities, science councils, private companies and services companies undertaking metal 3D printing, all the powder that is used for these activities is imported, explains Moller.
“We have a very active metal 3D printing community in South Africa, but we don’t have the infrastructure to produce the powders.”
Importing requirements entail having to order a minimum quantity, which constrains stakeholders’ ability to work with many different materials because they are expensive.
Moreover, it can sometimes be difficult to import certain powders, as they are classified as controlled goods and are, therefore, regulated by the Non-Proliferation of Weapons of Mass Destruction Act, in line with the Non-Proliferation of Nuclear Weapons Treaty.
Mintek is, therefore, aiming to use the atomiser acquisition to build the country’s capacity to make powders for the local 3D printing community and, eventually, expand to making niche alloys for export.
Additive manufacturing is one of the pillars of the Fourth Industrial Revolution, and it is imperative that the country does not fall behind in this, Moller emphasises.
He adds that the country has all the requisite minerals but is focused only on the 3D printing side using imported powders. Ideally, the reverse approach should have been followed, with the focus being, firstly, on beneficiation, and then on printing.
Mintek is aiming to address this by investing in the required infrastructure to complement the acquisition of the AMAZEMET equipment and, on receipt of the 3D metal printer, it will be able to manufacture metal powders and then test them using the printer, providing valuable insights for the 3D printing industry.
Moller lauds this as a positive for localisation. He highlights that Mintek’s approach is to source different pieces of equipment that complement one another, and then to build a complete, comprehensive programme regarding 3D metal printing, instead of focusing on projects in isolation.
Broad-Based Benefits
Speaking at the unveiling of the AMAZEMET, Mintek physical metallurgy head Joseph Moema emphasised the utility of the machine.
“This is pivotal for Mintek, as it will benefit a wide array of industries, including glass, biomedical, aerospace and jewellery. For instance, in the biomedical field, high-quality metal powder can be used to produce orthopaedic implants, dental prosthetics and even drug delivery systems.
“These applications rely on precision and material quality – areas where our technology excels. It aligns with our strategy to foster minerals-based industries in South Africa by providing value-adding technologies and services, thereby expanding the minerals- based value chain,” he said.
Moema said that Mintek saw many prospects for forging a mutually beneficial partnership with stakeholders across a diverse portfolio of metals.
Moller notes that, theoretically, the equipment can be used to beneficiate all the country’s minerals where 3D printing can add value to the economy.
He notes that, since the unveiling, considerable interest has been expressed, surpassing initial expectations, especially from organisations active in the 3D printing community, such as the Council for Scientific and Industrial Research (CSIR), the National Laser Centre and the Central University of Technology (CUT), in the Free State.
Mintek was also due to present this equipment at the recent Rapid Product Development Association of South Africa’s Conference (RAPDASA-RobMech-PRASA-AMI Conference) at the CSIR at the start of November to showcase it to a wider audience from the 3D printing community.
Research groups working in alloy development have expressed interest, as Moller notes that, although South Africa is “very strong” on the computational aspect, it lacks in actual alloy manufacture and experimental verification of the models.
Many requests from universities – to support postgraduate students with samples and develop new parameters for 3D printing applications – have also been received.
Moller adds that Mintek can also “recycle” components, with companies sending pieces that have been incorrectly 3D-printed, which are then re-atomised and turned back into a powder.
He emphasises the considerable scope in, and interest from, the precious metals industry – given the country’s considerable endowment of platinum group metal (PGM) reserves –
highlighting the attendance of Anglo American Platinum and the University of Pretoria at the unveiling, with the latter actively engaged in 3D-printed jewellery research.
International representation included Platinum Guild International (PGI) India and PGI China, as well as Helmich Luxury Group CEO Josh Helmich, with the company having a keen interest in patented platinum alloys and furthering jewellery manufacturing technologies.
Moller avers that the equipment is ideal for 3D-printed jewellery, as it can make platinum alloy powders using relatively small quantities, and when the 3D printer acquisition is realised, it can print very complex, customised jewellery that would not be possible to manufacture using other techniques.
Mintek has had talks with Sibanye-Stillwater and Impala Platinum, as these PGM miners are looking for new applications for their commodities to supplement and diversify from their focus on the hydrogen economy, he notes.
Other important areas of interest include the biomedical field, as high-quality metal powder can be used to 3D-print customised implants that are patient-specific.
At this stage, the alloy of choice for powder for implants is titanium, which contains aluminium and vanadium, but there are some concerns regarding the toxicity of the latter two; therefore, considerable work is being undertaken to develop more biocompatible titanium alloys, which can be made using this system, Moller outlines.
Further, Mintek is undertaking work on shape memory alloys, which are also used in biomedical applications, as well as the automotive and aerospace industries.
He says the CUT is already producing 3D-printed medical implants, and Mintek “would be a major partner in this”.
The company would also support the CSIR’s work in titanium 3D printing and casting, in addition to exploring using the equipment for coating applications.
Moller says there have been some initial discussions with stakeholders in the metal coating space, such as corrosion protection, with keen interest gleaned here.
Once the equipment gains traction in the country, Mintek will explore regional partnerships, he concludes.
Comments
Press Office
Announcements
What's On
Subscribe to improve your user experience...
Option 1 (equivalent of R125 a month):
Receive a weekly copy of Creamer Media's Engineering News & Mining Weekly magazine
(print copy for those in South Africa and e-magazine for those outside of South Africa)
Receive daily email newsletters
Access to full search results
Access archive of magazine back copies
Access to Projects in Progress
Access to ONE Research Report of your choice in PDF format
Option 2 (equivalent of R375 a month):
All benefits from Option 1
PLUS
Access to Creamer Media's Research Channel Africa for ALL Research Reports, in PDF format, on various industrial and mining sectors
including Electricity; Water; Energy Transition; Hydrogen; Roads, Rail and Ports; Coal; Gold; Platinum; Battery Metals; etc.
Already a subscriber?
Forgotten your password?
Receive weekly copy of Creamer Media's Engineering News & Mining Weekly magazine (print copy for those in South Africa and e-magazine for those outside of South Africa)
➕
Recieve daily email newsletters
➕
Access to full search results
➕
Access archive of magazine back copies
➕
Access to Projects in Progress
➕
Access to ONE Research Report of your choice in PDF format
RESEARCH CHANNEL AFRICA
R4500 (equivalent of R375 a month)
SUBSCRIBEAll benefits from Option 1
➕
Access to Creamer Media's Research Channel Africa for ALL Research Reports on various industrial and mining sectors, in PDF format, including on:
Electricity
➕
Water
➕
Energy Transition
➕
Hydrogen
➕
Roads, Rail and Ports
➕
Coal
➕
Gold
➕
Platinum
➕
Battery Metals
➕
etc.
Receive all benefits from Option 1 or Option 2 delivered to numerous people at your company
➕
Multiple User names and Passwords for simultaneous log-ins
➕
Intranet integration access to all in your organisation