Production flow system helping mines to improve productivity, employee engagement
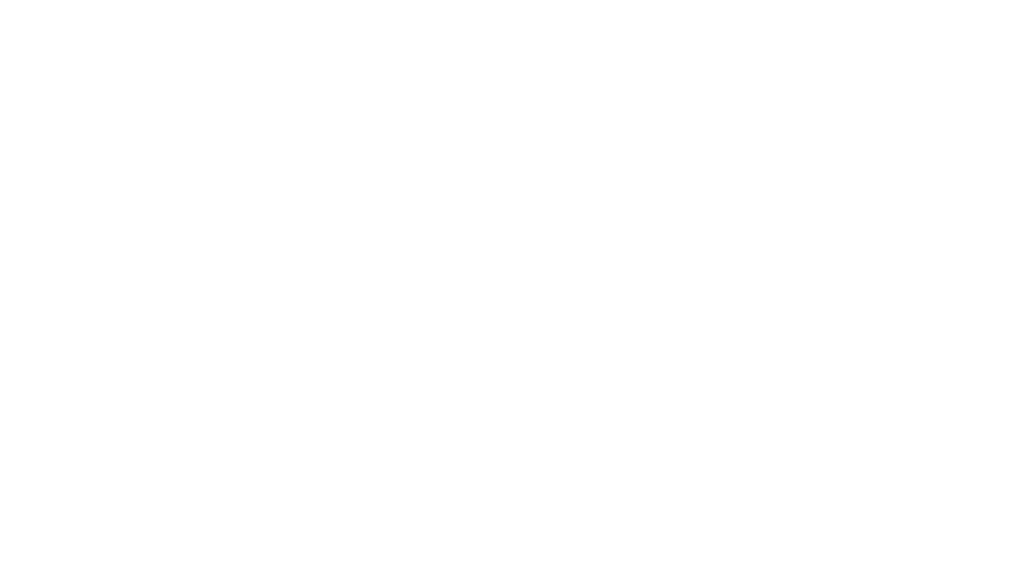
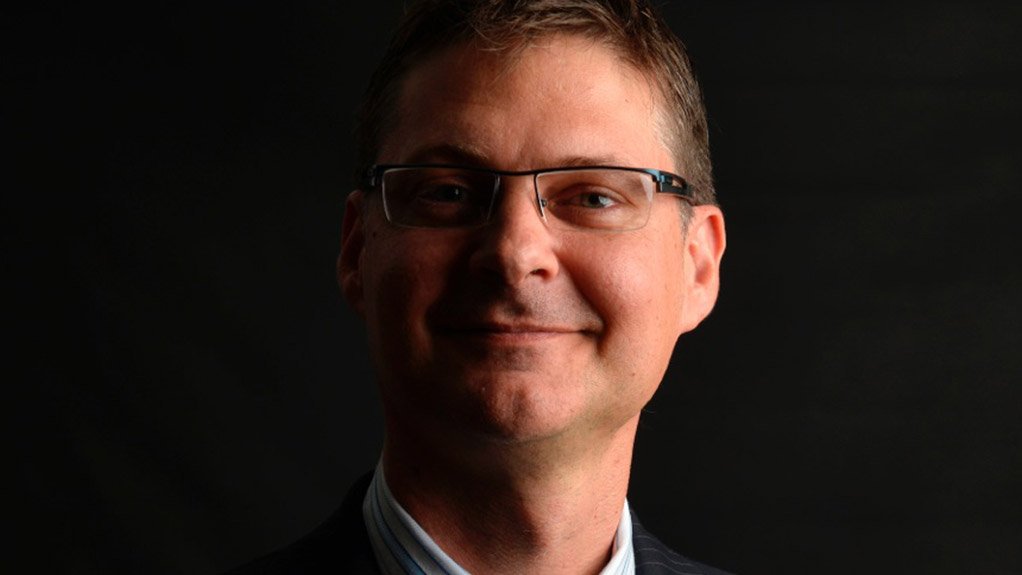
HENDRIK LOURENS Complex and complicated mining management must be approached in a suitable way, and many factors ensure that management actions taken are not suitably complex or complicated
The theory of constraints (ToC) produc- tion flow system, which is a leadership intervention, is helping mines to improve their productivity and employee engagement, says mining consultancy StratFlow CEO Hendrik Lourens.
McKinsey and Deloitte studies in the past years have shown that mining productivity is decreasing, while commodity prices are falling.
“Aggressive cost cutting over the past few years of the down cycle seems not to have been enough – often, cost per ton has actually increased and employee engagement seems to have decreased even further,” avers Lourens.
A 2013 Gallup poll showed South Africa as third last, tied with Syria, with 45% of employees actively disengaged, and a McKinsey 2015 report showed a 29% global decrease in mining productivity in the past decade.
The ToC production flow system, also called the Scrum production flow system, was developed by Tavanec CEO Arrie van Niekerk and is a leadership intervention to increase mining profitability and employee engagement in times of financial stress.
In more than 70 of the cases where the system has been implemented, production increases of between 7% and 50% have been achieved, with improvements of 20% to 40% in deep-level gold mining, 30% in chrome, 20% in platinum, 20% to 30% in copper, and 20% in gold and iron-ore opencast operations, explains Lourens, adding that, in all cases, employee engagement increased substantially.
The Scrum production flow intervention enables mine managers to manage the production processes according to systems-thinking principles, and their employees according to modern management methods. It creates a change platform for managing interdependencies and variability, which is more effective than change programmes driven by consultants.
“Having a visible production flow, we are now able to safely move decisions closer to where the work happens, and effective horizontal coordination of work becomes possible. This provides intrinsic motivation for employees, leading to better engagement.”
The buffers absorb variation and reduce intermittent flow, which stabilises production flow. This creates certainty and enables managers to manage proactively.
The principles of flow and dialogue practised in the daily Scrum production flow meeting enable managers and employees to identify the critical leverage points and focus improvement efforts there. This enables the creation of a leadership platform where managers and employees can jointly identify what is in the interest of the organi- sation and aim to effect that, leading to intrinsic motivation. In this way, the production rate increases beyond the best daily rate achieved previously.
The Cynefin Framework helps to explain the Scrum production flow intervention effectiveness by providing a perspective on the evolutionary nature of complex systems, including their inherent uncertainty. This framework divides the environment into five domains, each requiring different solutions to the problems faced.
The Cynefin Framework shows that maximum production flow – productivity – will be achieved by managing according to the principles of the complicated domain. This is the domain of systems thinking and organisational learning. In practice, many factors conspire to ensure that actions taken are best suited to the simple domain, he explains.
“By trying to control, activities vertically and by remote control through local efficiency measurements, which is legitimate good practice in the simple domain, we disempower those who best know what needs to happen. To maintain vertical control and coordination, senior and top management have to force certainty onto things that are inherently uncertain. Employee disengagement consequently increases and productivity drops.
Comments
Press Office
Announcements
What's On
Subscribe to improve your user experience...
Option 1 (equivalent of R125 a month):
Receive a weekly copy of Creamer Media's Engineering News & Mining Weekly magazine
(print copy for those in South Africa and e-magazine for those outside of South Africa)
Receive daily email newsletters
Access to full search results
Access archive of magazine back copies
Access to Projects in Progress
Access to ONE Research Report of your choice in PDF format
Option 2 (equivalent of R375 a month):
All benefits from Option 1
PLUS
Access to Creamer Media's Research Channel Africa for ALL Research Reports, in PDF format, on various industrial and mining sectors
including Electricity; Water; Energy Transition; Hydrogen; Roads, Rail and Ports; Coal; Gold; Platinum; Battery Metals; etc.
Already a subscriber?
Forgotten your password?
Receive weekly copy of Creamer Media's Engineering News & Mining Weekly magazine (print copy for those in South Africa and e-magazine for those outside of South Africa)
➕
Recieve daily email newsletters
➕
Access to full search results
➕
Access archive of magazine back copies
➕
Access to Projects in Progress
➕
Access to ONE Research Report of your choice in PDF format
RESEARCH CHANNEL AFRICA
R4500 (equivalent of R375 a month)
SUBSCRIBEAll benefits from Option 1
➕
Access to Creamer Media's Research Channel Africa for ALL Research Reports on various industrial and mining sectors, in PDF format, including on:
Electricity
➕
Water
➕
Energy Transition
➕
Hydrogen
➕
Roads, Rail and Ports
➕
Coal
➕
Gold
➕
Platinum
➕
Battery Metals
➕
etc.
Receive all benefits from Option 1 or Option 2 delivered to numerous people at your company
➕
Multiple User names and Passwords for simultaneous log-ins
➕
Intranet integration access to all in your organisation