Hard rock no match for MMD sizer
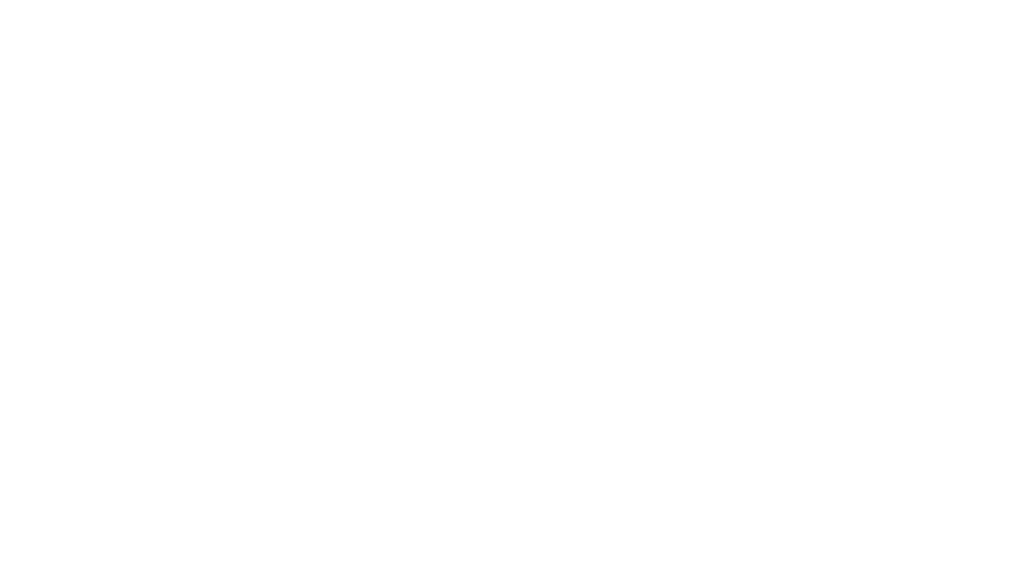
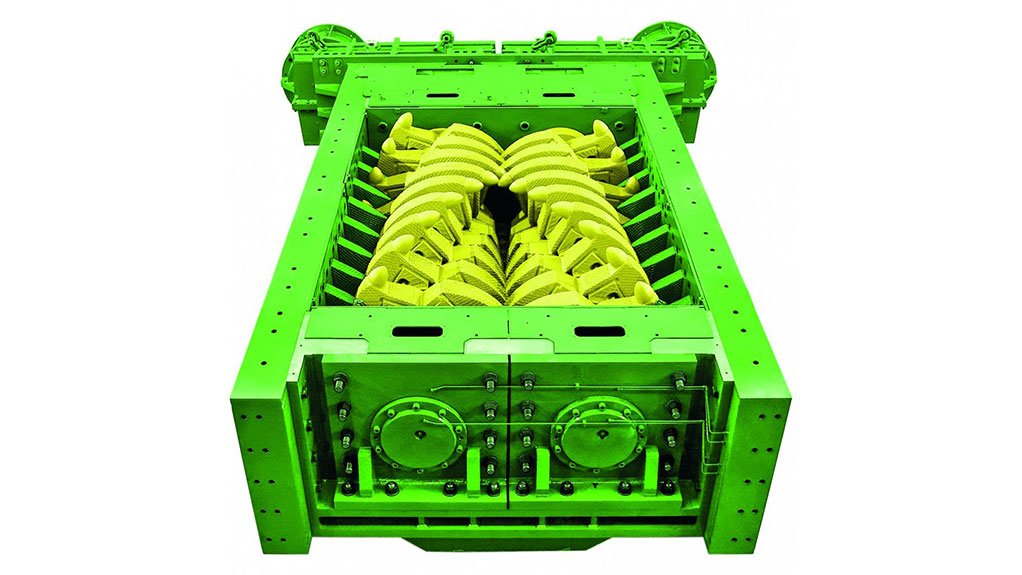
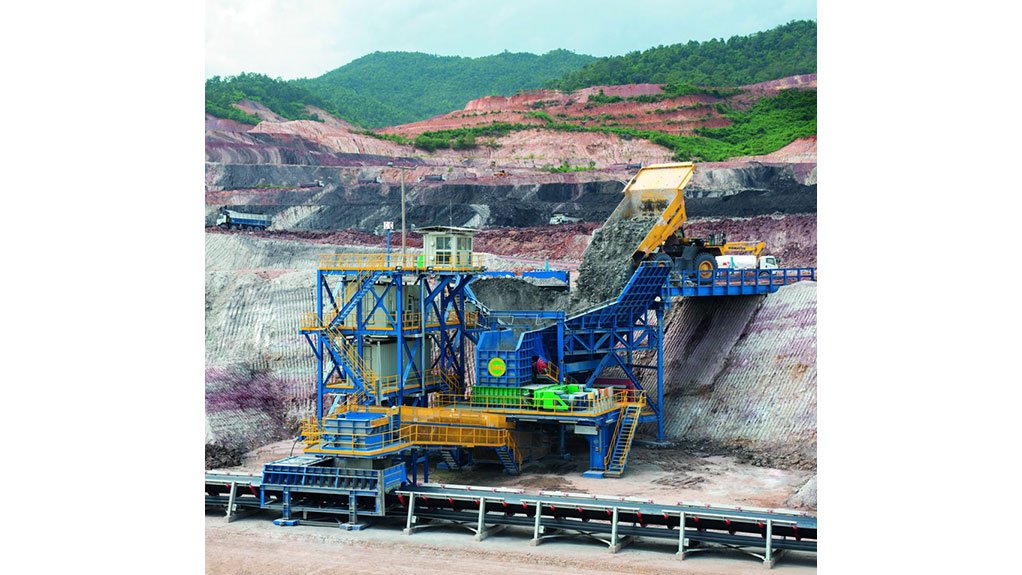
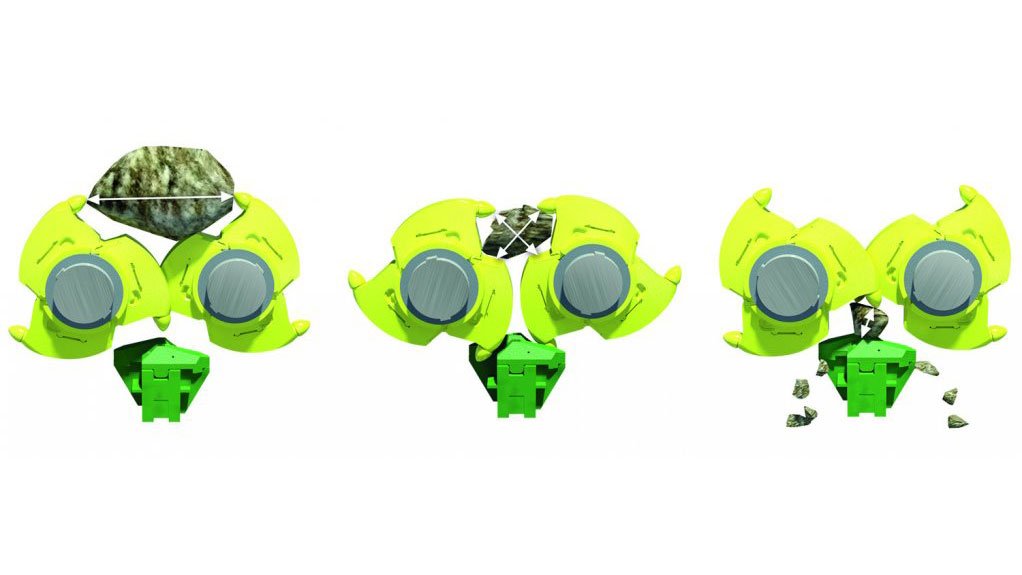
ROCK MUNCHER The twin-shaft mineral sizer is tough enough to handle any material – from soft coal right through to hard granite.
SEMI MOBILE The sizers generally only require a simple pontoon base, rather than a costly foundation and civil infrastructure.
ONE, TWO, THREE The sizer’s three stages of breaking provide the ability to control the product size in all three dimensions, while minimising the generation of dust and fine material.
The story of MMD Mineral Sizing began in the UK in the 1980s, when the mineral processing solutions company started marketing its innovation – a twin-shaft mineral sizer – to the underground coal mining industry. Fast-forward 40 years and MMD’s mineral reduction technology can be found in more than 70 countries, processing over 80 different materials.
As sizers originated in the coal industry, some believe that the technology is only suitable for soft material processing. This is simply not the case for MMD sizers, says business development manager Mark Peeters.
He states that MMD sizers produce a good-shaped product with minimal fines, while also being compact, energy-efficient and maintenance friendly, making it an appealing option for hard materials handling.
“Our dedicated in-house technical development team has provided consistent research and development since the sizer’s inception in 1980, and enabled MMD’s machines to operate successfully in a variety of industries, processing some materials rated over 250 MPa.
“From the sizer teeth design through to the drivetrain, the progress of these specialist heavy-duty sizers has taken many years of careful development and features a range of adaptations to allow them to handle harder rock,” Peeters says.
Specialist Hard Rock Designs
Sizer teeth designed for hard rock and highly abrasive applications are engineered from upgraded material to resist wear, with additional hard facing in high impact areas. The tooth designs themselves are bulkier to ensure maximum longevity between wear component changeouts.
Peeters notes that MMD is constantly developing new tooth designs, using a combination of theoretical and physical stress testing to find ways to improve wear components. The extra forces necessary to break harder material also require larger shaft diameters and heavy-duty bearings.
Another key feature throughout MMD’s range of sizers is the use of in-house designed gearboxes. Using only the highest-quality manufacturing processes, materials and components guarantees that the gearboxes can deal with the unique stresses inherent in sizing hard rock.
Each machine goes through stringent design procedures to ensure top quality. The in-house technical division provides simulations and analysis using the latest industry software. In some instances, physical trials will be carried out to test the material.
MMD offers turnkey solutions in the form of semi-mobile and fully mobile sizer stations. The lightweight nature and balanced breaking action of the sizer means that an MMD semi-mobile sizer station for hard rock applications generally only requires a simple pontoon base, rather than costly heavy-duty foundation and civil infrastructure.
However, ancillary structures still require some adaptation to match up with the impact forces generated in hard rock applications, Peeters says. For example, a fully fabricated one-piece hopper hood, with a wear-resistant skin rather than wear liners, reduces the risk of liners falling off, owing to high impacts. The skin is replicated on the hopper itself, along with a T-shaped lattice design in the impact area to combat high impacts from the truck dump.
“Adaptations such as these ensure MMD machines are designed to endure the harsh mining environment and are built to last,” he states.
Hard rock inclusions can be mixed with wet and sticky material without any major alteration to the sizer design or detriment to performance.
“Where some conventional crushers struggle to cope with sticky material, the space between sizer teeth and the constant agitation of material within the machine prevents material build-up, this can be further enhanced, where necessary, by adding side cleaning combs. Ultimately, MMD sizers can handle any combination of wet, sticky, hard or abrasive material,” says Peeters.
This is useful in climates where extremes of rainfall occur throughout the seasons, affecting the characteristics of the material being processed or where material types vary across the mine site.
Hall 5 Stand B19
Comments
Press Office
Announcements
What's On
Subscribe to improve your user experience...
Option 1 (equivalent of R125 a month):
Receive a weekly copy of Creamer Media's Engineering News & Mining Weekly magazine
(print copy for those in South Africa and e-magazine for those outside of South Africa)
Receive daily email newsletters
Access to full search results
Access archive of magazine back copies
Access to Projects in Progress
Access to ONE Research Report of your choice in PDF format
Option 2 (equivalent of R375 a month):
All benefits from Option 1
PLUS
Access to Creamer Media's Research Channel Africa for ALL Research Reports, in PDF format, on various industrial and mining sectors
including Electricity; Water; Energy Transition; Hydrogen; Roads, Rail and Ports; Coal; Gold; Platinum; Battery Metals; etc.
Already a subscriber?
Forgotten your password?
Receive weekly copy of Creamer Media's Engineering News & Mining Weekly magazine (print copy for those in South Africa and e-magazine for those outside of South Africa)
➕
Recieve daily email newsletters
➕
Access to full search results
➕
Access archive of magazine back copies
➕
Access to Projects in Progress
➕
Access to ONE Research Report of your choice in PDF format
RESEARCH CHANNEL AFRICA
R4500 (equivalent of R375 a month)
SUBSCRIBEAll benefits from Option 1
➕
Access to Creamer Media's Research Channel Africa for ALL Research Reports on various industrial and mining sectors, in PDF format, including on:
Electricity
➕
Water
➕
Energy Transition
➕
Hydrogen
➕
Roads, Rail and Ports
➕
Coal
➕
Gold
➕
Platinum
➕
Battery Metals
➕
etc.
Receive all benefits from Option 1 or Option 2 delivered to numerous people at your company
➕
Multiple User names and Passwords for simultaneous log-ins
➕
Intranet integration access to all in your organisation