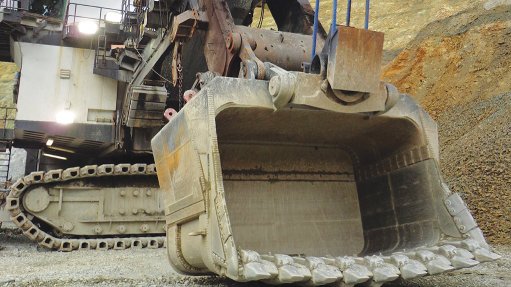
Every time a piece of rock impacts or moves across a metal surface, it removes small pieces from this surface, resulting in wear. Even though this wear is very small, the volume loss of these shavings adds up over time and has a direct impact on operational costs.
For this reason, Benoni-based engineered wear-protection solutions manufacturer Welding Alloys South Africa (WASA) says it is vital to use materials and solutions offering the best possible wear resistance.
WASA’s Hardplate™ range of wear-resistant materials comprise extremely hard, abrasion-resistant chromium and complex carbide materials which are welded onto a mild steel backing plate.
Produced in South Africa, in accordance with the standards of its parent company, Welding Alloys Group, these materials have proven over a 50-year task to outlast 500 Brinell quenched and tempered (Q&T) steels by between five and 12 times, depending on the application.
Hardplate™ products can save time and money in a typical 5:1 wear rate ratio, compared with Brinell 500 Q&T products. Where Brinell 500 Q&T would cost material, labour and downtime from initial installation through to maintenance cycle five, Hardplate™ products provide cost saving and require no intervention during maintenance cycle one to four.
WASA’s materials, solutions and expertise are hard at work across the globe in some of the most demanding applications known to man and include truck tray liners, chutes and hoppers, loader buckets, liner plates, transportation equipment, impact zones, storage bins and crusher plants.