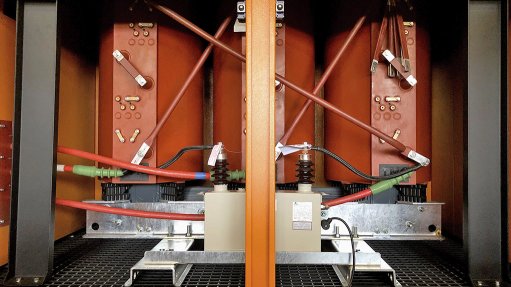
A mini substation featuring a 1250 kVA dry-type transformer built for a coal mine project
As mines aggressively pursue Zero Harm policies while seeking greater productivity and efficiency, dry-type transformers have much to offer, specialist company Trafo Power Solutions is seeing a substantial take up of this technology over traditional oil-filled transformers, with mines recognising the no-compromise benefits.
The priority area of mining today is certainly health and safety, and mines are wanting to achieve this without compromising on meeting their production targets; dry-type transformers are increasingly seen as one constructive way of doing this.
Trafo Power Solutions MD David Claassen says this is because of their F1 safety rating, combined with their low maintenance needs and versatility across mining applications. Their fire safety characteristics include being self-extinguishing and flame retardant, and not emitting harmful gasses.
“Dry-type transformers contain no oil as a coolant, rather using air for cooling,” says Claassen. “This means a much lower safety and environmental risk, so that these units can be readily and safely employed in opencast and underground mines – even in hazardous and space-constrained areas.”
Trafo Power Solutions’ design capability ensures that its transformers can run optimally in even harsh conditions of high dust and moisture levels, while remaining sufficiently cool to reliably carry 100% load. The necessary levels of ingress protection are applied to ensure no dust or moisture enters the unit. This includes working with challenging commodities like coal and graphite.
“To accommodate the space and transport limitations of underground mines, we custom engineer transformers to fit into lift cages in vertical shafts or into decline shafts,” he says, adding that the company’s fit-for-purpose designs also ensure that the transformers can be installed with limited footprints in confined spaces.
Cooling options where the transformer’s footprint is reduced include air-to-air heat exchangers, while for more extreme conditions the company can design and manufacture water-cooled transformers. For opencast mining operations, there is often a requirement for transformers to be moved regularly on skid-mounted platforms.
“This means ensuring a high structural integrity through rigid construction, so that the units can withstand vibration as they are frequently moved over rough terrain,” he says. “Under these conditions, mines can also rest easy that there is no risk of oil leaks from our units.”
He explains that Trafo Power Solutions conduct in-depth analyses of mine applications and conditions to inform its designs. Strategic partner TMC Transformers – a leading transformer manufacturer based in Italy – uses the latest thermo-dynamic software to simulate cooling across the transformers’ hotspots. Cooling options include natural ventilation and forced ventilation, with availability of air-to-air heat exchangers and auto heat exchangers.
“Mines can gain immediate safety benefits from dry-type transformers, while improving their operational uptime,” says Claassen. “With no oil to regularly check and change, our transformers are almost maintenance-free – cutting down on service costs and the related impacts of transformer downtime.”
Partnering with TMC Transformers, Trafo Power Solutions has access to a broad range of high quality cast resin transformers from 50kVA to 25MVA, at system voltages up to 52kV with Class F or Class H insulation systems.