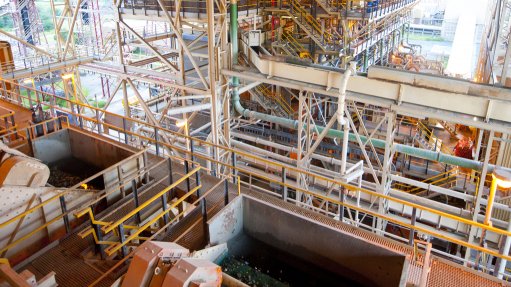
THROUGHPUT ENHANCEMENT Mines need to re-evaluate and enhance their processing operations to achieve the desired efficiencies and increased throughput
As the local mining sector faces increasing cost pressures across the entire mine supply chain, it is becoming increasingly important to enhance throughput during processing, where ore is effectively turned into saleable commodities.
“With cost pressures mounting on a daily basis, it pays mines to enhance plant efficiency and gain the maximum profit from processing operations,” says industrial components and solutions provider Tega Industries South Africa (SA) national sales manager Kirby Vermaak.
To achieve the desired efficiencies and increased throughput, mines need to re-evaluate their processing operations and, where possible, enhance existing infrastructure to eliminate bottlenecks and tackle equipment reliability issues, stresses Vermaak.
He and his team of engineers and process specialists encounter serious design flaws and avoidable bottlenecks on mine processing plants on a daily basis. In most instances, solutions are surprisingly simple and engineered solutions can be easily applied to resolve the problems and restore the plant to operate at full capacity, he says.
Eliminating Backlogs
“Tega Industries SA often undertakes studies of plants where workers have grown accustomed to simply ‘dealing’ with problems, rather than addressing the issues and sorting them out. For example, if a chute gets blocked, workers simply use a crowbar and remove build-up by hand while the plant stands idle. This type of problem management is commonplace at some mines and has significant implications for mine productivity ,” Vermaak points out.
For this reason, the company prefers to work with its customers to help identify process snags and find solutions in the form of high-tech linings and other specially engineered products that can be tailor-made for clients’ unique requirements.
Although plants have been designed and built by a specialist original-equipment manufacturer (OEM), Vermaak believes that customers need not slavishly use these OEMs’ solutions.
“In many instances, new materials have become available that can radically improve the performance of such plants. If the OEM does not supply these products, they will . . . supply customers with the old products forever,” Vermaak says.
Screening Efficiency
Vermaak further highlights that, in most instances, material flow problems are caused by inefficient screening of materials, or incorrectly specified linings. “Screens play a significant role in allowing only workable materials to enter the process and should exclude items that are too large or that can damage equipment, such as with crushers or cyclones,” Vermaak says, adding that rubber scalping panels, for example, remove oversize rocks from crushing and screening processes and can also play a significant role in the effective operation of a plant and contribute positively to its overall throughput.
“Yet, optimisation of this critical element is often overlooked in favour of other more visible aspects of a plant, which often call for more costly screening techniques or even capital equipment upgrades. “However, by removing choking rock debris from entering the process, many issues can be avoided and process times dramatically improved.”
Vermaak further points out that equipment lining needs to keep materials flowing at a con-stant pace throughout the plant.