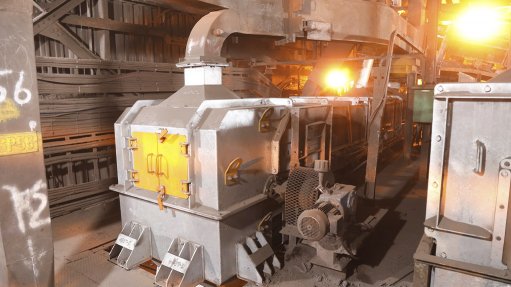
A conveyor onto conveyor transfer chute installed at a local steel plant
It has been another good year for transfer chute specialist Weba Chute Systems, and signs are that it will get even better.
While demand from the mining industry can be volatile, the company has developed a solid pipeline of projects – not only in southern Africa but also abroad. Mark Baller, CEO of Weba Chute Systems, is expecting 2024 to get busier, and believes that this trend will continue into 2025.
“As customers recognise the value of custom-engineered transfer points in their mines and plants, we have seen demand grow in various regions,” says Baller. “There are good prospects in countries like the Democratic Republic of Congo – where copper and cobalt mining is strengthening – and in platinum prospects in Zimbabwe, for instance.”
He notes that Weba Chute Systems has for many years been active in overseas markets, and is looking forward to fulfilling some large foreign projects. The company expects to supply a large package of about 50 chutes to a project in the US, and a gold mine expansion in Turkey will be supplied with up to eight custom engineered Weba chutes.
“We continue to attract new customers who have heard about our specialised solutions, and who approach us with specific challenges they are trying to overcome,” he says. “We have had interesting engagements recently with companies operating in Jordan and Saudi Arabia – which promise to extend our reach beyond traditional markets.”
Closer to home, Weba Chute Systems has continued to design and deliver substantial projects for Southern African customers. In South Africa, the company manufactured and installed 32 bespoke chutes for a steel plant. Through a leading EPCM company, it also supplied 10 large chutes to a platinum mine in Zimbabwe – to handle large run-of-mine material.
“An expansion project at a local manganese producer has requested our services, so we have completed the engineering design for nine chutes and will soon begin the manufacturing process,” he says. “We have also been designing and delivering multiple chutes to three diamond mines in Botswana, and this will continue into next year.”
Baller highlights that the company has remained resilient to production disruptions such as loadshedding by the national utility in South Africa. As the owner of its design and manufacturing facility in Wadeville, south of Johannesburg, Weba Chute Systems has invested extensively in both renewable energy and backup power. This allows the facility to continue work uninterrupted, to meet customers’ deadline requirements without compromising quality. Its on-site solar power installation also assists in mitigating the rising cost of energy.
“By carefully managing our work environment and ensuring that all phases are fully resourced with the latest technology, Weba Chute Systems can deliver cost effective solutions that are tailored to each specific transfer point,” he explains. “For foreign contracts, we often have a cost advantage by conducting the design and manufacturing work in South Africa. At the same time, the value of our solutions is really measured by the extra production our customers achieve by optimising uptime through our high quality, engineered chutes.”