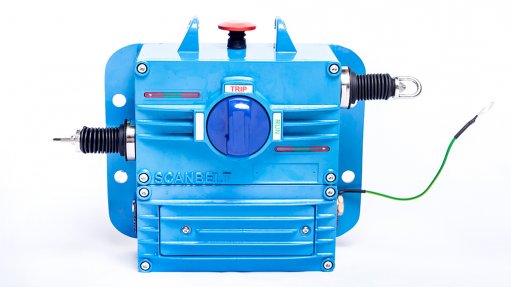
EVOLVING FEATURES Electrotron continues to improve its systems to meet customer needs
Conveyor materials handling original-equipment-manufacturer Electrotron’s ScanBelt suite of conveyor belt protection systems helps to improve safety and efficiency while decreasing downtime and damage to machinery.
The range comprises monitoring and safety systems designed in accordance with various health and safety regulations, as well as requirements that ensure moving machinery is adequately protected to prevent, for example, personal injury, says Electrotron chief of operations Shane Thompson.
Occupational health and safety regulations require certified safety systems to be adequately commissioned and regularly checked, whereby mines can be prevented from operating until the infringing conveyor safety standards have been adhered to.
Therefore, mines require monitoring and safety systems that are aligned with regulations and that can assist mines in maintaining compliance.
Compliance requires safety mechanisms, such as tripping mechanisms, to make equipment safe in the event of a fault and misalignment of the conveyor belts. Further, the belt speeds need to be monitored for prevention of slip.
Additionally, operational considerations such as fire-detection systems on conveyors, rip detection, audible and visual prestart warnings, must all be maintained and the central control room requires this information for operation and control purposes.
Electrotron’s ScanBelt automated systems simplify these safety processes and ensure a user-friendly means of reporting the systems for automated planned maintenance.
Intelligent, automated safety systems, such as the ScanBelt range, are a complete safety and management solution for conveyor systems, Thompson adds.
Evolving Features
Electrotron introduced the ScanBelt range in 2008 and continues to improve the systems based on customer feedback, emerging trends and amendments in associated regulatory requirements.
Thompson explains that the company’s 40 years of experience in the industry ensure that Electrotron’s customers get significant value from the equipment range and can, in turn, improve the efficiency and safety of their operations on site.
In the past year, Electrotron has introduced speed and mechanical misalignment detectors, as well as complete conveyor prestart process systems that do not require additional wiring or junction boxes.
The ScanBelt suite also incorporates fire-detection systems – compliant with recent amendments to the Mine Health and Safety Act.
“We ensured that our systems can actually incorporate fire-detection systems and went further by bringing in other inputs and outputs, where we can control or bring in information, which doesn’t now require additional cabling,” says Thompson.
The system also offers down-the-line powered circuitry and single-cable source compatibility.
Additionally, ScanBelt conveyor belt pull-key trip mechanisms can be installed up to 100 m apart, which makes the pull-keys more cost effective in the long term and ensures that the conveyor system is more user friendly.
Product Range
ScanBelt further ensures safety by indicating the last time and date any particular conveyor component was tripped and checked by an inspector.
Thompson explains that the system’s register-generated data cannot be overridden and requires that a worker physically engages with the system when faults are logged and the ScanBelt system then reports the interaction to a central database.
The database generated by ScanBelt then shows that the conveyor has been adequately inspected, also reflecting the number of times it should have been checked, which consequently provides a better indication of its compliance. When captured correctly, such data can help inform safety reports.
Mines can then present the resulting report from the database to the Department of Mineral Resources and Energy to help show the associated mine and its systems are compliant.
Meanwhile, Electrotron’s ScanBelt conveyor belt tear alignment detector system can monitor the alignment of a conveyor belt by measuring the horizontal drift of a conveyor belt and report any deviation from its trained position.
The alignment detector does not make any contact with the conveyor belt when the conveyor belt is operating within its limits but, if the conveyor belt misaligns beyond its allowable drift limit, the edge of the conveyor belt will make contact with striker rollers, which activates a trip mechanism.
The unit is factory setup to warn or trip when the striker rollers move 18 ° from the trained position and trip at 30 °, thereby improving operability, the meeting of operational parameters and overall efficiency.