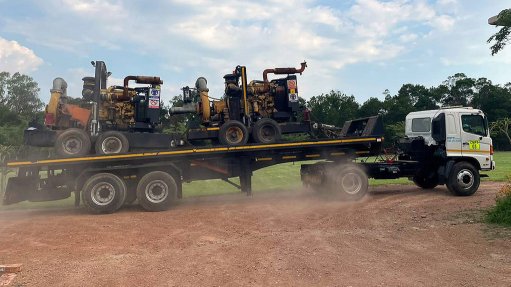
TAKING DELIVERY Mechanical Rotating Solutions received multiple mobile pump units for refurbishment last month
South Africa’s electricity crisis has made it more evident than ever that maintenance and planning should form the core of any industrial operation, says mining supplies company Mechanical Rotating Solutions (MRS).
Many mining companies strive to improve the reliability of their operations, but this becomes more difficult in a time of continuous deep cost cutting. While many see maintenance as a cost, lessons learnt from State-owned power utility Eskom should make it clear that just maintaining equipment is a futile exercise as technology and processes advance over time and maintaining old equipment is a recipe for even greater expenditure in the long run.
MRS claims it has proven, over the last decade, that maintenance and proper planning can be a cost-cutting exercise if done right by using the right business partner and the latest product offerings available.
“Our philosophy has always been never to accept ‘good enough’. In reality, to offer a client a product that is ‘good enough’ to facilitate cost cutting, is not only undercutting the industry but creating continuous breakdown issues and most probably a strained relationship with the client over time,” says MRS CEO Franscois Steenkamp.
The use of gland packing instead of mechanical seals when sealing a pump to prevent fluid loss is one of the most frequently used cost-cutting measures at mining operations. By using gland packing, or a mechanical seal, the rotating shaft can enter the wet area of the pump without the pressurised fluid in the pump escaping.
“Often our clients would ask why use mechanical seals when gland packing is considerably cheaper and shows an immediate cost saving on the maintenance account. While many clients still use traditional methods of sealing, such as gland packing, as a considered cost-effective solution, the truth is that this traditional way of sealing a pump will cost more over the long term as a direct result of premature pump failure, increased leakage, higher energy use and shaft sleeve damage,” explains Steenkamp.
He adds that because the gland packing is in constant contact with the pump shaft sleeve it will cause threading and that will require a considerable amount of money to repair or replace.
“We advise our clients on the advantages and disadvantages of using mechanical seals over traditional seals and try to help them make the right decision to suit their needs.”
Correctly adjusted gland packing should be maintained with a leakage rate of about one drop a minute of sealed product per 25 mm of the outside diameter of the shaft. On a 50-mm-diameter shaft this equates to two drops a minute, 450 ℓ a month or 5 400 ℓ/y. Based on these figures, return on investment in an advanced mechanical seal would be realised in around six months.
Correctly designed, specified and fitted mechanical seals have no visible leakage and, therefore, no product loss.
After a calculation revealed that 24 service pumps at a Limpopo platinum mine were losing in excess of 252 000 ℓ/y of water, MRS stepped in and replaced the existing pump gland packing with AESSEAL single cartridge seals ensuring a lasting solution to undue wastage of water – South Africa’s most valuable resource.
By replacing the conventional stuffing box gland packing of the client’s original-equipment manufacturer slurry pumps with AESSEAL single monolithic stationary seals, MRS has not only addressed the excessive water loss, but also improved the reliability and efficiency of its client’s plant.
Further, MRS received delivery of multiple mobile pump units for refurbishment last month.
“The mobile pump units will be completely stripped and rebuilt to our specification ensuring the best quality possible for our clients,” says Steenkamp.
Apart from refurbishing mobile dewatering units for its clients, MRS launched its own mobile dewatering unit in 2017. The unit was designed using the best pump selection for its customers’ needs and includes a heavy-duty double axel with agricultural wheels to significantly reduce the risk of power hopping and soil compaction.
The MRS mobile pump set is not only capable of controlling in-pit water levels, but can also be stored in proximity to the operations, increasing productivity while drastically reducing transport costs.
To be optimally productive, while also keeping an eye on the cost of a dewatering solution, mines should constantly monitor the water level and procure the most cost-effective solution possible that can be rapidly deployed and stored on site.
“In a short period, we have managed to establish ourselves as the go-to company for the refurbishment and upgrading of existing mobile pump units. Incorporating this niche with our mobile rental unit business is definitely seen as an area of growth for the company this year,” states Steenkamp.