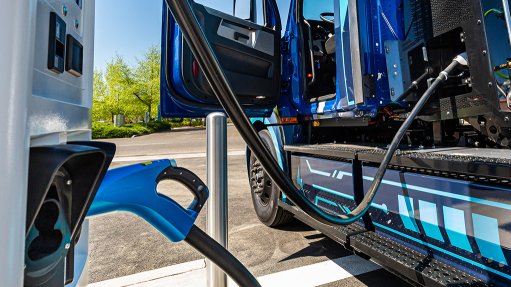
FUELING THE FUTURE Miners can create zero-emission mobile equipment through a combination of EVs and alternative fuels
Mining operations are energy intensive, with energy representing one of the sector’s biggest operational costs. Fossil fuels remain the primary feedstock, which leaves miners exposed to volatile gas, oil and coal prices.
Consequently, an overarching challenge is decarbonisation, explains construction and engineering firm Black & Veatch South Africa sub-Saharan Africa regional director Joseph Mahendran.
Miners recognise the need to decarbonise operations as part of global efforts to mitigate the causes and effects of climate change. Currently, mining is responsible for 4% to 7% of greenhouse-gas (GHG) emissions globally.
Further, the sector is under increasing pressure from governments, investors, and society to reduce emissions, while operating licences may be at risk for companies that do not sufficiently reduce their carbon emissions.
In October 2021, industry organisation International Council on Mining and Metals members committed to net-zero Scope 1 emissions, which refers to direct emissions, and Scope 2 emissions, which refers to indirect emissions, by 2050.
Mahendran remarks that, although decarbonisation is the end-goal, there is “no one-size-fits-all approach”. Miners have multiple options, as well as a suite of technologies, to choose from, which they integrate in accordance with their operational needs and specifications.
Firstly, mines can integrate more renewable energy into their operations. This has primarily been through green power purchase agreements for grid-connected mines and the creation of on-site renewable-energy infrastructure at remote mines globally.
For activities, such as smelting, which require high temperatures, green hydrogen can serve as a feedstock to replace coal and natural gas. Currently, green hydrogen is the only way of reaching the temperatures required for smelting in a low-carbon manner.
“When burning in air, hydrogen can hit 2 000 °C to 2 100 °C, similar to natural gas at about 1 950 °C. When mixed with oxygen to create oxyhydrogen, maximum temperatures can reach 2 800 °C,” explains Mahendran.
Improvements in operational efficiency can also reduce GHG emissions by reducing overall energy consumption. Efficiency solutions can range from digitalisation of operations for better management of energy usage to a focus on more efficient equipment that can deliver longer-term savings in the form of reduced energy consumption.
Further, water and wastewater treatment and water carriage systems require significant power, but comprehensive water management plans can reduce levels of consumption, treatment and carriage.
Reducing evaporation, leaks and waste, in addition to other water management methods, will reduce energy requirements and related GHG emissions, adds Mahendran.
Miners can also create a zero-emissions mobile equipment fleet by using a combination of electric vehicles, hydrogen fuel cell electric vehicles, or bio- or synfuels.
The on-site generation of power using renewables can help miners achieve carbon reduction targets by placing miners in direct control of their emissions and other environmental impacts.
On-site renewable energy can reduce emissions through powering mine processes, charging batteries or powering electrolysis to create hydrogen for use in zero-emission mobile equipment.
On-site generation using renewables can also reduce long-term operational costs and help to protect mining operations against unreliable grid supply.
Combined Efforts
While Mahendran acknowledges that no single activity will achieve net-zero mining, he explains that a combination of efforts or methods can be adopted to get closer to net-zero mining. Concrete steps need to be planned and integrated as part of a decarbonisation roadmap, he says.
The quality of miners’ initial strategic decarbonisation roadmaps has the most significant impact on their net-zero investments and ability to compete and thrive in a decarbonised future.
Mahendran adds that decarbonisation can potentially take up to 30 years. Therefore, the roadmap needs to identify easily achievable tasks, factor in uncertainty and include scope for adaptability.
It also needs to incorporate commercially ready and emerging technologies that will become available over the next 30 years.
This requires the technical competence and in-depth knowledge to identify technology timelines, cost curves and resiliency characteristics, as well as the prioritising of technologies across multiple factors such as cost and returns, risk, availability and opportunity to scale.
Decarbonisation programmes at all levels require an understanding of how legacy, new and soon-to-emerge technologies can work together. A decarbonisation strategic roadmap needs to have a detailed technology core, explains Mahendran.
He stresses the importance of establishing decarbonisation technologies that are best suited to delivering a miner’s decarbonisation goals. This is also dependent on factors such as developing an understanding of organisational change and the relevant regulatory landscape.
“None of these elements in isolation will give rise to an effective strategic decarbonisation roadmap; integration is essential,” Mahendran concludes.