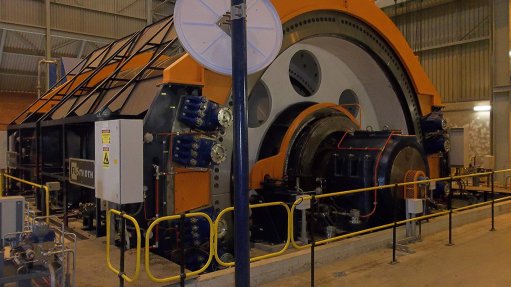
HEAVY DUTY Blair Multi-Rope winders are used for raising and lowering conveyances during mining operations
Engineering group FLSmidth will next year deliver two Blair multi- rope (BMR) winders for raising and lowering conveyances during mining operations to new mine shafts, owned by diversified mining major Glencore, in Zambia.
FLSmidth sales manager for mine shaft systems in South Africa Wendy Norman tells Mining Weekly that the BMR winders will be installed at the Nkana mine’s Mindola shaft, in Kitwe, and the Mufulira mine’s Mufulira shaft, 25 km north of Kitwe.
“This is the highest-value order that FLSmidth’s mine shaft systems business has received for BMR winders to date. The company has installed more than 90% of the world’s BMR winders and has been actively involved in the development of the winders since the first installation in 1959,” she says.
FLSmidth will begin delivering the equipment to the new mine shafts in the last quarter of 2015, with installation likely to start in 2016.
Norman adds that, these two installations increase the number of BMR winders currently operating in the Zambian mining industry to five – all of which have been installed by FLSmidth. “With only about 50 BMR winders of this kind operating in the world, it is gratifying to have been responsible for adding another five in this country, whereas, two years ago, there were none.”
FLSmidth will supply identical equipment for both shafts, including a double-drum BMR rock winder and a single-drum BMR man-and-materials winder. “The drums are almost identical for both winders, each measuring 5.7 m in diameter, with two 1.8-m-wide rope compartments,” she explains.
The company will also supply a Hooke’s joint application, which, says Norman, is unique for these winders. This is only the second time – and the first in Zambia – that a Hooke’s joint will be used for a mine-hoisting system on the African continent.
“The Hooke’s joint is a giant universal coupling used on double-drum BMR winders to link the two drums mechanically, without the use of gears, to allow for the drums to be angled towards the conveyance centres, which improves rope fleeting angles,” explains Norman.
She adds that, at the Mindola and Mufulira mine shafts, the Hooke’s joint will allow for the wide BMR drums to be installed at an angle of 12° to each other, accommodating the drum centres without incurring any fleeting angle problems.
“This system offers significant capital cost savings that beats the price of electrically coupled winders. Further, the cost of a BMR installation is offset by the higher tonnages that can be hoisted using twin ropes per conveyance.”
Norman tells Mining Weekly that FLSmidth installed the first Hooke’s joint application in the early 2000s, at a gold mine in Westonaria, west of Gauteng.
The drum shafts will be manufactured in South Africa and, after a trial assembly, the equipment will be dismantled and transported to Zambia.
“All the equipment for this installation will be sent to the mine sites in a strict sequence,” she says, adding that the total weight of the components that will be transported by road is about 3 000 t, including electrical equipment such as transformers.