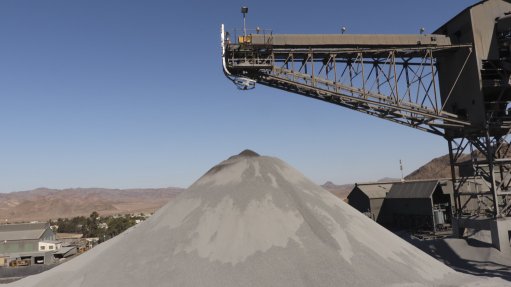
SIMPLIFYING MAINTENANCE I-CAT’s retractable stockpile dust ring makes the dust-suppression system easy to access for maintenance
Environmental management solutions provider I-CAT this year introduced a retractable stockpile dust ring (R-SDR) for dust suppression at conveyor discharge points, which can be fully automated and allows for easy maintenance.
I-CAT technical manager Morne van Wyk explains that comprehensively controlling the dust generated when discharging mining material from conveyor chutes onto stockpiles, which is then transported to processing plants or ports, has been a long-standing challenge in the mining industry. Performing maintenance makes it doubly challenging, owing to the difficulty of accessing any dust-suppression system that is attached to the discharge chute of a conveyor, as it is typically at a height of between 3 m and 22 m.
Van Wyk points out that, traditionally, accessing the system for maintenance purposes first requires the stockpile to be cleared away, allowing for the chute to be accessed by a crane or a cherry picker – a time-consuming and expensive process.
Dust-suppression systems – comprising stainless steel misting rings with nozzles – are commonly fitted at the bottom of the chute to spray a curtain of fine mist around the material being discharged.
I-CAT’s R-SDR is, however, unique in its ability to retract, says Van Wyk. The system can be winched down from the discharge chute, either electronically or manually, allowing for maintenance to be carried out easily and much more cost effectively. “What used to be a two- or three-day exercise to perform maintenance can now be carried out within an hour,” he points out.
The R-SDR can also be fully automated. In such a case, I-CAT installs a tank and pump system with a filtration system and programmable logic controller (PLC), which keeps the line to the nozzles in the R-SDR pressurised.
Van Wyk explains that the PLC is programmed to receive two input signals. The first signal comes from a belt-run switch and indicates whether the conveyor is operational, while a product sensor that is placed above the conveyor belt transmits the second signal. If the PLC receives both signals, indicating the conveyor is running and product is being transported, the R-SDR is activated and mist is sprayed onto the product being discharged onto the stockpile. If one or neither signal is received, the system stops automatically and switches to standby mode.
Engineered to industrial strength and longevity, the R-SDR is customisable, with various nozzle types and sizes available, Van Wyk notes. Besides being easy to access, install and maintain, the dust-suppression system also offers lower water use than other similar products and can be equipped with a two-way valve to provide manual control over water flow. A water filter can be added when using nonpotable water, as can a booster pump if there is a need for increased water flow and pressure.
“The policing of environmental and health and safety regulations at mines has increased greatly over the past few years. The R-SDR can help companies comply with these regulations while reducing costs and simplifying the operation and maintenance of the system,” Van Wyk concludes.