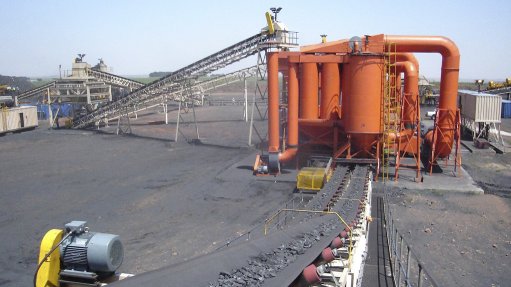
FGX DRY-PROCESSING UNIT A layer of coal is subjected to a high-frequency vibration to separate coal from stone
The Coaltech Research Association plans to further evaluate a new, dry dense-medium separation (DMS) process later this year at a pilot plant at a coal mine in Witbank.
Since mid-2015, Coaltech has been investigating the new process commercialised by electricity and coking company Shenzhou in China in 2012.
A preliminary evaluation of this process was done by heavy mining minerals company Exxaro Resources, a Coaltech member. Exxaro tested whether this process was effective and also whether it could be used for South African coal. The evaluation of the Chinese test results was positive.
The process employs the same principle as conventional DMS, but uses a dry magnetite medium, fluidised by air and not water, explains research and development organisation Council for Scientific and Industrial Research (CSIR) coal specialist Johan de Korte.
The process allows for sharp separations at low relative densities and potentially offers a more effective dry beneficiation process; it can also potentially produce export-quality coal.
Dry Beneficiation
Coal mining in arid regions has led to calls for research in the field of dry beneficiation because it offers not only lower water requirements but also lower operating and plant costs, notes De Korte.
“A foreseeable conflict is brewing in South Africa between industry, agriculture and the local populace, as they compete for scarce water resources. The traditional wet separation process requires about 500 ℓ of water for every 1 t of coal, compared with dry beneficiation that requires no water,” says De Korte.
Eliminating the use of water also removes the need for costly dewatering processes such as pumping, screening, filtering and centrifuging. “Dry coal preparation plants offer multiple advantages, such as being smaller and cheaper to operate because of simpler equipment being used, compared with water-based beneficiation that requires pipelines and thickeners, and reduced freight costs (because of the reduced weight of the haul) since moist coal will not be transported,” he outlines.
Coaltech’s coal beneficiation research, in collaboration with the CSIR, aims to develop and adapt coal processing technologies that can improve the efficiency and economics of the South African coal industry, which is facing dwindling reserves.
“The coal in South Africa differs from that in many other countries and, in general, is more difficult to beneficiate. It is, therefore, necessary to evaluate the effectiveness of different new coal processing technologies,” De Korte emphasises.
He tells Mining Weekly that new dry beneficiation technologies are necessary, as the current technologies available are not suitable to prepare export-quality coal. “The current dry-processing equipment is more suited to destoning operations where the quality of the coal is not critical.”
Dry beneficiation exploits the difference in the relative densities of coal and stone to affect separation.
“In shaking tables such as the Fuhe Gan fa Xuan mei, or FGX (meaning compound dry-type coal washer, in Chinese) dry-processing unit, a layer of coal is subjected to a high-frequency vibration, which causes the coal to move to the top of the layer while the heavier stone works its way to the bottom of the layer on the table. The coal and stone can then be discharged at opposite ends of the shaking table,” explains De Korte.
Two new FGX units are being installed at Exxaro’s Matla colliery, near Kriel, Mpumalanga. The plant is expected to be operational by June and will be used to prepare coal for State-owned power utility Eskom.
Coaltech started research on dry beneficiation early in 2009, with testwork on a pilot-scale FGX dry-processing unit being made available by Exxaro.
Coal mining company Eyethu Coal also uses an FGX dry-processing unit to beneficiate coal for Eskom, while global diversified miner Glencore owns a plant with two FGX units, which will soon be recommissioned to beneficiate coal, also for Eskom.
X-Ray Sorting
Coal miner Wescoal currently uses an X-ray sorter at its Elandspruit colliery, in Middelburg, Mpumalanga, while mining company Isambane Mining, also in Middelburg, owns two X-ray sorters. Isambane’s sorters were previously used to reclaim coal from discard dumps and will soon be recommissioned to beneficiate coal for Eskom.
In 2011, X-ray sorting of coal was introduced in South Africa. It uses X-rays to distinguish the difference in density between coal and stone. The principle employed is that the higher-density stone particles absorb more X-rays than the lower density coal and can be distinguished from coal particles using image analysis. The particles identified as stone are removed from the falling stream by a jet of compressed air.
Stone lowers the quality of coal, since it constitutes an incombustible substance. The coal has to be milled to a fine powder before the combustion process and any stone contained in the coal contributes to abrasive erosion of milling equipment.
However, De Korte points out, these methods of dry beneficiation can not completely replace water-based methods, since there are various markets for coal with different quality requirements, some of which can be produced only by using more efficient processing methods, such as conventional DMS.
“Dry beneficiation can, however, be gainfully employed for numerous applications, however, such as where coal is prepared for electricity generation,” he concludes.