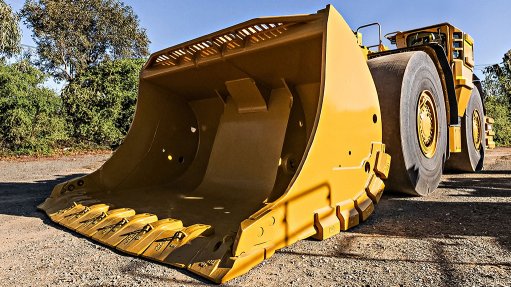
Caterpillar has developed the new Durilock™ Lip Shroud System for underground loader buckets. The fully integrated bucket system features hammerless installation and maintenance-free retention of GET with Cat Infinitite™ elastomer compression retainers. Three interchangeable shroud styles enable a mining operation to quickly remove one type and replace with the type that is best suited to the loader application—without changing the base edge or retention system.
The Durilock system delivers 50% faster installation and removal of GET compared to legacy, mechanically attached systems, and, because there is no need to re-torque bolts periodically, maintenance time for GET is reduced by more than 50%. Additionally, integral corner guards extend bucket in-service time by about 30%.
The Durilock Shroud System is available for Cat R1700 to R3000 loaders and most buckets of 5 to 10 cubic meters capacity.
Innovative, adaptable GET
The Cat Infinitite retention design provides superior retention reliability without time spent performing re-torque procedures. The elastomer compression retainer installs in seconds to allow fast installation and removal. There is no complex hardware to fail, handle or tighten.
The Durilock system offers three different shroud styles to enable matching the GET to the application and conditions in the mine. The D50S Standard is a traditional wedge shape used in most production and development applications. The D50A Abrasion has a contoured design and repositions more material on the shroud base, and the D50P Penetration has less leading-edge material to deliver easier penetration in dense material.
The lip assembly provides the mounting surfaces for the shrouds and corner protectors, which balance corner and center station wear rates. Cast corners are welded to the base edge assembly to create the lip assembly. The corners incorporate a stepped design that eliminates corner shroud torsional loads and delivers superior reliability. The integral corner design boosts corner life by 15% and improves penetration as compared to systems that experience corner erosion and shortened bucket life due to corner rounding.
With the addition of Durilock, Caterpillar has a complete portfolio of GET products that are designed to meet the unique and challenging requirements of any underground mine. For more information about Durilock and Cat GET offerings for underground loaders, contact the local Cat dealer.