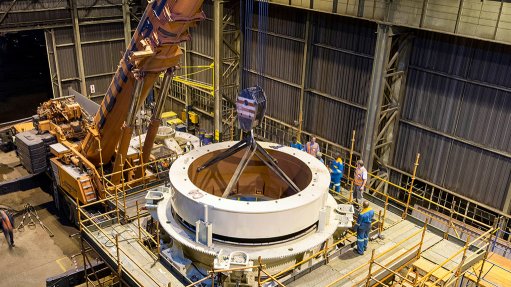
CONE CRUSHER The MP2500 is designed for use in secondary and tertiary crushing
Diversified engineering group Metso’s first MP2500 cone crusher will be operational at base metals miner First Quantum Minerals’ (FQM’s) Sentinel mine, in Zambia, early next year.
FQM operates seven mines and is developing five projects worldwide, currently producing copper, nickel, gold, zinc, and platinum-group elements. It is also developing projects in Zambia, Panama and Peru that, when complete, will increase their combined yearly copper production capacity to more than 1.3-million tons.
The crusher order, worth more than €10-million, was received in the first quarter of 2013.
Metso highlights that, as ore grades decline, more ore needs to be processed to obtain the same amount of the valuable mineral and meet production targets, which often result in increased processing costs. As a result, the global mining industry is striving to develop more energy and cost-efficient technologies for minerals processing.
Metso is responding to this challenge by developing larger and more energy efficient equipment for minerals processing, such as the MP2500 cone crusher.
The MP2500, which is designed for use in secondary and tertiary crushing, was selected for use at the Sentinel mine because it can process large volumes of rock using a single machine. It is also more cost effective as fewer crushers are needed to achieve increased production.
For example, to duplicate the performance of two MP2500s, four smaller MP1250s and the associated infrastructure would be required.
Further, the MP2500 crusher has the ability to crush larger pieces of rock, as it has the largest cone crusher feed opening ever developed by Metso. Its ability to crush rock further than the traditional crushers decreases energy consumption during the later stages of the process.
The MP2500 cone crusher links easily with other Metso products to create a simplified, cost-effective process flow for high production sites.
Less Equipment Means Improved Safety
The development of the MP2500 cone crusher resulted in innovations in health and safety, many of them based on discussions with FQM. The most important is a reduction in the amount of times personnel have to conduct work due to fewer pieces of equipment.
Serviceability and ease of maintenance was also a focus during the design. Part lifting, installation and removal were all considerations of the development process. For example, the socket weighing nearly two metric tons, led Metso to develop a patent pending hydraulic process for removal. This new method of socket removal eliminates heating if in a difficult working space, eliminates process variables and reduces the stress on the socket and main shaft.
The company has also refined the existing jackbolt locknut design to reduce the amount of manual work and replaced it with hydraulics to simplify the same work.
These examples, along with other serviceability features and purpose-built lifting fixtures, simplify the maintenance of large equipment. Metso is assisting the Sentinel mine to guarantee the efficient operation of the new MP2500 by stationing full-time field-service engineers on site for one year after commissioning and by stocking critical spare parts on site and at Metso’s distribution centre, in Vereeniging.