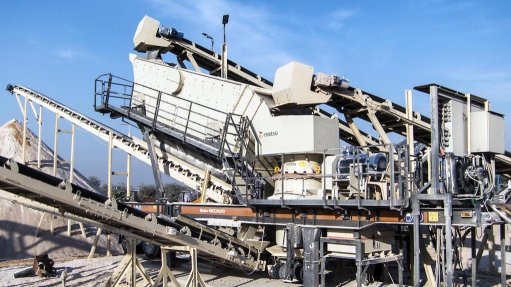
NW RAPID CRUSHING PLANT The NW Rapid can increase production capacity by as much as 30% and offer higher uptime, better safety and ease of use
Diversified engineering group Metso reports that its NW Rapid is the world’s “first and only” wheel-mounted crushing plant that fits into standard (12-m-wide) shipping containers and can be set up for operation in less than 12 hours.
The company says that, in addition to fast installation, the NW Rapid can increase production capacity by as much as 30% and offer higher uptime, better safety and ease of use.
Metso declares that, in the highly competitive aggregates market, its customers are increasingly looking for more cost-efficient ways of improving their productivity and lowering the cost of operations.
“The NW Rapid crushing and screening system, introduced a year ago, has proven to provide flexibility at a whole new level. The concept helps aggregates producers to now profit more from even smaller contracts than before and to change site locations more often,” the company states.
Metso says that NW Rapid’s high production capacity was one of the decisive factors when India-based M/S M G Contractors required a new plant.
“The new Metso NW Rapid plant is a perfect fit for our growing needs for more ecofriendly, mobile and economical solutions. When looking at the available products in the market, we realised that the NW Rapid is a breakthrough in terms of application and quality.
“It is also backed by Metso’s good brand reputation and their service standards. With this purchase, we feel confident that our production efficiency will increase by as much as 30%, compared to a traditional solution. The 12 hour setup time is extraordinary,” enthuses M/S M G Contractors director Udit Mittal.
Further, Metso points out that setting up a conventional portable crushing and screening plant normally takes at least a week and often requires preparation in terms of foundations and other site conditions.
Additionally, the company notes that equipment transportation can be difficult and requires special arrangements.
However, Metso highlights that, because the NW Rapid fits compactly into standard shipping containers, it is easy to transport from one place to another by sea, rail or truck.
Fast installation and dismantling are facilitated with hydraulically fine-adjustable support legs, hopper walls and screen lifting.
“Cost-efficiency achieved through easy setup and flexibility serves our customers in the emerging markets particularly well, since it is important to be able to swiftly move production to where the construction projects are located,” says Metso portable solutions product manager Julius Mäkelä.
He notes that the NW Rapid series includes equipment for multiple aggregates production needs, such as portable jaw crushing and cone crushing, as well as horizontal and vertical shaft impactor plants.
Mäkelä remarks that, with these products, customers can set up multistage crushing and screening plants for high-quality end products, as well as for ballast production.
He says the NW Rapid crushing and screening plant can be fed by excavator, wheel loader or dump trucks. Ready-made layouts cover screen feed and cone feed applications, with and without surge hoppers and field conveyors.
Mäkelä adds that the increased capacity is mainly achieved by the powerful Nordberg GP220 cone crusher and the new four-deck dual-slope screen, enabling higher screening performance. He points out that the whole process can be “precisely adjusted” by a process control system.
“The new Metso IC50C process control system forms a seamless combination between the primary crushing stage and the secondary crushing and screening stage of the plant. The whole process, including field conveyors, can be started and stopped with the push of a single button, making daily operations safe and easy,” Mäkelä highlights.
He also points out that the system complies with European safety standards and meets the requirement to be issued with a CE marking.