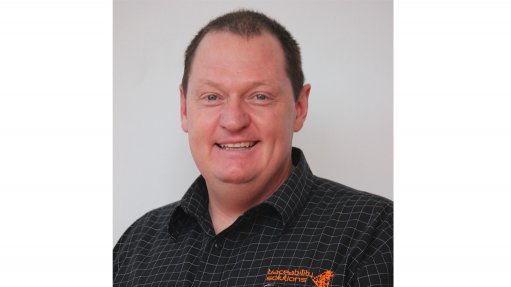
Traceability Solutions general manager Kyle Parker
The instability in the mining industry over the past few years has led to an increase in the theft of tools, minerals and assets, which poses problems for pump manufacturers supplying the mines with equipment and accessories. In addition, there has also been a marked increase in the theft and counterfeiting of related quality parts.
Pump manufacturers typically secure data or rating plates to the casing of a pump to assist with identification, but Johannesburg-based Traceability Solutions general manager Kyle Parker believes it is not sufficient anymore, as the rating plates are easily copied or removed, resulting in compromised quality.
Rating plates typically contain information such as the product or serial number, component number, date of manufacture and company logo. They are used to assist with identification when replacements are done under warranty and to ensure that worn parts are replaced with quality ones from the original manufacturer.
Parker says that despite this, there is an increase in the use of non-original parts, which may lead to higher costs owing to more maintenance during the life cycle of the pump.
He states that some manufacturers are now going beyond the legal requirements for data plates by using a two-dimensional (2D) Data-Matrix barcode to identify their components. The 2D code consists of a series of dots, which are only readable using specialised scanners and thereby assists in eliminating the need for human readable text on the parts. These codes are generated using computerised Dot Peen technology or a laser marking system and can contain up to 1 000 characters, depending on the size of the code.
“These codes have historically been used for ‘track and trace’ applications, inventory control, resolving service-related issues and implementing stock control measures in the pump industry, but are now also being used for quality control and production management in the pump industry.”
Manufacturers are using the technology to save a large amount of data into these codes, such as batch numbers, serial numbers, part numbers and date codes, among others.
“Due to the fact that these 2D codes are not easy to duplicate without the aid of a computerised marking system, these codes are successfully preventing the counterfeiting of parts and reducing the implications of damage caused by identification plates being removed, and manufacturers losing all identification and traceability of the part,” says Parker.
Traceability Solutions provides a number of products that are able to mark the various materials found in the pump industry, ranging from soft plastics through to hardened materials. Many pump and pump-part manufacturers are using Traceability Solutions’ products in order to help their customers to easily identify the correct and original replacement parts for their installed pumps.
“These marking solutions assist to reduce the frequency of repairs by ensuring that the client uses the correct replacement parts, thus increasing uptime and saving on long-term costs,” Parker states.
Traceability Solutions is based in Northriding, Johannesburg and has branches in the Eastern Cape, Western Cape and KwaZulu-Natal.
Hall 6 Stand J25