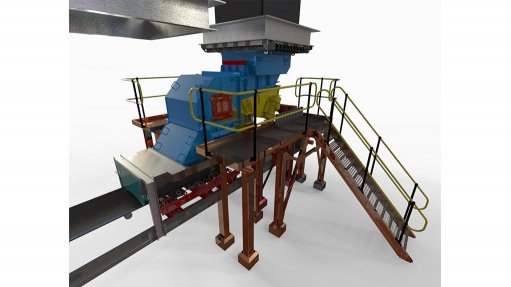
CUSTOM COLLABORATION The solution developed by Weba Chute in collaboration with Kwatani promises direct savings in terms of mill bearings, as well as less mill downtime
Specially designed ore silo chutes from transfer solutions provider Weba Chute Systems will be installed at a South African gold mine to reduce mill wear and other processing challenges caused by the uncontrolled flow of mined material into the mills.
Developed in collaboration with vibrating screens and feeders manufacturer Kwatani, the solution must also deal with frequent large-sized material as the mine has no crushing stage before the milling circuit.
Weba Chute Systems technical adviser Alec Bond says the over-feeding of material through the existing manually operated chutes causes regular ‘mill vomit’. The inconsistent feed exacerbates wear on mill bearings and
the waves of material carry insufficiently milled material out of the mill, including chunks of rock. This leads to problems for the downstream mineral processing facilities,.
“The challenge starts with the existing chutes needing constant supervision and control by operators, being opened and closed with a chain block device.
“Our solution was to design a robust, self-controlling chute and feeder system that would ensure an even flow of material into the mills,” Bond explains.
The mine’s existing system had no means of closing the silo outlet. Therefore, any maintenance at the chute area required the emptying of the silo and the stoppage of the mill.
“We, therefore, added a spile bar arrangement which seals off the silo,” says Weba Chute Systems designer Wesley Hunkin.
The Weba chute, which is choke fed, is placed under this installation. This allows the feed rate to be controlled by the Kwatani feeder, which has been integrated into the chute design.
The vibrating action of the feeder controls the tonnage and feed rate to the mill, keeping the flow constant. New mounting structures have been designed to accommodate each chute and feeder.
Oversized rocks in the ore feed are a serious challenge. This makes it important for chute designs to accommodate the worst-case scenario of chutes choking, says Hunkin.
He highlights that the flow of material is also controlled to prevent direct impact onto the conveyor belt feeding the mills, and to ensure central loading.
“If the material from the feeder is biased to the one side, our chute brings everything to the centre. This enhances the consistency of material flow into the mill.”
Bond emphasises that the customer motivated for a concept change.
“Given our materials handling experience, design expertise and high-quality local manufacturing facility, we were able to work closely with the customer and with Kwatani to turn this concept into reality,” he says.
Weba’s solution promises direct savings in terms of mill bearings, as well as less mill downtime. Significant gains in terms of recovery rates in the plant can also be achieved.
“The joint solution is a testament to the expertise and capacity in the local manufacturing sector,” Bond concludes.