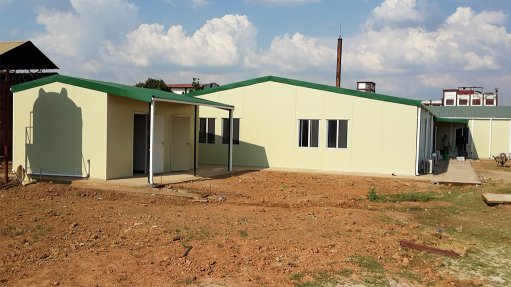
CORE COMFORT AMBS’s newest 60-mm-thick polyurethane core panels have similar insulation properties to a wall of 2.5 bricks thick
Prefabricated building solutions manufacturer and supplier African Modular Building Solutions (AMBS) is constructing an emergency communication and control call centre facility, comprising six buildings, for Zambian copper producer Mopani Copper Mines (MCM) at the company’s headquarters in Kitwe.
AMBS financial manager Rhett Bellamy explains that the six buildings include a 680 m2 main call centre, three 25 m2 locker rooms, a 23 m2 generator and compressor building with a laundry room and a 36 m2 underground equipment preparation and inspection room.
He explains that the main call centre building is being constructed using a portal frame structure, which will accommodate 15 offices, a kitchen, ablution facilities and a central open area for emergency mine rescue vehicles and fire trucks.
All six buildings will be erected on concrete raft slabs, which will be linked by covered walkways.
Bellamy highlights that the company will also install all the building services and the required components, such as electrical, plumbing, air conditioning, roller-shutter doors and epoxy flooring for heavy vehicle traffic in the main call centre building. The project is expected to be completed by the end of next month.
Bellamy highlights that the facility is being constructed using about 370 of the company’s 60-mm-thick polyurethane core panels, cladded on either side with 0.5 mm chromadek steel sheets, which the company has been manufacturing at its Roodepoort facility since 2013.
He adds that the polyurethane panels were selected for the project because they are lightweight, expediting installation significantly, which met MCM’s requirements that the complete building solution be delivered within two months.
Owing to the tight deadlines, AMBS required a solution that was easy to transport. “We sent two super link trucks to site, which were loaded with all the portal frames, roof trusses, wall panels and trims needed to erect the buildings,” Bellamy points out, noting that the trucks arrived on site on August 1, four days ahead of schedule.
Meanwhile, AMBS is also constructing five 36 m2 three-bedroom prefabricated accommodation units at Spanish technology group Abengoa’s 100 MW Xina Solar One project, in the Northern Cape.
Bellamy notes that the company is supplying a turnkey housing solution for the project, which includes the supply and installation of concrete slab foundations, toilets, basins, showers and furniture, as well as an environmentally safe wastewater treatment plant.