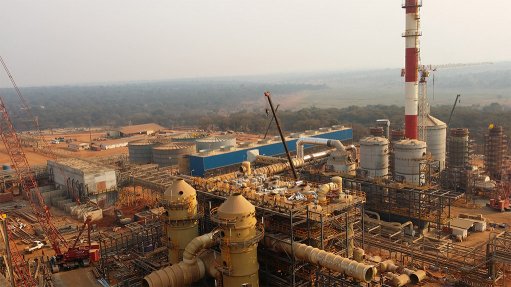
KANSANSHI SMELTER COMPLEX
Dickinson Group’s refractory installation crew has arrived at the Kansanshi greenfield copper smelter project in Solwezi
Photo by: Dickinson Group
Minerals processing and smelter services company Dickinson Group’s refractory installation crew has arrived at Canadian mining and metals company First Quantum Mineral’s (FQM’s) Kansanshi greenfield copper smelter project, in Solwezi, Zambia. The mine is owned and operated by Zambian mining parastatal Zambia Consolidated Copper Mines Investment Holding (ZCCM-IH) and FQM subsidiary Kansanshi Mining’s Kansanshi copper mine.
Dickinson Group sub-Saharan Africa director Anton Briedenhann tells Mining Weekly that the company mobilised the materials handling crew, which is responsible for materials marshalling and sequencing in preparation for the R24-million project in July 2014.
The project is scheduled for completion in November this year.
Dickinson Group’s scope for the project includes installation of a matte settling electric furnace (MSEF), an Isasmelt furnace, four Pierre-Smith converters, two Anode furnaces and two incinerators.
“Refractory materials of 4 271 t are supplied by Austria-based refractory products manufacturer RHI for the lining of the furnaces and converters,” Briedenhann highlights, adding that the materials were shipped to Durban port from Austria, Germany and China, and then transported by truck to Zambia from June 2013.
Meanwhile, Dickinson Group completed a R13-million smelter shutdown and rebuild project in June 2014 for Mopani Copper Mines, which is owned by joint venture company Carlisa Investments Corporation, comprising mining companies Glencore, FQM and ZCCM-IH.
Dickinson Group was contracted as the engineering, procurement and construction management company for the project. The project entailed the rebuild of the Mopani Copper Mines smelter’s Isasmelt furnace and MSEF, which included the demolition of the linings using the latest Brokk demolition machines.
The group completed the partial rebuild of the MSEF, which included the side and end walls, as well as the complete roof and a section of the hearth.
Briedenhann says there was additional scope creep – uncontrolled changes in a project’s scope – that occurred during the shutdown, where Dickinson had to partially repair the MSEF hearth.
“With any project, one of the biggest challenges is scope creep. The Mopani project was scheduled for completion within 37 days, which we managed to achieve in 31 days. However, securing the supply of brick was a significant challenge, as scope creep resulted in more bricks being required to complete the project,” he recounts.
To proceed with the installation, Dickinson Group had to cut the bricks to suit the shapes required for the installation.
Diversified engineering services provider Harrison & White Contractors (H&W) was appointed mechanical subcontractor for the project. H&W’s scope involved replacing the copper blocks, the roof suspension system and all the steel panels on the side and end walls.
Briedenhann further points out that Dickinson Group provided an Ez Lift platform – a suspended platform that was hoisted up the Isasmelt shaft during installation. “It was the first time that this technology was used at the Mopani project. It is based on a new design provided by Dickinson Group, together with its partners and the platform’s supplier, US-based refractory equipment supplier Bricking Solutions.
“The platform was fabricated from aircraft- grade 6061-T6 aluminium with a three-to-one minimum safety factor. The platform was a modular design, which made assembly relatively easy with parts that were no heavier than 50 lb and no longer than 10". The assembly of the platform took only one hour,” Briedenhann explains.
He highlights that the platform, hoisting and control system used for the Ez Lift platform were imported from the US. This system was also new technology employed at the smelter, with the controls and hoisting system located on the platform instead of at the top.
Dickinson Group provides an array of specialised services, which increase productivity and performance and reduce costs to the metals smelting and mineral processing industries. This is done through leadership, technology and innovation across related industries, together with complementary product and service offerings.