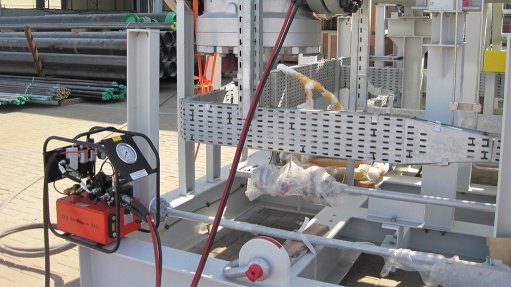
TPA WRENCH PUMP The air-driven torque wrench pump developed in 2013 has achieved record sales
UK-based hydraulic tools manufacturer Hi-Force has achieved record sales for its torque wrench pump air-driven (TPA) unit and torque wrench pump electric-driven (TPE) unit, with sales for the six months following the units' launch being 10% higher than predicted by MD Kevin Brown.
Development on the TPA and TPE units started in late 2013, with the official launch in November last year during the Abu Dhabi International Petroleum Exhibition and Conference.
The international market’s response has been largely positive, with Hi-Force marketing director Laura Thompson noting that prior to the official 2014 launch, Hi-Force’s UK manufacturing facility had back orders for more than 50 units.
Hi-Force South Africa GM Sean Sandham adds that the local response has also been favourable and that, to date, there have been no returns or warranty claims for any of the pumps sold in South Africa.
Product Specifications
Thompson states that the TPA and TPE units can provide consistent and reliable hydraulic power for bolting applications in various industries, such as mining, construction and power generation.
Designed to withstand the demands of harsh operating environments, particularly the challenging conditions of the South African mining industry, the high-speed, three-stage design of the TPA and TPE units allows for faster flow at midrange pressure.
The multioutlet four-way design enables four wrenches to run simultaneously and provides an even compression of the critical leak-sealing gasket on the flange joint connections. This ensures that projects with time constraints are completed safely and efficiently.
Thompson further explains that the TPE unit comes standard with an oil-cooling heat exchanger, which is automatically activated to cool the pump and hydraulic fluid, extending the service life. The TPA model features an exhaust radiator inside the oil reservoir to assist in maintaining a relatively low temperature. Both units have a maximum oil temperature of 80 °C.
The two TPA models require a 101.5 psi air supply and are equipped with either an analogue or a digital pressure gauge, while the TPE range has 12 models that offer power supply options of 50 Hz and 60 Hz on all of the 110 V, 120 V, 230 V and 480 V pumps.
The TPE and TPA units’ lightweight aluminium reservoirs have an oil capacity of 7 ℓ and the pumps weigh 30 kg each. While these units are some of the lightest hydraulic torque wrench pumps available, they have a rigid roll frame that provides protection while allowing for manoeuvrability on site. At 45.6 cm in length and 28.6 cm wide, with a height of 47.6 cm, the pumps come standard with a glycerine-filled gauge, with digital pressure gauges available as an optional extra.
Safety features include an adjustable pressure-relief valve, with locking nut, and a 5-m-long pendant cable that allows for considerable distance between the pumps and the bolting application for additional user convenience.
Further, Thompson adds that the TPA and TPE units are compatible with the TWS-N square drive and the TWH-N low-profile female hexagon design hydraulic torque wrenches.
She says Hi-Force’s strategic priority of increasing its market share by introducing innovative products is what led to the new pump design, adding that the earlier version was ”similar in design and performance to [those of] competitors, that is, too heavy, too slow at midrange of operation and without any unique selling features or benefits”.
The Daventry-based research and development team created “a twenty-first-century pump for a twenty-first-century market” by interpreting customer feedback and market analysis, and applying that knowledge when establishing the design parameters, Thompson notes. The pump heart, motor electronics and cooling systems, as well as the flow and pressure controls, were designed using computer-aided design technology.
After the initial prototype proved that the fundamental ideas and mechanics worked, the team refined the dimensions and aesthetics before sending five units, manufactured in-house, for field testing in offices in Dubai, the US, the UK, Holland and Malaysia.