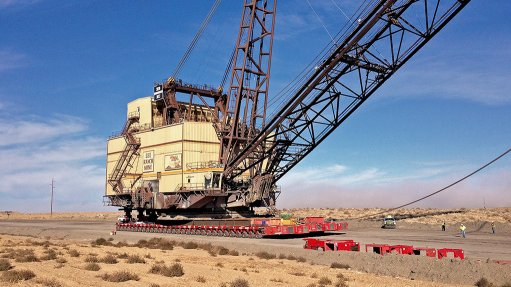
INTACT HAULAGE Mammoet is able to transport intact dragline machines using its self-propelled modular transport units
Global heavy-lifting, heavy-haulage and logistics company Mammoet is aiming to break into the mining industry with its comprehensive logistics offering, coupled with its traditional heavy lifting and ability to move heavy equipment, says local branch Mammoet Southern Africa (SA).
Mammoet SA marketing and business development manager Ryan Amos tells Mining Weekly that the company is keenly eyeing the South African and African mining sectors, owing to the vast potential Mammoet has in terms of end-to-end logistics solutions for large pieces of equipment, and even buildings.
The local division operates in the Southern African Development Community region, including countries such as South Africa, Mozambique, Botswana, Zimbabwe, Lesotho, Namibia and Swaziland.
Amos adds that a vast amount of skills, technology and experience can be transferred to the company’s Southern Africa division from the global company, which has undertaken many mining-specific projects elsewhere in the world.
Mammoet entered South Africa in 1996, when it acquired lifting company Kew Engineering. “From where we started to where we are now is worlds apart,” says Amos, adding that the company sees massive potential for its operations in the mining industry once the economy improves.
The global office has received a significant amount of work in the mining industry, especially in the US, having moved some of the largest pieces of equipment and buildings to date.
Meanwhile, he says the current downturn in commodity prices has had little negative effect on Mammoet SA’s operations because this is a new market for the company.
However, most potential contracts in the mining sector have been put on hold “indefinitely”, as mining companies are stagnant, or downscaling and cutting back on expenditure, notes Amos, adding that this is prompting many mining companies to find ways of moving machinery in-house.
Reducing Downtime
Amos notes that in living by its motto, Mammoet SA can add value to the mining industry. The biggest thing we move is time, by planning the fastest and safest means of moving equipment, thereby reducing a client’s downtime and reducing unprofitability.
Amos tells Mining Weekly that Mammoet SA offers end-to-end logistics and heavy-haulage solutions. “We can perform all logistics operations, from A to Z, including forwarding and clearing, transportation and full project management.”
All Mammoet SA’s operations are performed using in-house skills and equipment, “nothing is outsourced”, he says, adding that this helps reduce costs, mitigates unnecessary cost overruns and ensures that the safest methods are used under the global Mammoet best practices.
Its range of heavy-haulage equipment includes some of the industry’s largest and most specialised pieces of equipment – from self- propelled modular transport units and skidding equipment to multiaxle abnormal-load trucks and customisable jacking systems, all of which can be used independently or in conjunction with each other to offer clients a haulage solution in most circumstances.
In this regard, the global Mammoet company has assisted in some of the most unique and challenging haulage and salvage operations. This includes salvaging the Russian submarine Kursk from a depth of 108 m in 2001, when it had crashed into the ocean floor of the Barents Sea after an explosion in its torpedo room.
Amos says, for example, if a mining company in Africa wants to import a new large dragline machine from an overseas supplier, then Mammoet SA can arrange for the equipment, manufactured in the relevant country, to be hauled overland from the factory and then by ship to a South African port, including the forwarding and clearing of all shipping and customs documents.
“. . . from the port, we can transport the equipment directly to the mine site, where Mammoet SA can also assist in assembling . . . cranes, hydraulic jacks or skidding equipment.”
He adds that a key advantage of Mammoet’s solutions is that large machinery can be transported intact, without the need to disassemble certain significantly sized components prior to haulage.
“Currently in South Africa, equipment, such as draglines, are partly disassembled so that they can be transported individually, but this leads to a longer downtime between locations, as the machinery will require reassembly at the new site,” says Amos.
Mammoet has moved draglines machines fully intact for several projects, in the US.
Further, Amos tells Mining Weekly that, owing to Mammoet’s using logistics engineers, special routes are devised to suit almost any type of terrain.
Previous projects for the global Mammoet company have included the lifting of bridges to accommodate high loads on roads and the building of temporary bridges to overcome gaps.