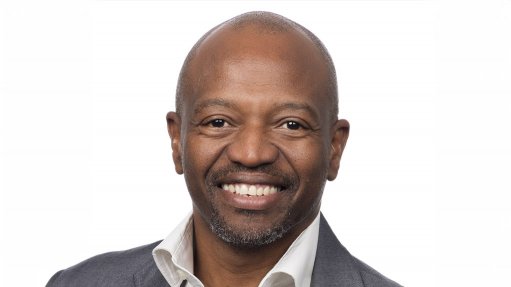
Khomotso Duiker, Business Line Manager for Underground Drills at Sandvik Mining and Rock Solutions
The world of underground drilling technology is undergoing a significant transformation. This evolution promises not only enhanced precision and productivity but also a wealth of detailed operational data. Moreover, it offers the potential for safer drilling practices through remote control. One company leading the charge in this revolution is Sandvik Mining and Rock Solutions, offering a wide range of underground drill rigs and bolters. Customers are progressively embracing intelligent drilling, with a growing interest in battery electric models for the future.
Khomotso Duiker, Business Line Manager for Underground Drills at Sandvik Mining and Rock Solutions, reveals that the Sandvik 400 Series and the Sandvik 300 Series now feature intelligent models. These innovations are driven by Sandvik's iSURE® Intelligent Sandvik Underground Rock Excavation software, enabling automated drilling cycles.
“In Southern Africa, some forward-thinking diamond mining customers are already reaping the benefits, using the DD422i development drill rigs, as well as the DL422i and DL432i top hammer longhole drill rigs,” he says.
Duiker cautions that integrating intelligent technology into drilling operations is not without its challenges and says that Sandvik Mining and Rock Solutions collaborates closely with customers during this transformative phase, offering training and support. Sandvik's Product Masters, experts in the equipment, play a vital role in facilitating the introduction of cutting-edge machines. Additionally, Sandvik's in-house training department ensures operators and maintenance teams receive the necessary guidance.
“Understanding the full potential of automated functions is crucial for operators. These functions not only enhance safety but also boost productivity. The level of automation can vary from individual machines to entire fleets, with some machines capable of completing development ends without any operator intervention,” Duiker says.
One remarkable feature of Sandvik’s intelligent machine models is their ability to download the mine's drill plan for development ends and execute drilling precisely according to that plan. This optimisation leads to more effective blasting, eliminating issues like underbreak or overbreak.
Remote control capabilities are another highlight. The tele-remote function allows drilling operations to be controlled from the surface, provided there is sufficient on-site network infrastructure. To facilitate this transition, Sandvik Mining and Rock Solutions has a dedicated Business Line Manager overseeing automation initiatives.
Monitoring equipment performance has become critical for mining operations, and Sandvik's drill rigs come equipped with the Knowledge Box™, gathering valuable data such as advance speed, penetration rate and cycle times. The data, collected by iSURE®, can be leveraged to optimise work cycles and improve the drill and blast excavation process through targeted reports and analysis.
Duiker says that while data connectivity is essential, most mines are already addressing this requirement. “Operators can track rig performance from a control room, identifying signs of underperformance or potential failures in real-time. This data empowers mines to make necessary improvements, be it in operator behaviour or machine condition, all of which is aimed at increasing productivity and uptime.”
Sandvik's dedication to sustainability also extends to supporting Small Medium Micro Enterprises (SMMEs) in South Africa. The company actively facilitates the extraction of carbide buttons from its drill bits in partnership with SMMEs, fostering entrepreneurship and job creation. This initiative contributes to a circular economy by recycling tungsten carbide buttons from drill bits, reducing energy consumption by 70 percent and cutting carbon dioxide emissions by 64 percent when manufacturing tools. This aligns perfectly with the principles of sustainability and environmental responsibility.