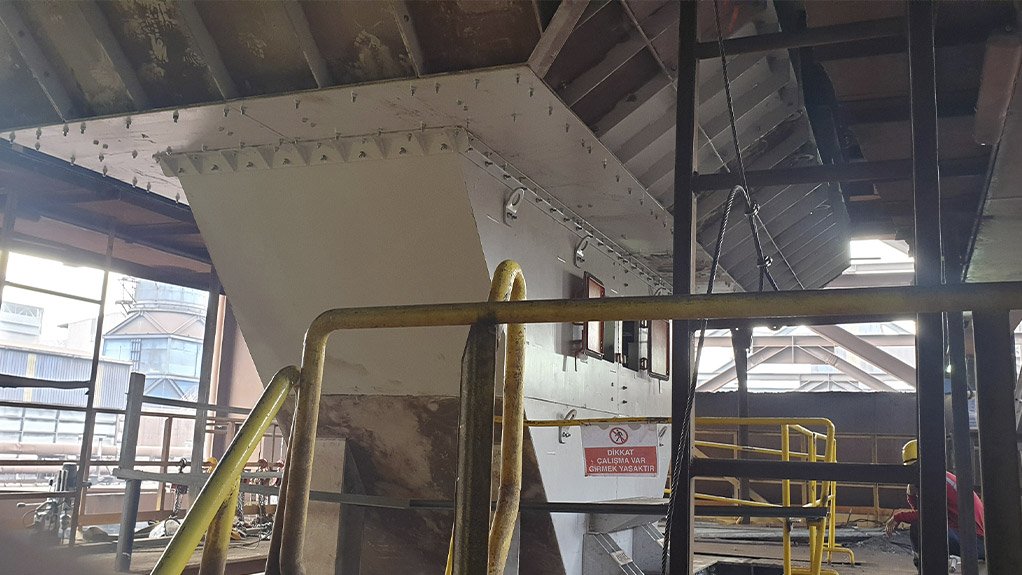
The installation of custom-engineered transfer chutes at a sinter plant in Turkey has highlighted the value of Weba Chute Systems’ decades of experience
The recent installation of custom-engineered transfer chutes at a sinter plant in Turkey has highlighted the value of Weba Chute Systems’ decades of experience in design engineering and manufacture.
According to Dewald Tintinger, technical manager and designer at South Africa-based Weba Chute Systems, the application had to deal with sinter material with temperatures up to 700⁰ C, while also reducing the level of material degradation which could undermine the furnace performance.
“The plant process uses heat to produce a solid bed of sinter from imported fines, which is then broken down into manageable clumps of minus 150 mm,” says Tintinger. “Our chute solution had to ensure that these clumps did not degrade unduly as they passed through the chute from the sinter breaker and onto a circular cooler.”
He also emphasises that to ensure the cooling conveyor operates energy-efficiently, the chute delivers a homogeneous feed with coarser material at the bottom and the finer material on top. This is because cooling takes place from below.
The scale and complexity of the chute structure is substantial, with a double-inlet design and a height of some 12 metres. With top inlet dimensions of 5 metre by 4 metre and 5 metre by 2,5 metre respectively, these chutes were narrowed down to control the stream before widening again to discharge a wider spread onto the cooling conveyor.
As is common in the design and engineering of Weba Chute Systems, a layer of material passing through is captured using dead boxes, creating a protective lining on the chute surface that reduces
wear and resists the impact of high temperatures. The plant had previously been successfully equipped with four chutes from Weba Chute Systems.
“The customer’s experience with our earlier chutes was an indication of what our specialised expertise delivered, especially in terms of fit-for-purpose solutions,” Tintinger says.
Weba Chute Systems uses the latest discrete element modelling (DEM) software to compute and simulate the interaction of individual particles and boundaries, accurately predicting bulk solids behaviour and building this into each specific design. The company can point to more than 5000 successful chute installations globally underpinning its position as an international leader in transfer point solutions.