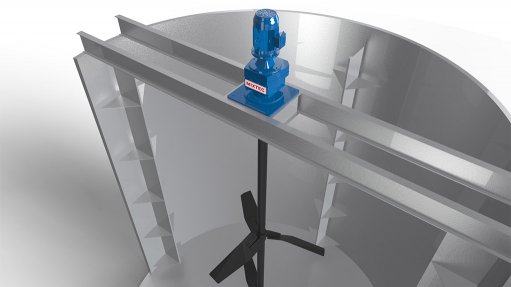
MIXTEC MIXER Mixtec retrofits pre-existing mixers with modern custom designs
Demand for more effective and efficient impeller and agitator technology is on a dramatic upward trend in the Democratic Republic of Congo (DRC), says industrial agitator and mixer manufacturer Mixtec sales and projects manager Rudi Swanepoel.
He notes that the company sees a significant opportunity in copper processing, with develop- ments and project explorations constantly increasing in the country. “Having done numerous projects in the DRC, we see the need for innovations and improvements that will assist in speeding up recovery time and productivity.”
Mixtec has “stepped up” in terms of upgrading and retrofitting existing mixers, and there is a need for greater life spans through continuous maintenance and improvements, he adds. The company retrofits pre-existing mixers with modern custom designs, and not only retrofits its own products, but any preinstalled system.
“The mining industry has benefited from our ability to refurbish and improve on existing mixing systems. We not only produce improved power savings but also increase the operational life of existing agitators.”
Further, Swanepoel states that Mixtec has serviced most of the small and large mines throughout the DRC with its custom-designed mixers, and the copper-cobalt industry has also benefited, with “several mixers at one plant in the DRC, which we are proud of”, he enthuses.
The company prides itself on its technical support team that offers assistance in the DRC through site evaluations, inspections, on-site training and walk-throughs. “Many companies do not initiate the personal interaction and training that Mixtec offers, which is a complementary service,” he points out.
Challenges
Swanepoel says some of the challenges that Mixtec faces in the DRC are outdated knowledge of mixing technologies and developments, and poor design practices – which the company usually evaluates and redesigns – as well as using poor material.
Although there is a lack of knowledge regarding the benefits of mixing technology in processing applications, Mixtec tries to educate the mines through training, he adds.
“The case with dynamic systems is that these mixers need to be maintained and manu- factured to the best quality and standard, ensuring smooth operation. We apply our research to produce real-world results using stringent fabrication methods.”
The company also uses the latest international standard inspection procedures and advanced machine tools to provide tolerances for accurate alignment and a precision-made product.
Moreover, Mixtec can constantly test and improve its products, and provide testwork for more demanding and uncommon applications at a client’s request through its global network of laboratories.
“Having our own on-site laboratory enables us to constantly develop and test new impellers and improve their efficiency and, subsequently, provide a continuously improving quality of service and more efficient designs for clients,” Swanepoel highlights. The ability to quickly assemble small-scale versions of larger mixers in the field enables Mixtec to test and analyse problems quickly and accurately, and respond to problems at a rate “unmatched” by its competitors, he advances.
Meanwhile, the company hopes to expand significantly with regard to carbon-in-leach processing, and has expanded its research and development department, which is dedicated to further improve and perfect the company’s systems in terms of mechanical integrity, as well as process knowledge and application.
“Mixtec has increased its staff complement and training programmes to better service clients locally and globally,” Swanepoel concludes.