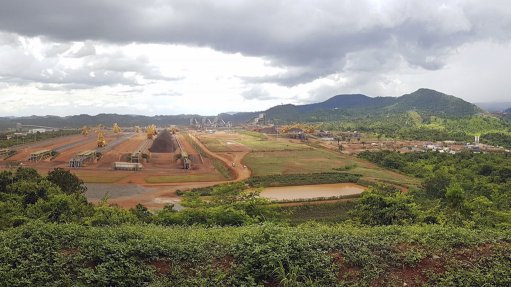
ONE FOR THE BOOKS Vale’s iron-ore mining project in North Brazil is the largest of its kind in the company’s history
Laser measurement technology supplier LASE has delivered 15 LaseBVC laser-based measuring systems for bulk volume transported on conveyor belts to an iron-ore mining project at the S11D Eliezer Batista complex owned by Brazilian mining major Vale.
Opened in December 2016, the iron-ore mining project, in North Brazil, is the biggest iron-ore mining project in Vale’s history. At 90-million tonnes a year, Vale posits that it is the largest iron-ore mining project in the world.
The operation site at the S11D complex, in the Brazilian municipality of Canaã dos Carajas, in the state of Para, hosts a “huge” plant, to which material is transported on conveyors. The material volume needs to be determined by specific measurement applications from LASE.
Commercial operation of the complex started in January, whereafter LASE began rolling out the LaseBVC systems, with the systems commissioned together with its long-standing Brazilian partner company, C+ Tecnologia.
“This prestigious project sets a new standard in the mining industry where advanced technology meets high productivity,” LASE said in a March press statement.
To measure the height of iron-ore as well as the volume being transported on conveyors, one laser scanner is mounted above each conveyor belt. The scan direction of the laser system runs across the transfer direction of the conveyed material and generates two-dimensional profiles. These are compared with so-called zero-profiles, which have been stored during the initial commissioning of a conveyor belt. By knowing the individual difference and the belt speed, the exact volume can be determined. Additionally, if the bulk density is known, the mass flow can also be calculated.
By the use of high-resolution laser scanners with a scan ratio of up to 100 scans a second, the volume of the material can be recorded even at high transportation speeds. Special algorithms within the LaseBVC software application for the adjustment and calibration ensure high measurement accuracy.
The system can be operated intuitively, owing to user-orientated dialogue control and configuration wizards, for simple commissioning. For integration in production plants, the common interfaces of Ethernet Transmission Control Protocol/Internet Protocol, Profibus DP, Analog 0 mA to 20 mA and Serial RS 422 are integrated.