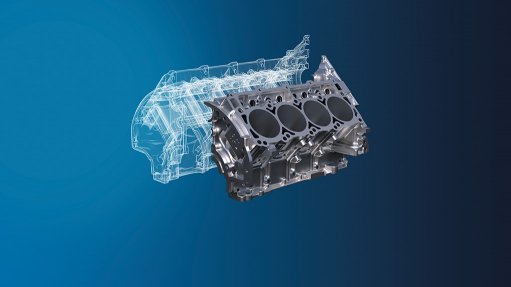
CASTING CONCEPT The new materials constantly being developed by Voestalpine not improve the quality of end product but also the life of the die-sets as well
Steel and technology group Voestalpine boasts a strong footprint in the supply of metals used in various die-casting applications and strives, through continuous research, to further expand its product and reach in South Africa and Africa.
The company says researchers at its mills, in Austria and Sweden, are continuously striving to develop improved steel and processes with clients and suppliers.
Research includes improving its current additive manufacturing metal powder used in three-dimensional printing die-sets.
The company is actively working with clients to ensure that the steel provided is the best suitable grade, and according to client requirements.
“We focus on customers that do die-casting, as we are the steel supplier with required steel product to manufacture the die-sets.”
Providing a higher-grade steel for die-casting allows for a longer die-set life span, consequently saving clients cost in terms of die-set replacement, as well as loss of production time.
Importantly, the number of shots achievable in a die-casting die is strongly influenced by the working temperature of the casting alloy.
The die life for a specific alloy can vary considerably, owing to the design of the cast product, the surface finish, the production rate, the process control, the design of the die, the die material, its heat treatment, and the acceptance level of size and surface-finish variations – all factors Voestalpine considers when supplying its clients.
Meanwhile, Voestalpine supplies a large portion of its materials to the South African automotive sector, owing to the sizeable local automotive manufacturing industry.
It also supplies a lot of materials to the plastic industry, which uses moulds for various packaging solutions.
Additionally, the supply of its metals to the overall die-casting sector makes up a healthy portion of the market share within Voestalpine SA.
Waste Not Want Not
The company, based on its long and extensive global experience in the high-pressure die-casting industry, understands that a reduced scrap rate and improved overall equipment effectiveness are the most crucial requirements to improve productivity.
Additionally, optimised cycle times, reduced maintenance, less downtime and extended die lifetime are critical to an effective manufacturing process.
The company aims to reduce the total cost of ownership of every die-cast part manufactured by its clients.
This can be achieved by, for example, improving the overall equipment effectiveness of the die-casting machines or by reducing the scrap rate through developing innovative tooling solutions.
Using such solutions, such as engineered products with conformal cooling generated through additive manufacturing, reduces the cycle time by more than 30% – even for highly complex parts – for clients.
Voestalpine also assists clients in finding the right combination of tooling materials and required services for every part to significantly increase production runs and produce higher-quality parts.