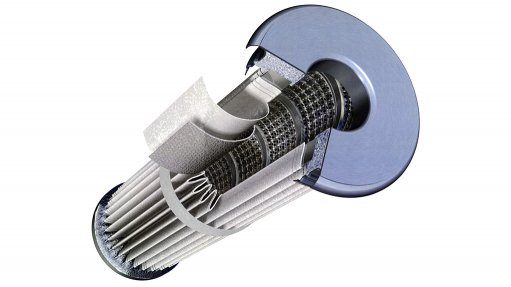
X-600 The X-600 offers a filtration area at least two to four times higher than that of conventional bags of the same diameter
Sefar Group subsidiary and filtration company Sefar Filter Pure released its X-600 – a high-temperature pleated filter element – in January 2020. Despite being two years since its release, Sefar Filter Pure is the only manufacturer and distributor of the X-600, which is used in dust extraction baghouse applications.
The X-600, with an expanded polytetrafluoroethylene (e-PTFE) membrane, offers a filtration area at least two to four times higher than that of conventional bags of the same diameter.
Consequently, the air/media ratio is divided in half, reducing the differential pressure “tremendously”, says Sefar Filter Pure MD Shawn Kallmann.
The X-600 also comprises innovative sealing technology that eliminates leaks, 100% metal caps at the top and the end, ultra-resistant aluminium sealing, sealed stitching, fiberglass felt with type A phenolic resin, a galvanized steel core, and heavy-duty bands.
The X-600 shows an immediate increase in air flow, making the process significantly more productive, while the e-PTFE membrane laminated on the filter media increases the filtration efficiency, consequently leading to better particle retention and, thus, lower emissions, he explains.
Kallmann says Sefar’s patented potting compound makes the sealing of end-caps almost unbreakable. The X-600 element can be operated continuously at temperatures as high as 260 °C without any degradation of the potting compound, which is usually the main reason for element destruction.
“The X-600 element is also shorter than conventional elements, protecting them from abrasion at the inlet zone, and is also an ‘all-in-one’ filter, as it has its own supportive filter cage, thus eradicating the use of conventional filter cages,” he states.
Existing conventional filtration solutions can be replaced by Sefar’s X-600 element without any modification of the baghouse – an inestimable added value – and the process profits from the reduction of the differential pressure, as the energy consumption of fans and use of compressed air for cleaning systems are significantly lowered.
The element also offers longer service life and its operational reliability minimises replacements and shutdowns.
Kallmann notes that, without proper filtration, clients lose valuable product, the environment is polluted, and health and safety is compromised.
“One cannot compromise on the need for quality and reliable filtration.”
Although industries may be similar in principle, processes are very often not and Sefar’s aim is to design, manufacture and produce products that are unique to a client.
“This is where Sefar plays a major role around the world,” he adds.
The company is at the forefront of developing new technical textiles, which are released only once proper and extensive trials have been conducted in the market, says Kallmann.
The Sefar Group head office is in Switzerland, with 27 branches globally, including its research and development team in Romania. Sefar Filter Pure is the subsidiary of Sefar in South Africa with its manufacturing facility and regional head office in Honeydew, Johannesburg. Sefar Filter Pure also has offices in Cape Town, KwaZulu-Natal and Mpumalanga.