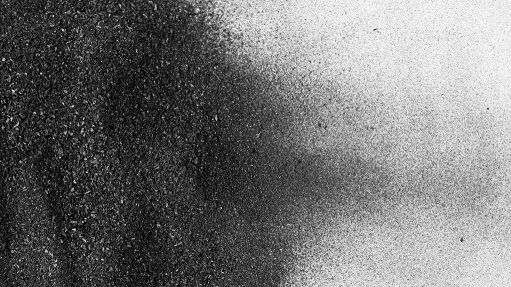
WASTE NOT, WANT NOT Process lines could easily be designed and established in proximity with local coal wastes or collieries to produce activated carbons for cost-effective adsorbed natural gas storage and transportation
Activated carbons derived from South Africa’s coal wastes present a cost-effective adsorbent for adsorbed natural gas (ANG) storage and transportation amid growing global pressure to reduce the environmental impact of the country’s coal waste.
“Coal dumps can not only potentially spontaneously ignite but can also lead to air and water pollution. Coal mining and beneficiation produce substantial amounts of coal waste, with South Africa generating 60-million tons of coal waste a year, according to the Department of Mineral Resources and Energy,” says University of the Witwatersrand (Wits) DSI/NRF SARChI Clean Coal Technology research fellow Dr Jibril Abdulsalam.
The distribution of natural gas, which is cheaper, cleaner and more efficient, with lower emissions compared with those of alternative fossil fuel sources, is currently costly and complex.
“ANG storage has been identified as the most promising low-pressure alternative to storing natural gas. However, the cost of adsorbents is a major limiting factor in the effective deployment of this technology, alongside the system's thermal control,” explains Abdulsalam.
A study published in 2020 by Wits on the natural gas storage properties of adsorbents synthesised from three different South African coal wastes: run-of-mine (RoM) fines, also referred to as duff coal, discard coal and slurry coal, revealed that activated carbons derived from these sources showed an improvement in adsorption capacity, compared with other activated carbons derived from coal-related materials.
Coal waste samples were collected from a mine 15 km south-west of Witbank, in Mpumalanga.
The study involved adsorption uptake experiments using methane as the adsorbate to measure the storage capacity of the activated carbons derived from the local coal wastes through potassium hydroxide activation.
To make activated carbons, dried samples of coal waste were mixed with potassium hydroxide at a weight ratio of 1:4. The mixed samples were placed in a furnace and heated to 800 °C at a rate of 10 °C per minute with a flow of 100 mℓ of nitrogen per minute. The samples were kept at the final temperature for two hours, and then cooled under a flow of nitrogen.
“The samples were washed using 0.5 N hydrogen chloride to remove residual alkali and, subsequently, washed with distilled water and centrifuged until the neutral pH of the samples was achieved. The washed sample was dried in an oven overnight at 110 °C,” explains Abdulsalam.
The methane storage capacities of the synthesised activated carbons were measured at 25 °C and at pressures of up to 40 bar using a particulate systems high-pressure volumetric analyser.
The adsorption isotherm of methane on the activated carbons revealed that the activated carbon synthesised from RoM fines had the highest adsorbed amount of 162.71 cm3/g at 37 bar and 25 °C, compared with discard coal (157.58 cm3/g) and slurry coal (106.69 cm3/g).
He says this can be attributed to RoM fines’ higher carbon and low ash content resulting in activated carbon with a larger surface area and pore volume.
However, irrespective of the source of the fines or discards, the sample analyses will determine the synthesis procedure and if further modification is necessary to achieve the required surface area and pore structure for the application.
“The experimental data from methane adsorption was validated with three adsorption isotherm models: Langmuir, Toth and Dubinin-Astakhov. The adsorption parameters obtained from the models are useful and important information in the design, managing the thermal effects and improving the efficiency of an ANG storage system.”
Abdulsalam adds that the chemicals and additives required for the low-cost activated carbon process are readily available and the process line could easily be designed and established in proximity with local coal wastes or collieries.