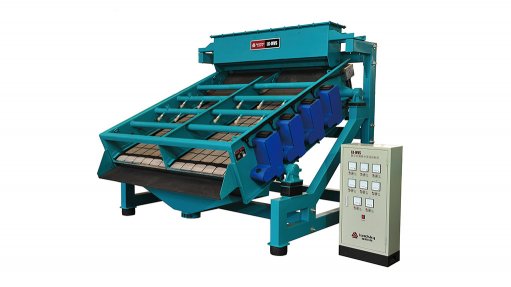
SCREENING SYSTEM Landsky is keen to service mineral sands operations in Africa as this sector presents significant potential for future growth
Chinese mineral processing equipment manufacturer Landsky believes that there is a genuine need for its processing equipment in the heavy minerals sector, as, previously, not only was fine screening equipment expensive, but lead times were long, which led to projects being shelved.
“However, we offer short delivery periods with very competitive commercial terms,” states Landsky Africa director Udo Busch.
Landsky has a 15 t/h pilot plant available for testwork on site, as the company aims to demonstrate its value proposition to potential clients.
“Generally, testwork is associated with small-scale equipment, which presents a concern in terms of scaling up. However, the test screen, with a design capacity of 15 t/h, solves this problem, as it is adequately sized and easily scaled, ensuring that we are 100% confident in using data compiled from this test unit for the design of a full-scale plant,” says Busch.
He adds that the company – already well established internationally – is keen to service mineral sands mining operations in Africa, as this sector presents significant potential for future growth.
“We’re considering mineral sands operations in KwaZulu-Natal and the Western Cape, in South Africa, as well as in Mozambique, Tanzania and Kenya.”
Additionally, Landsky has encouraged minerals companies to send material to its China-based laboratory for testwork on ore samples for classification prior to pilot testing and flowsheet development.
Although Landsky, founded in 1997, established a distribution base in South Africa only in 2012, it has exported its products into the African market in the past, which included screens for ferrous miner Kumba Iron Ore.
Busch says the company has a significant global presence, with distribution facilities and clients on every continent. Landsky has installed more than 8 000 screening units worldwide, but predominantly in Asia, Eastern Europe, the Middle East, the Democratic Republic of Congo and now in South Africa.
Busch
notes that the company services all areas of the production chain, with separate teams responsible for research, design, manufacture, marketing, maintenance and after-sales service. Landsky considers itself a leader in the development and manufacture of flowsheet and fine-ore processing equipment. “The emphasis is on research and development, proof of which is the more than 35 patents that have been registered to date. It should also be noted the company is internationally certified and compliant with quality management standard ISO 9001: 2000.”
The company’s product range includes electromagnetic high-frequency vibrating screens, as well as linear vibrating and multideck screens.
Busch notes that Landsky’s multideck screens range between 2.8 m2 and 14.4 m2. These multideck screens are equipped with polyurethane panels ranging from 75 µm to 3 mm aperture sizes.
The Landsky manufacturing facility in Tangshan High-Tech Industrial Park, in China’s Hebei province, covers an area of 48 000 m2 and includes the research centre. The manufacturing division produces 40 000 m2 of stainless steel wedge-wire welded mesh a year and 100 000 m2 of stainless steel woven-wire composite mesh a year. The smallest aperture for stainless steel panels available currently is 43 µm. These stainless steel panels are used for products such as the centrifuge baskets, sieve bends and strainers.
“The manufacturing facility is autonomous in a way,” Busch says, adding that everything is processed in-house. Landsky even buys raw rubber to produce, among others, its own rubber for lining of feed inlets, underpans and discharge chutes.
He points out that, in addition to laser technology for the high-quality production of individual components, the company also uses robotic welding for the fabrication of the screens.