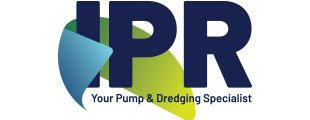
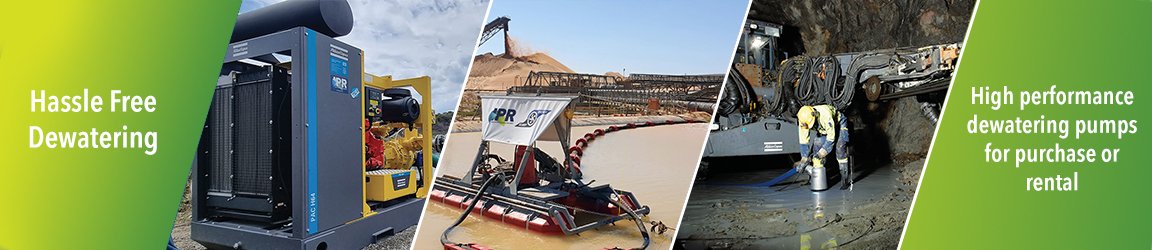
Next-gen SlurrySucker for silt-challenged water areas powered by Toyo
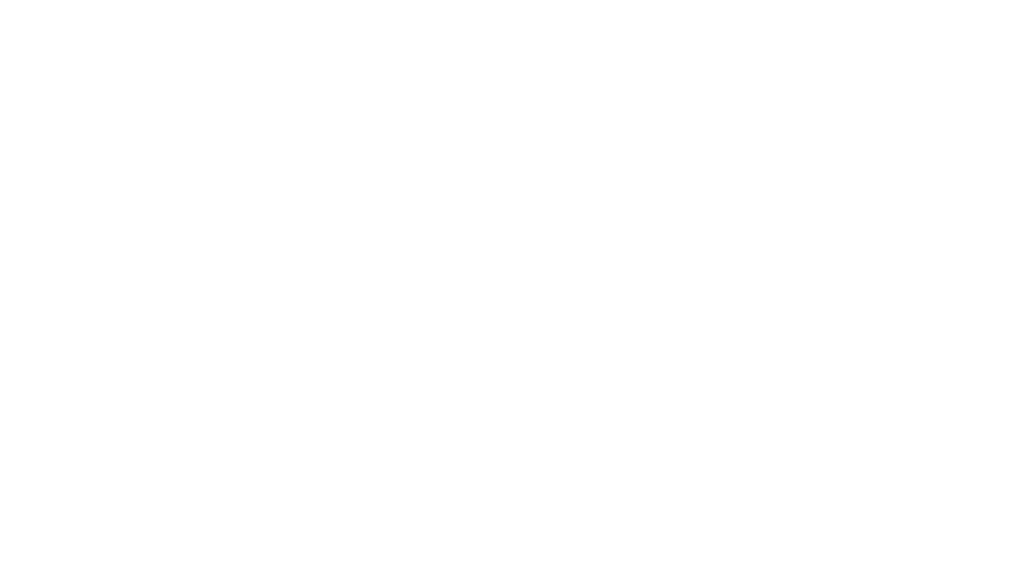
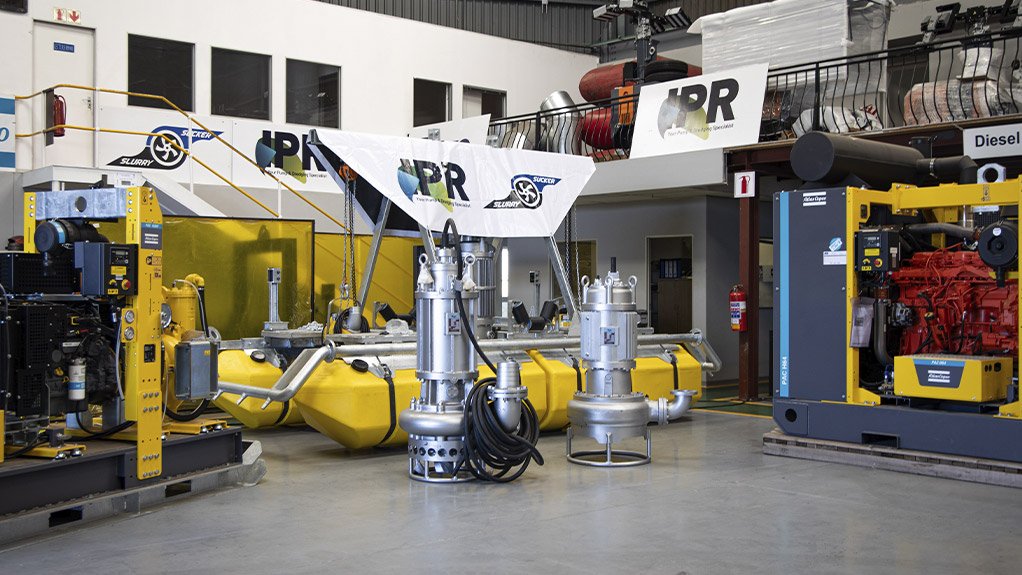
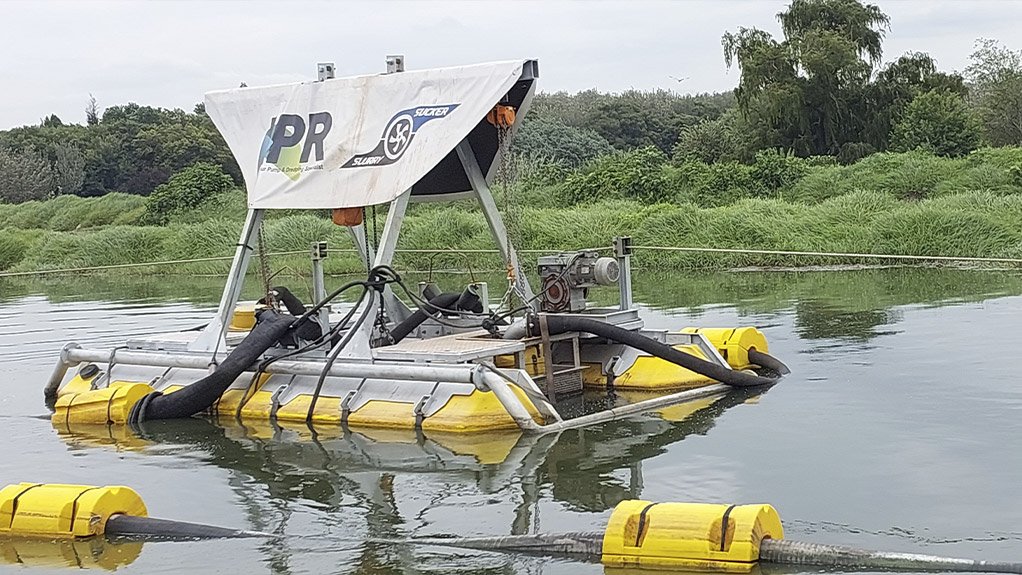
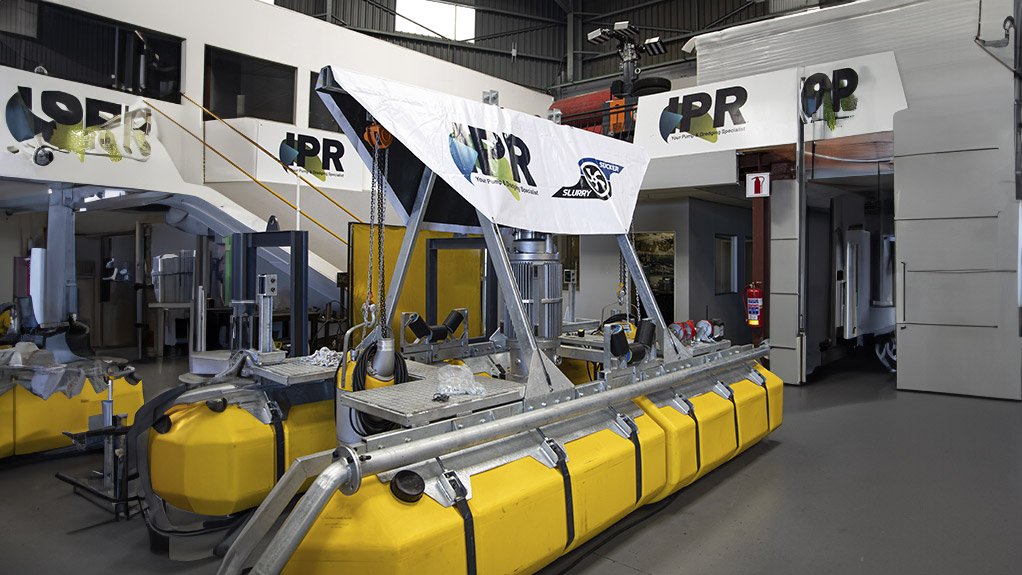
The SlurrySucker MK III incorporates the world renowned Toyo heavy duty slurry pump, making it the most efficient and cost effective electrically powered floating dredging system available on the market
Equipped with Toyo heavy duty slurry pumps, the SlurrySucker MK III boasts enhanced solids handling capabilities
The SlurrySucker MK III can be sized to meet an individual plant’s slurry removal requirements
Not only does IPR’s SlurrySucker dredging system effectively clean process water ponds, return water dams or other water storage areas, it has become recognised as an ideal solution for cleaning water capture areas where silt is an issue, or where water retention and water holding capacity is being threatened. Some of these areas are environmentally sensitive and must be protected from causing any pollution.
Taking this innovative locally manufactured product to the next step, IPR recently launched its new generation unit - the SlurrySucker MK III. This powerful dredging system now incorporates the world renowned Toyo heavy duty slurry pump, making it the most efficient and cost effective electrically powered floating dredging system available on the market.
This is according to IPR Managing Director, Lee Vine, who says that the benefits of the SlurrySucker extend well beyond improving mines’ environmental footprints. “Bodies of water such as ponds, lagoons, dams and canals should be considered valuable plant assets and must be maintained to maximise their operational efficiency and contribution to optimised operational performance,” he explains.
“This is where the SlurrySucker has continued to deliver without fail, assisting our customers with some of their pressing issues including the need to increase water storage capacities, the recovery of minerals and improving process water quality,” he continues.
Equipped with Toyo heavy duty slurry pumps, the SlurrySucker MK III boasts enhanced solids handling capabilities. The pumps are fitted with robust cutter fans or agitators, facilitating the management of larger particles. Moreover, they can effectively handle slurries with a high specific gravity (SG).
Commenting on the effectiveness of the SlurrySucker MK III, Vine says the unit can be sized to meet an individual plant’s slurry removal requirements in terms of particle size, aggregation, distribution, cohesiveness, flow characteristics, sedimentation rates and specific gravity.
He is quick, however, to point out that while desilting or cleaning of settlement ponds may seem like a simple task, it is not always as straightforward as it would initially appear. Cleaning these facilities can become an onerous task, as it involves the pumping of high solids materials from the facility being desilted and should an incorrect system or equipment that is not fit for the task be specified this could cause issues including environmental harm.
“Historically many operations have used manual excavation methods for desilting and cleaning, but our established track record has proved that this is not only inefficient, but it often fails to remove the required volume of sediment,” Vine says.
There are several ways to accomplish effective desilting, but it has to be done effectively and cost efficiently, and this is where IPR’s skilled and experienced team comes into play. The best option, according to Vine, is a site visit to assess the application requirements and conditions.
“In some instances, it is possible to pump the high solids material to another nearby dam or reservoir. However, this is sometimes not possible and in this type of scenario we implement an alternate solution such as capturing and storing the content in specialised geotextile bags while the water is separated from the solid material,” he explains.
Once the actual condition of the dam or pond has been assessed the decision can be made as to how to proceed. The SlurrySucker itself needs sufficient volume of water on which it can be floated, and should there be areas where this is not possible, then a hydro-mining solution is applied to these drier areas.
“What is also important is that we can effectively ensure mine and industrial water contaminated sites do not negatively affect surrounding areas and being equipped with remote controlled height adjustment of the primary slurry pump and dredge head assembly allows the SlurrySucker to operate without causing damage to plastic liners in dams and settlement ponds.
Vine highlights two product options – the Maxi SlurrySucker which is capable of moving 250 m³ an hour at 20% to 30% by volume – equivalent of approximately 70 dry tons per hour. The Mini SlurrySucker® operates at 100 m³ an hour, again at 20% to 30% by volume for roughly 30 dry tons every hour.
The SlurrySucker comes standard with a galvanised frame structure and IPR’s flexible design provides the option for stainless steel with polyethylene and UV-stabilised pontoons.
In conclusion, Vine says that the opting for the SlurrySucker option is also far safer as the barge itself can be operated remotely from a defined distance away from the dam or pond edge. This is much safer than having equipment and personnel on the dam.
Integrated Pump Rental