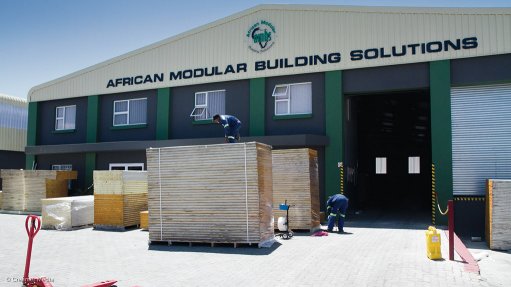
IN-HOUSE MANUFACTURING
To enhance the quality of its products, AMBS manufactures several key components in-house
Photo by: Duane Daws
The R28-million mine housing project at Zambia-based copper mine Mopani Copper Mines is currently 85% complete, reports Roodepoort-based prefabricated buildings company African Modular Building Solutions (AMBS).
AMBS managing member Allan Bellamy tells Mining Weekly that the company signed the 18-month contract with Mopani Copper Mines for the outright purchase of housing solutions for the mine in October 2013. The contract comprises the erection of modular buildings in the form of two-bedroom sleeping units, office buildings, ablution facilities and a clinic.
The mine’s housing section currently accommodates 120 personnel.
AMBS’s housing service offering to the mining industry currently consists of two-bedroom units of 84 m2, worker dormatories of 128 m2 and four-person sleeper units of 90 m2. The two-bedroom and dormitory units are the company’s most popular products in the mine site accommodation sector.
“All of our units are shipped as flat-packed units, which are assembled on site,” Bellamy says, adding that the on-site assembly of units often results in the employment of people from the local community.
The company can also incorporate ablution facilities, which it sources from a list of preferred contractors.
“Market acceptance of our products has been good and we expect good future growth in the industry,” says Bellamy.
Further, to enhance the quality of its products, AMBS manufactures several key components, such as chromadek panels and aluminium extrusions, in-house. “We also offer in-house project management services and a single point of contact for all the needs of our clients,” he says.
AMBS prefabricated buildings conform to ISO 9001:2008 for the manufacture, supply and installation of housing solutions.
Further, for short- to medium-term housing applications, AMBS provides a rental fleet of modular buildings.
Secondary equipment is also available from AMBS, including water and electrical reticulation; clean water supply equipment; power supplies, such as generators, solar panels, power-generating wind turbines and equipment for sewage disposal; and office and home furniture. AMBS can also supply kitchen, laundry and recreational equipment.
Meanwhile, Bellamy notes that the greatest challenge to providing housing solutions in Africa is the long distances between the manufacturing site, or factory, and the end-users.
AMBS has supplied its housing solutions to several African countries, including Angola, Benin, Chad, Djibouti, Ethiopia, Ghana, Kenya, Lesotho, Malawi, Mali, Mauritania, Mozambique, Namibia, Nigeria, Senegal, Sierra Leone, South Africa, Sudan, Swaziland, Tanzania, the Democratic Republic of Congo, Zambia, Zimbabwe and Madagascar.