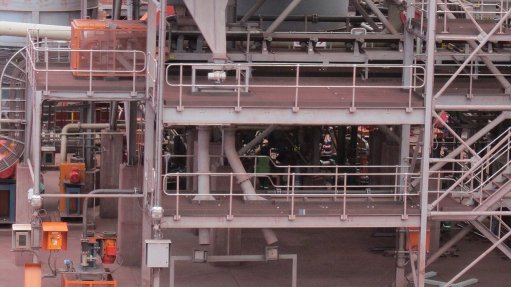
Company Announcement - A conveyor belt can account for up to 60% of the maintenance cost of a bulk materials handling plant. This means that the cost implications of constant replacement due to wear can be significantly higher than the original investment. “Maintenance outlay in the minerals processing sector can be reduced substantially by applying an innovative concept such as a Weba Chute System transfer point,” Mark Baller, managing director of Weba Chute Systems, says. “Transfer points can contribute to some of the highest maintenance costs on a mine. However, many engineers often do not view transfer systems as a critical element of the minerals processing system,” Baller argues. “Weba Chute Systems believes that transfer points should be accorded the same level of importance as any other machinery in the minerals processing cycle.”
The uncontrolled discharge of bulk materials through conventional chutes results in increased maintenance and replacement costs. “All of this adds up to unnecessary expenditure and a headache for the engineers concerned. Numerous installations of Weba Chute Systems have proved that the correct use of our streamlined, scientific approach to the dynamics of bulk materials handling greatly reduces the problems associated with conventional transfer chutes, as well as resulting in significant cost savings.”
The most common problems associated with transfer points are spillage, blocked chutes, high wear levels on the receiving belt due to major differences between the material velocity and the belt velocity, rapid chute wear, degradation of the material being transferred, excessive generation of dust and noise and misplacement of the receiving conveyor belt due to unbalanced loading from the transfer chute. Therefore Weba Chute Systems recommends a systems approach in order to ensure that operational characteristics are matched throughout the plant. Conveyors, feeders, crushers, hoppers and screens are typically selected on the basis of particular operational requirements, with little emphasis placed on the design of the chutes that transfer material between components. “However, chutes are essential components in bulk materials handling plants. It is important to note that these are also subject to operational characteristics and physical constraints,” Baller says. “The expertise of a manufacturer such as Weba Chute Systems is essential during the design stages of a project in order to eliminate potential flow and maintenance problems,” Baller says.
Weba Chute Systems’ extensive experience and technical expertise, coupled with its broad applications knowledge, has positioned it as the leader in its field. It designs systems using sophisticated 3D computer software, while data received from clients is always verified.
All Weba Chute Systems are supplied with performance guarantees in accordance with operational and application parameters. Each Weba Chute System is custom designed for the transfer point served and is configured to control the direction, flow and velocity of the calculated volume and type of material processed in a particular application.