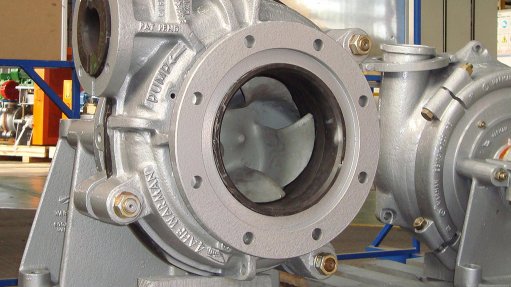
IMPROVED FROTH HANDLING A large inlet diameter and unique impeller inducer blade are able to handle heavy froth and high-viscosity dense slurries
Owing to design improvements on the Warman AHF series of heavy-duty horizontal froth pumps, the product now has enhanced and revitalised froth-handling capabilities, reports slurry equipment solutions provider Weir Minerals Africa.
The recent updates are the result of extensive testwork initiated about 18 months ago, and form part of a fundamental change in the design layout associated with the installation of the AHF pumps, which includes feed tanks, orientation and footprint.
The heavy-duty Warman AHF froth pump – based on and interchangeable with the better-known Warman AH and L pumps – has been modified to handle difficult froth slurry.
Key to the unique AHF froth pump design is a significantly larger-than-normal inlet diameter with a unique impeller inducer blade, which is able to handle heavy froth and higher-viscosity dense slurries. The larger inlet, with a correspondingly larger inlet volume, enables the pump to handle significantly greater expanded air volumes without air binding and with less surging, making it possible for the user to install a smaller pump.
Weir Minerals Africa conducted local test-work over the last seven years, based on findings drawn from research conducted in North America and Europe.
Weir Minerals Africa slurry pumps product manager Rui Gomes says this research enabled his team to understand the variability prevalent at different plants and how the AHF pump can be adjusted to respond to these irregularities.
“Being able to tap into the latest proven methods and apply them to local operations is one of the benefits of being part of a large multinational organisation,” he says.
Gomes adds that the mining industry is plagued by froth and high-viscosity problems, further noting that, in the process of recovering minerals from the ore, the slurry is often floated with strong flotation agents.
“The hydrophobic bubbles carry the con-centrate to be recovered and processed further. This can cause complications in standard slurry pumps, as conventional pumps are prone to overflowing, which leads to spillage and loss of valuable concentrate. It also poses a risk to the environment. This often results in the selection of overly large and inefficient pumps,” explains Gomes.
He points out, however, that the Warman AHF froth pump is small and efficient. “The inducer impeller and oversized inlet are effective in ensuring that froth or viscous slurries enter the impeller, enabling the pump to transport it to the next destination. Lower power costs, reliable operation, and greatly reduced surging and feed-tank overflow make this pump user friendly,” says Gomes.
He adds that, with concentration froth, there is no ‘copy and paste’ solution, as was the theory in the past, as individual applications vary over a broad spectrum.
“We therefore continue to collaborate with customers to conduct ongoing testwork that guides the application of this pump technology to suit customers’ unique processes,” he concludes.