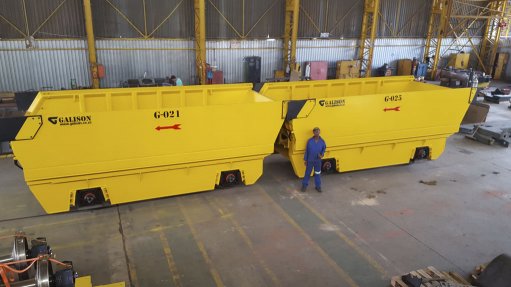
DESIGNED TO DELIVER Galison’s wagons are capable of carrying up to 40 t of rock each in trains of ten wagons, which are pulled by a 65 t locomotive
South African original-equipment manufacturer Galison last month completed the delivery of an automated underground rolling stock solution to Chinese State-owned copper mine Pulong, in Yunnan province, at a cost of about $5-million.
The delivery was completed earlier this month and the solution comprised 40 underground wagons and two tipping stations.
Galison CEO Andrew Thorburn explains that each 20 m3 wagon can carry 40 t of rock in trains of ten wagons, pulled by a 65 t locomotive along a 4-km-long stretch of rail.
The chassis of the wagons were constructed with quenched and tempered steel producer SSAB’s Strenx 700 high-strength structural steel, while the company’s Hardox 400 wear plate steel was used to fabricate the body.
Meanwhile, Thorburn highlights that the tipping solution can discharge about 200 000 t/m of rock, with a train load of 400 t being discharged on average within two minutes, significantly surpassing the local industry average of 30 minutes.
He notes that, owing to Pulong’s location 3 700 m above sea level, the tipping solutions required that the motors, supplied by electronics and manufacturing multinational Siemens, be sufficiently powered to take into the account the loss of efficiency at that altitude.
The completely automated system requires only one surface-based operator to load, drive and tip each train, and has low maintenance costs. Thorburn points out that no people are involved in operations on the haulage level at Pulong, highlighting the effectiveness of track-based systems as an automated solution.
“The running costs of this system is its big advantage over trackless equipment,” Thorburn says, adding that the running costs of the system are basically null for five to ten years.
“This system does not use diesel or require spare parts and uses very little electricity. This system just works.”
He suggests that the system highlights that mechanisation and automation techniques are not always ideally suited to trackless mining. “In fact, it is much easier, more efficient and cost effective to automate a track system, as track systems allow for equipment to be moved exactly where you want it . . . and requires no steering system.”
Galison won the contract in June last year and started manufacturing at its facility in Welkom, in the Free State, the following month. Delivery started in September, while the installation of the solution started in January and final commissioning having taken place earlier this month.
Thorburn notes that the company was awarded the contract because of its quick manufacturing and delivery turnover time, as well as the competitive price of its solution.
Galison designed and manufactured the mechanical aspects of the system, while Chinese State-owned mining automation company Beijing Soly Technology developed the automation aspects. Thorburn states that the two companies will partner to sell this solution to other mining operations in Africa.