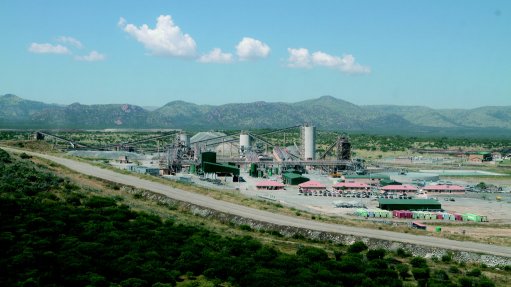
PILANESBERG PLATINUM MINE The implementation of General Electric Intelligent Platform’s Proficy Plant Applications software has brought measurable improvements to production processes for Platmin’s Pilanesberg platinum mine
General Electric (GE) Intelligent Platforms, a unit of US multinational conglomerate cor-poration GE Energy, has partnered with RKA Consulting, the South Africa-based technical support, training and product sales supplier of GE Intelligent Platforms software, to supply its Proficy Plant Applications software solution to TSX- and JSE-listed Platmin’s Pilanesberg platinum mine.
The Proficy Plant Applications software, which is suitable for any mine or large-scale pro- duction process, is used to automate and inte- grate information-related activities for managing production execution and performance optimis-ation, and to help businesses balance the trade-offs across the many competing priorities of production operations.
The software also provides a good manufac-turing execution and manufacturing intelligence environment for tracking and optimising operat- ing efficiency, energy and resource consump-tion, product and process quality, environmental and product safety compliance, schedule execu-tion, work-in-progress inventory tracking and genealogy/traceability.
Three of four phases of integrating the Proficy Plant Applications modular solution into the existing Proficy iFIX human–machine interface/supervisory control and data acquisition system have been completed over the last 18 months, without any loss of data or production during the installation of the software.
The implementation of the software has brought measurable improvements to production pro-cesses for the mining company and has been able to reduce machine downtime.
The open and scalable Proficy Plant Appli-cations solution enables equipment monitoring in real time and the capture of downtime for main-tenance purposes, while also enabling managers and engineers to have visibility of the process and to see how each piece of equipment is performing and whether it is meeting yield targets, says GE Intelligent Platforms Mining & Metals division regional manager Johnny Teixeira.
“The supply chain of heavy equipment in the crushing and milling process is crucial for the mine, and we monitor the process plant and the equipment in it,” he says.
In addition, the software enables managers and engineers to see whether a machine is losing time, when a machine is failing and why it is failing.
Teixeira adds that the software looks at yields in real time, enabling managers to immediately monitor the yields of different ore blocks, thereby enabling quicker decision-making to maintain production levels.
The Pilanesberg platinum mine, located on the western limb of the Bushveld Complex, in the North West, comprises a single opencast mine with its own crushing and milling facilities. It has a processing capacity of 417 000 t/m through its concentrator, as well as a monthly milling capacity of 285 000 t.