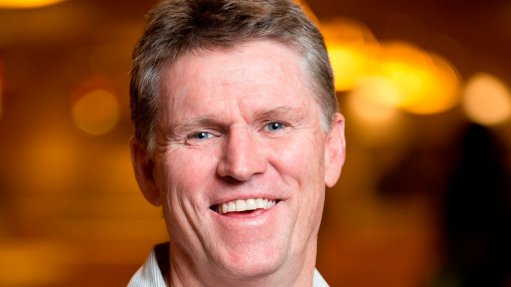
DAVE BODY MineCycle is the first of Bentley’s products created through syndicated development, whereby industry participants were directly involved in developing the software’s definition and design
Global infrastructure software developer Bentley Systems last week launched its new range of mining software applications, developed in collaboration with mining technology solutions provider Cyest Technology, through a syndicate-driven development programme (SDDP) with mining majors Anglo American Platinum, AngloGold Ashanti, Royal Bafokeng Platinum and Lonmin, as well as engineering firms Hatch, GHD Group and PDC Group.
Bentley’s new MineCycle range of mine planning solutions help mining industry participants tackle some of their most pressing challenges, including the need for a continuous, rather than an intermittent, mine-planning cycle.
Based on Bentley’s software foundations, the MineCycle products comprise MineCycle Designer, MineCycle Survey and MineCycle Material Handling. They are the first Bentley products to be created through syndicated development, whereby industry participants are directly involved in developing the software’s definition and design.
“Leading South African mining houses have been trying to collaborate for more than a decade to drive improvements in the industry’s mine planning systems,” said Lonmin technical services head Jurgens Visser earlier this month in Johannesburg, during the Bentley Advantage Seminar, where MineCycle was launched.
He explained that this was finally achieved in 2012, when Bentley and Cyest approached the mining majors to help develop the next generation of general mine-planning solutions.
“SDDP members, [who met once a month], determined the functional requirements of the new industry product and, therefore, were empowered as part of this new paradigm,” added Visser, describing the collaboration as an “industry first”.
The development programme took place over 100 weeks, with 22 iterations, ensuring that SDDP members saw progress on a monthly basis and that the final product met exact functional user requirements.
Visser explained that like-minded industry stakeholders had been working for years to do away with the traditional bespoke linear mine-planning system, which does not take situational change into account.
“We aimed to get the best outcome for everyone, providing industry with the ability to provide direct input into the software’s definition and design,” said Bentley Systems solutions executive Dave Body at the launch.
He explained that, through open communication with key mining stakeholders, Bentley and Cyest identified the key challenges that companies face regarding mine planning, including insufficient planning agility, information silos and insufficient time to explore alternative options.
The SDDP found that time-consuming traditional processes, which can take up to six months, prevent the consideration of alternatives or a change in the mine plan and can result in strategies that are out of sync with changing mine and market conditions.
Bentley and Cyest aimed to counteract the current linear mine-planning process, designing MineCycle Designer and MineCycle Survey to work together to greatly accelerate mine planning and incorporate mine survey iterations.
The third product in the range, MineCycle Material Handling, enables engineering, procurement and construction (EPC) firms and consultants to accelerate the preliminary design of bulk materials handling facilities. Employing the same ‘optioneering’ principle as MineCycle Designer and MineCycle Survey, MineCycle Material Handling empowers EPCs to quickly consider multiple scenarios.
The MineCycle software range therefore enables ‘optioneering’, which is Bentley’s way of describing the ability of mine owner-operators to assess multiple operational alternatives, enabling higher-quality decision-making that subsequently ensures enhanced operational performance.
“Companies can now automate the normal administrative steps of mine design and scheduling, thereby enabling mine planners to make technical decisions that pertain to what the economic output variables are,” said Cyest Techonology MD Gary Lane.
He explained that the product consolidates mine design, scheduling and evaluation, which enables a mine planner to consider every possible scenario, compared with a company following the traditional linear mine-planning approach, where a plan is often outdated by the time the company starts production.
Lane believes MineCycle is going to radically change the way mine planning is done in future. “By applying new innovative approaches to planning and scheduling, mine management can now test different production planning options to understand the impact on the economics of a mine and thereby derive a more optimal plan that meets the strategic objective of the business.”
Bentley simulation product management VP Robert Mankowski said: “This ability to quickly assess operational planning and engineering alternatives was one of the ‘musts’ that our syndicate development sponsors identified.”
He added that Bentley’s collaboration with strategic software partner Cyest Technology and the syndicate sponsors was instrumental in developing MineCycle and that this collaborative approach to product development enabled industry leaders to mutually influence the design of new products.
“Thus, the mining industry is now assured of solutions to high-priority business challenges and Bentley has been able to mitigate risk and accelerate time to market,” Mankowski concluded.