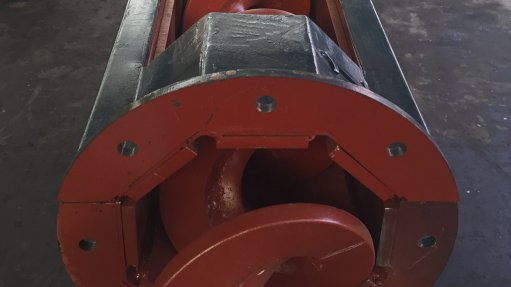
DIFFICULT MATERIALS DEALT WITH Shaftless spiral screw conveyor systems effectively handle bulky and abrasive solids that often cling to the central pipe of a conventional shafted screw conveyor
Spiral pipe machines manufacturer Spiral Tech Screw Conveyors says its custom-built shaftless spiral screw conveyors are gaining popularity in the mining industry, owing to their ability to reduce costs and boost productivity, especially in applications involving difficult materials.
As an alternative to conventional shafted screw conveyors, shaftless screw conveyors are not a new phenomenon in materials handling, notes the company, based in Boksburg, Gauteng, a member of machinery manufacturer Pan Mixers South Africa.
However, Spiral Tech manager Dawie Verster says the company is aiming to raise the profile of this tried and tested technology in the mining industry through “innovative designs”.
“Spiral screw conveyors are designed specifically to handle bulk solids with high moisture content discharged from centrifuges, filter presses and mixers. “This is material that conventional shafted screw conveyors cannot process easily,” he explains.
In most instances, these bulky and abrasive solids have the additional characteristic of being extremely sticky and, thus, tend to cling to the central pipe of a conventional shafted screw conveyor, Verster points out, adding that spiral screw conveyors do not have this central pipe and, instead, use the spiral shape of the conveyor to convey such difficult materials with ease.
Spiral Tech’s shaftless screw conveyor system also reduces maintenance requirements as it has no hanger bearings or end bearings. Moreover, lower speeds reduce both wear and tear on the system components and energy consumption. The largest available system is up to 45 m wide and 20 m high, making it big enough for most materials handling applications in the mining industry.
In addition, Spiral Tech is capable of designing systems that can operate horizontally or at various angles, depending on a client’s specific requirements. A motor and gearbox driven by a variable frequency drive is connected to one end of the spiral using a flanged and bolted drive shaft and spiral end plate. Significantly, the tail end of the spiral is unattached and allowed to rotate freely, which results in significant energy savings and improved performance, comments Spiral Tech.
Verster highlights that the strength and hardness of the spiral is critical to the long-term success of an installation. “For example, if you are conveying an abrasive bulk solid, you need a spiral that is extremely hard to reduce the amount of abrasion on the shaftless spiral.”
He further points out the importance of the trough liner used in these applications, noting that popular choices are tough ultrahigh molecular weight polyethylene and xylethon.
The shaftless screw conveyor system addresses current demands in the mining industry for reduced operating costs and increased productivity, states Verster. “Through constant research and development, Spiral Tech has managed to supply custom-built products to suit the process needs and objectives of its diverse customer base.”
Apart from shaftless screw conveyor systems, Spiral Tech’s product range includes live bottom systems, vertical conveyor systems, dewatering presses and grit classifiers.