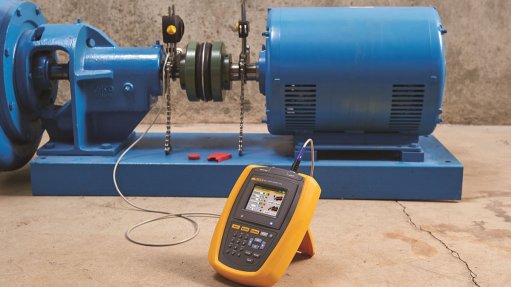
LASER PECISION Unlike the straight-edge method or dial indicators, Flukeās 830 performs complicated alignment calculations automatically
All rotating machinery is susceptible to misalignment and the conventional methods of measuring alignment, such as rulers and dial indicators, are outdated and inaccurate, says industrial equipment supplier Comtest Group.
The company points out that these methods could result in inadequate alignment, thereby costing the end-user “thousands of rands a year in replacement bearing costs, hours of unnecessary repair time, crippling unplanned downtime and a probable decrease in the machine’s useful life”.
The South African distributor of industrial testing equipment manufacturer Fluke, Comtest advances the use of the Fluke 830 laser shaft alignment tool, specifically engineered for precision-aligned rotating shafts.
It stresses that the Fluke 830 offers simple functionality and provides fast, accurate and actionable answers. “Unlike the straight-edge method or dial indicators, Fluke’s 830 performs complicated alignment calculations automatically.”
This means users have the answers needed to quickly align the machine. An enhanced user interface provides easy format results that do not require extensive alignment knowledge. The results screen shows both coupling results and vertical and horizontal measurement corrections in real terms, allowing for corrective alignment action.
Other device features include the single laser measurement technology, which ensures reduced errors, thereby enhancing data accuracy; an intuitive guided user interface for easy alignment and a compass measurement mode for reliable and repeatable measurements using an activated electronic inclinometer.
The device also includes a dynamic machine tolerance check, which provides continuous evaluation of alignment adjustments so that the end-user can see when the machine is within an acceptable range (of alignment); a unique extend mode, which handles gross misalignment by virtually increasing the laser detector size and a data protection feature with auto save and resume capability, allowing the user to recover measurements when needed.
The 565 mm × 343 mm × 127 mm Fluke 830 laser alignment tool comprises a laser sensor, laser prism, a chain-type mounting bracket with 150 mm support posts, a microfibre cleaning cloth, sensor and PC cables, as well as a 64 MB USB drive and cable.
The device has 64 MB random-access memory and is powered by an integrated lithium-ion polymer rechargeable battery, which has a typical operating time of 17 hours.
Weighing 5.6 kg, the Fluke 830 laser alignment tool has an ingress protection rating of IP 65, indicating that it is dustproof and water spray resistant. It is also shockproof and has an operating temperature range between –10 ºC and 50 ºC.
Comtest notes that, since machine downtime is costly, testing repeatability or retest reliability – where there is little to no variation between multiple tests conducted on the same piece of equipment under identical or similar conditions in a short period of time – is critical.