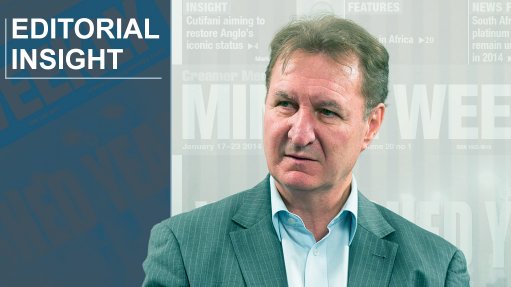
Serious thought is being given to the modernisation of the South African mining industry following the plea at the Joburg Indaba by Anglo American Platinum (Amplats) independent chairperson and apartheid struggle veteran Mohammed Valli Moosa.
It sometimes takes a person with a political bent to put the message across forcefully, which is what Moosa did when he said last October that the marathon January to May strike in the platinum belt was tantamount to a revolt against back-breaking, low-wage and low-skill jobs and that the industry subsequently needed to move towards modernisation.
There is evidence that even in the late seventies the gold mining industry had a modernisation blueprint that for some inexplicable reason died on the vine, presumably because of a decision at the time to put political modernisation ahead of mining modernisation.
The official reason that a backfill technology could not be found sounds hollow and many believe there was more behind the long delay in the introduction of what AngloGold Ashanti is now implementing to mine gold-rich shaft pillars as a forerunner of bigger things to come.
Lonmin Platinum also tried to introduce ultra-low-profile (ULP) mining equipment to take on South Africa’s narrow reefs. Enthusiastically, Mining Weekly ran what proved to be an overoptimistic headline at the time entitled ‘Gulp! Here comes ULP’. But that involved drivers of machines not being able to sit upright and having to assume reclining positions. Because of the height-restricted reef areas, unloading of the load-haul-dump vehicles was by push action.
Veteran research commentator Dr Robbie Robinson last year put up a very convincing case for the use of a process called selected blast mining, which ingeniously separates the precious metal from the waste underground.
This involves only the precious metal being brought to surface and waste remaining underground for use as backfill. But, for some unknown reason, this has largely fallen on deaf ears, one imagines, because of the large volume of work done in continuing to drill and blast, but in an automated fashion, using a suite of remotely controlled extra-low-profile (XLP) and ULP machines to do the job.
Amplats has put serious thought into initiating a ten-year-long process of converting its mines into sustainable, mechanised mining systems using XLP and ULP equipment (Mining Weekly January 23).
For the past seven years, the platinum major has been trialling two XLP equipment suites at its Rustenburg-based Bathopele platinum mine, as well as advanced ULP prototypes since 2010.
The focus for 2015, reveals Amplats technical executive head Gordon Smith, is to make these ULP prototypes – designed and manufactured by Croatia-based unmanned vehicle producer Dok-Ing – production- ready for 2017.
Once that is achieved, the company aims to complete the implementation of these new technologies by 2019.
Central to the implementation of this technology is an improved on-reef stoping layout and design that allow for the implementation of either the ULP or the XLP technologies, says Smith, adding that trialling of the layout and design is already under way at Bathopele.
Mines need to run like factories to become more profitable, says the University of the Witwatersrand’s Centre for Mechanised Mining Systems director Declan Vogt.
Thankfully, that penny is now clearly beginning to drop.