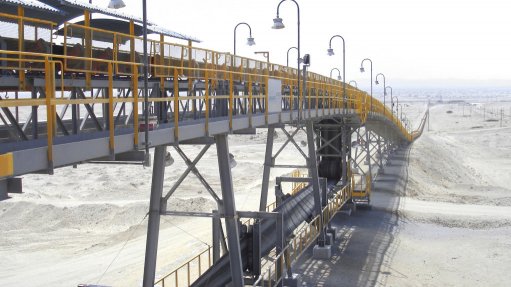
LOW-WEIGHT INNOVATION Despite their light weight, the new Sandvik HR185 composite rollers are durable in demanding, medium to heavy duty conveying applications
Tooling, materials technology, mining and construction engineering group Sandvik Group has launched its latest generation all-composite roller, the Sandvik HR185, which is a low-weight, low-noise innovation for conveyor systems.
The rollers feature a composite tube and moulded composite end caps which hold the bearings and seals, explains Sandvik Mining global product line manager Chris Mitchell.
While other plastic rollers rely on the physical properties of a single primary shell material to deliver both strength and abrasion resistance, the two shells of the Sandvik HR185 rollers are formed by advanced processes to deliver a two-part composite tube that can handle all the running loads of a steel roller at a significantly reduced weight.
The composite shell material of the rollers is up to 70% lighter than the shell used on traditional steel rollers and up to 40% lighter than other plastic shell materials on the market.
Mitchell adds that, despite their light weight, the new Sandvik HR185 composite rollers are durable in demanding, medium to heavy-duty conveying applications.
Further, the significantly lower weight allows for safer, easier handling and helps reduce the risk of injuries that can occur while installing new rollers or replacing failed rollers during maintenance.
The new composite rollers also deliver significantly more value than competing steel rollers, from lower cost to corrosion resistance in wet and high-salt environments, the company states.
The Sandvik HR185 rollers are also suitable for noise-sensitive applications, including export terminals and conveying installations near populated areas, as they generate more than 50% less noise than traditional steel rollers. The natural dampening effect of the composite means that the rollers reduce noise impact on the surrounding environment.
“In addition to improving safety and increasing productivity, Sandvik HR185 rollers can reduce total cost of ownership by up to 20%,” says Mitchell.
He explains that the rollers require less time and manpower to install and maintain, while their reduced power demand, as a result of a lower rotating inertia, means savings in electricity costs.
In addition, should a roller reach the end of its service life and stop rotating, there is no steel end cap to damage the belt, reducing the risk of belt damage.
The large, nonrotating end cap covers up to 90% of the roller face and helps limit damage to seals and bearings from dirt, rocks and other material build-up at the roller face, further extending the roller life and reducing costs, Mitchell says.
The rollers are also suitable for high speeds and large tonnages and are available in diameters from 152 mm to 178 mm, with bearing sizes from 6 306 up to 6 310.