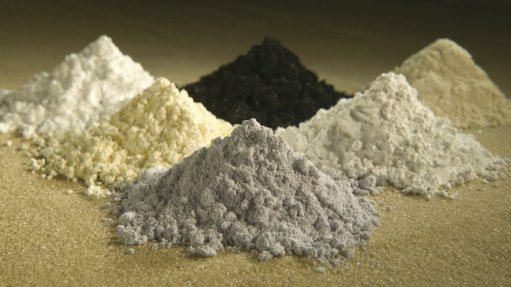
Name of the Project
Saltend Chemicals Park rare-earth oxide separation facility.
Location
Saltend Chemicals Park, in Humber, Yorkshire, in England, in the UK.
Project Owner/s
Pensana (formerly Pensana Rare Earths).
Project Description
The Saltend Chemicals Park is a cluster of world-class chemicals and renewable-energy businesses, including bp Chemicals, Ineos, Nippon Gohsei and Air Products. It will be the first major rare earths separation (MRES) facility to be built in more than a decade and the first to be located in a Freeport.
The project study outlines plans to establish the world’s first sustainable rare earths separation facility, which will primarily treat material sourced from the Longonjo mine, in Angola.
The Longonjo mine will treat 1.6-million tonnes a year for 20 years.
The rare earths processing facility will produce 12 500 t/y of separated rare-earth oxide, of which 4 500 t/y will be magnet metal rare earths – neodymium and praseodymium oxides – equivalent to about 5% of the projected world demand for magnet metals in 2025.
Potential Job Creation
The project is expected to create 100 direct jobs once it is built and in operation.
Net Present Value/Internal Rate of Return
The project has a net present value, at an 8% discount rate, of $2.4-billion and an internal rate of return of 61%, with a payback of 2.1 years.
Capital Expenditure
The Saltend refinery is expected to cost $195-million and the MRES refinery $127-million, while the Longonjo concentrator and Longonjo mine and infrastructure will cost $123-million and $49-million respectively.
Planned Start/End Date
Commissioning and production are due to start in the fourth quarter of 2023 in the UK and Angola.
Latest Developments
A comprehensive value engineering and optimisation programme is well advanced and is expected to be reported in May and is expected to result in a further reduction in capital costs.
Worldwide supply chain constraints and inflationary pressures brought about by Covid-19 and the recent Ukraine-Russia conflict, which could have impacted on the Saltend and Longonjo projects, have been largely mitigated by these detailed optimisation and value engineering processes, Pensana has said.
Specific workstreams, involving capital and operational cost savings, currently under way, include spent acid regeneration to maximise the recycling efficiency of the sulphuric acid plant, integrated with off-gas from the calcining of concentrate at Longonjo.
In addition, Pensana is piloting a more cost-effective flotation concentrate calcining process offered as a vendor alternative post-front-end engineering design (FEED), which it says will enable a significantly shorter lead time for fabrication and ease of installation at Longonjo.
There is also the optimisation of Saltend’s civil and earthworks for load-bearing structures undertaken alongside the completion of detailed geotechnical investigation.
Further, there has been piloting of process simplification opportunities discovered in the precipitation circuit at Longonjo.
Key Contracts, Suppliers and Consultants
Wood Group (FEED); pxGroup (construction); PPM (owners representative); Wood, and Snowden Mining Industry Consultants (capital expenditure estimate, the operating cost budget and the project schedule).
Contact Details for Project Information
Pensana, email contact@pensana.co.uk.