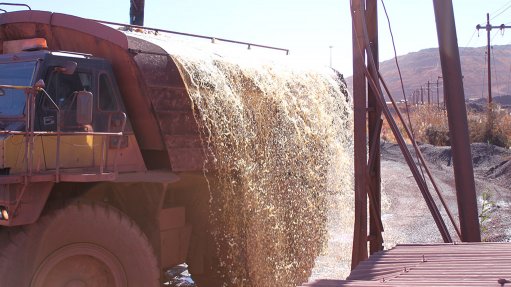
WATER SAVER I-Cat’s radio-frequency identification system monitors and reports water and product use
Envionmental management company I-Cat Environmental Solutions has installed six radio-frequency identification (RFID) and electronic camera (E-Cam) systems to monitor water bowsers at a Northern Cape-based iron-ore mine to eliminate water spillage, and will roll this out to the remaining 12 water bowsers before the end of this year.
“This spillage is caused by the refilling of water bowsers,” says I-Cat Environmental Solutions innovation division manager Wayne Wagener.
Current research shows that accidental spills, caused by incorrect alignment with the discharge point of the water-filling station, can cause water loss of up to 2 800 ℓ in ten seconds.
Wagener points out that the RFID system reduces operational costs, saves water and increases productivity, as well as other environmental benefits.
In addition, the system contributes to operator safety by eliminating the need to depart from the driving capsule to ensure that alignment with the discharge point of the water filling station is correct, he says.
“The RFID system automatically identifies the vehicle, its capacity and current water levels. The system then activates the water pump, and the product or dust-suppression pump, and fills the tank accordingly. Any risk of injury to the operator is eliminated and a safe work environment is created,” Wagener explains.
He notes that when the tank is full, the unit will automatically switch off the pump to ensure that there is no water or product spill.
Wagener further points out that I-Cat’s system monitors and reports on water and product use, which can be accessed using secure software. This, in turn, can be used for audit trails and the reporting structures of the mining company.
I-Cat’s software also enables a mining company to determine the productivity of the vehicle and operator through the logging of work hours, vehicle idling time and vehicle non- operational hours.
Wagener adds that control room operators can monitor the vehicle using mapping software and satellite tracking as an optional extra. The software indicates the progress of the vehicle while it is spraying, which is useful when implementing structured spraying protocols.
Meanwhile, the E-Cam system is an extension of the RFID system, as it tracks vehicle movement on the mine using an integrated global positioning system to manage and improve dust- suppression management systems on haulage roads.
Wagener notes that there is currently a gap in the mining industry to effectively monitor and coordinate mine vehicles, especially water bowsers used to suppress dust on haulage roads.
He adds that there is also a need in the industry for a system – like I-Cat’s RFID solution – to mitigate accidental spills caused by filling-alignment problems.
“Water is becoming a scarce and expensive commodity and its use is becoming more regulated. Never in the past has it become more necessary to manage the efficient use and to eliminate unnecessary wastage than now. No such system has been available commercially until now, Wagener concludes.