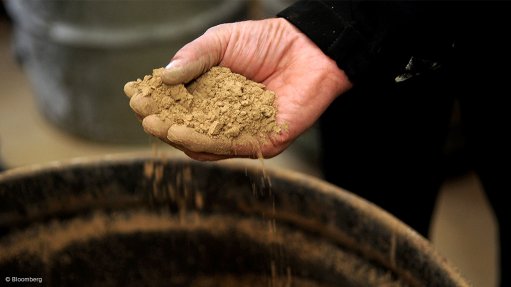
Photo by: Bloomberg
TORONTO (miningweekly.com) – A preliminary economic assessment (PEA) of the Lofdal rare earths project, in Namibia, had given investors in project promoter Namibia Rare Earths their first positive indications of the economic potential of the project.
The TSX-listed project developer on Wednesday reported the positive findings of a PEA on the $155.74-million rare earths project, indicating an after-tax cumulative cash flow of $257-million, with a net present value at a 10% discount rate of $147-million, and an internal rate of return of 43%.
The study confirmed that based on the initial National Instrument 43-101-compliant mineral resources for the Area 4 deposit, the north-western Namibia project could produce an average of 1 500 t/y of separated rare earth oxides (REO) to be sold at the base case average price of $105.77/t.
“The PEA confirms the strengths of the project in terms of its favourable rare-earth distribution and amenability to conventional mining and processing, and demonstrates its financial strengths in terms of the low capital costs and significant cash flows.
“The PEA provides a clear path forward for development of the project. Management believes that there remains considerable upside to the project as we move toward prefeasibility and feasibility studies. Together with ongoing metallurgical optimisations, we will target additional drilling to significantly expand mineral resources and to establish mineable reserves, thereby extending the life-of-mine. The company will aggressively pursue the most expeditious path towards development of Lofdal through all available options,” Namibia Rare Earths president Donald Burton said.
At a cutoff grade of 0.1% total rare earth oxides (TREO), the Area 4 deposit currently held a resource of 2.88-million tonnes in the indicated category, yielding 9 230 t of REO, of which 7 050 t was estimated to be heavy rare earth oxides (HREO) and 3.28-million tonnes in the inferred category, yielding 8 970 t of REO, of which 6 700 t was estimated to be HREO. The remainder of the REO was made up of light REO.
The PEA indicated that there was considerable potential to expand the current mineral resource and recommended more drilling to see whether the mine life could be extended beyond the current 7.25 years. This would be carried out in conjunction with a forthcoming six-month prefeasibility study programme.
Mining would be by conventional openpit methods using an owner-operated mine fleet at a mining rate of 2 500 t/d, or 840 000 t/y, with the ultimate pit reaching a vertical depth of 200 m, providing 6.04-million tonnes of ore at a diluted grade of 0.28% TREO over the current mine life.
PROCESS FLOW SHEET
The PEA had established tentative flow sheets for processing the Lofdal ores.
After secondary and tertiary crushing, the feed would be delivered to X-ray technology and X-ray fluorescent sorters to eliminate internal waste, thereby reducing the volume proceeding to the ball mill for fine grinding. The ball mill product slurry would be fed to the rougher magnetic separator with tails going through three scavenger magnetic stages. The magnetic concentrate product would be subjected to a cleaner flotation circuit and then passed through a concentrate thickener before the acid leach circuit.
The leach circuit would use a four-stage hydrochloric acid (HCl) leach to dissolve the carbonate minerals. A gangue leach centrifuge circuit would provide for a primary acid water wash to remove the entrained dissolved calcium chloride solution and a secondary potable water wash, with a second centrifuge for solid/liquid separation. The resulting solids would be filtered in a press for final concentrate bagging and shipping to a hydrometallurgical facility, which the company had proposed to build at the deep-water port of Walvis Bay.
Concentrate batches of 29 t each would be shipped in containers over a distance of 375 km to the hydrometallurgical facility for caustic cracking and washing. The caustic cracking plant would be designed to break, or ‘crack’, the phosphate component of the rare-earth mineral xenotime to access the contained thorium that would be removed by a subsequent HCl leaching stage.
Following the caustic cracking stage, the washed residue would be transferred to the HCl digestion tank to leach the thorium. Subsequent precipitation steps would produce a thorium hydroxide product for storage and a rare-earth hydroxide product to be combined with the HCl digestion residue as a final product for drying and drumming.
Namibia Rare Earths said the Lofdal project was not large enough in scale to support capitalisation for a separation plant and it was expected that the final product would be delivered to a third-party facility and subject to an offshore treatment charge.