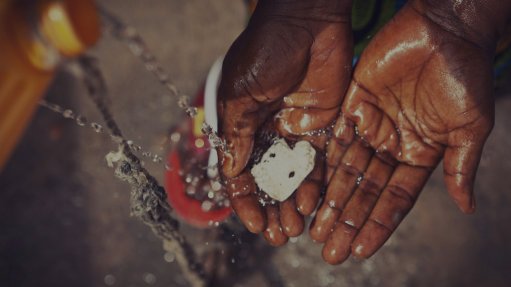
BACK-TO-BASICS In both the fields of health and safety the focus is on preventing injury or illness
Occupational health and hygiene practitioners share a common vision with safety practitioners, which is that of ensuring zero harm to all mineworkers and a healthy and productive workforce, through the effective management of occupational health and safety risks in the workplace, says diversified mining major Anglo American occupational health and hygiene leader Dr Cas Badenhorst.
“A working environment cannot be safe if it is not healthy; and a working environment cannot be healthy if it is not safe,” he states.
Badenhorst says that, in both the fields of health and safety, the focus is on preventing injury or illness. He explains that, in the case of safety, the impact of an incident is immediate and usually affects an individual or small number of individuals, whereas a health risk can potentially affect a large number of individuals and even whole communities in some cases. Badenhorst highlights that health concerns are usually a result of exposure to a health hazard or a combination of health hazards over a long period of time.
“In other words, safety is the ‘now’ and health is the ‘future’, or indeed, the effects of the ‘past’ that we need to manage. They are merely different points on the same timeline. They are different impacts that happen at different speeds, but with the same potentially harmful results.”
Further, he notes that occupational disease takes a long time to develop and, by the time it is diagnosed, it is very difficult to reverse and, in some cases, cannot be fixed at all. Badenhorst remarks that exposure to noise, dust, chemicals and other health hazards, such as vibration and temperature extremes, can lead to ill-health if not properly managed and controlled and, it is, therefore, “critically important” that the controls that are in place to manage this exposure are continuously monitored.
“If we start treating each potential health risk as a safety risk, as if there could be an immediate impact or an immediate injury, we would be able to avoid many of the health problems that we only pick up years later,” he points out.
Badenhorst comments that a workers’ health can also have an immediate impact on their safety. He says that, if workers are fatigued or unwell at work, they are potentially compromising their own safety and that of their colleagues. Badenhorst adds that increased absenteeism also puts pressure on the workers that turn up for work, requiring the need for change management.
An underlying health element applies in all five main types of change – physical changes (new controls), new or modified equipment, equipment failure, new or different materials and chemicals or substances – all of which demand health-risk management.
Badenhorst states that health issues can lead directly to “people change”, such as in the case of having new or different team members, change in an individual’s personal circumstances, regular absence of a supervisor or operator on shift or even a change in someone’s usual behaviour.