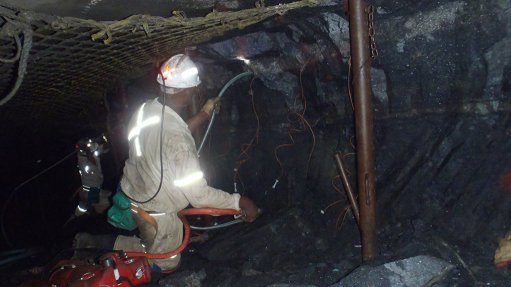
BLASTING EFFICIENCY BME’s portable charging unit enables mines to employ safer and more cost-effective emulsion-based blasting technology
Mining explosives company BME is establishing a 300 m vertical emulsion pipeline – the deepest in the world – at a South African gold mine currently implementing BME’s new narrow-reef emulsion system.
The pipeline, scheduled for completion at the end of this year, will reduce the usual shaft time required to transport emulsion underground.
BME research and development manager Selwyn Pearton tells Mining Weekly that the pipeline will function in conjunction with BME’s new mechanised emulsion charging units (ECUs), as well as the narrow-reef emulsion system, which was installed in 2013.
The ECUs will be fitted with BME’s recently launched Mobile pump technology, increasing both the reliability, efficiency and safety of charging practices within mechanised mining operations.
In addition to the new Mobile pump tech-nology, BME’s portable charging unit (PCU) for narrow-reef operations will also make use of the vertical pipeline. “BME’s PCU has been developed especially for emulsion charging in narrow-stope mining environments, enabling mines to employ safer and more cost-effective emulsion-based blasting technology in highly confined underground spaces,” Pearton says.
He adds that the 14 kg pump can be carried to the blast face for charging and that the emulsion is contained in two 20-kg-capacity bags that can be filled aboveground or at a central refilling point underground. The bags are then sealed to avoid any contamination by dust or dirt. The bags are connected to the pump at the blast face just before charging, says Pearton.
The fail-safe pump control mechanism ensures that blasting performance and emulsion costs are carefully controlled, as it allows for the mass of explosives for each hole to be preset, he adds.
While rigorous trials of the new narrow-reef emulsion system have been conducted on multiple operations since the launch of the product, BME currently has agreements in place to complete a roll-out of the system at two large operations in South Africa, Pearton says.
“Owing to the positive market reaction to the system, the level of interest has necessitated expansion within the underground division,” he notes.
“Meanwhile, as part of its endeavour to develop more effective blasting methods, BME has manufactured its own microcontroller-based control system to monitor and record data on the performance of its emulsion pumps.
Pearton highlights that the company used its electronics expertise to develop its in-house pump controller, enhancing the company’s range of emulsion pump technology currently in oper- ation at opencast and underground mines. He notes that BME is applying the controller to its full range of mechanised emulsion units.