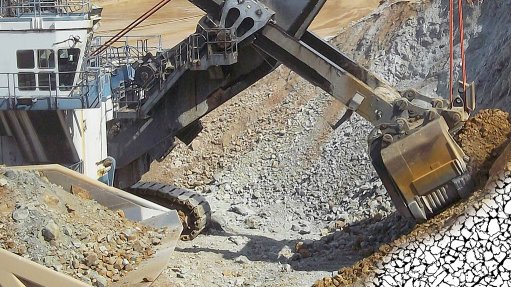
ACCURATE RESULTS The Split-ShovelCam system automatically captures images of post-blast muckpiles so that operators can be immediately updated with rock fragmentation results
Miners are now able to quantify the post-blast fragmentation of rocks using the Split-ShovelCam system, an economical alternative to manual sampling that provides an instant objective measure, as opposed to subjective qualitative estimates.
The system, whose latest version was released in September by US-based coarse-rock fragmentation size-measurement systems company Split Engineering, provides a key metric of rock particle sizes.
The particle-size data enables users to adjust blast designs to improve the efficiency of energy consumption, throughput and equipment use, thereby saving costs.
Split-ShovelCam is an automated online muckpile-fragmentation monitoring system that was engineered for use on mobile digging equipment such as hydraulic excavators and cable shovels.
The system automatically captures images of post-blast muckpiles so that operators immediately receive rock fragmentation results. The system makes it possible for mine operators to collect and integrate high-volume rock-size data, enabling true post-blast particle sizes to be instantly trended and modelled.
The Split-ShovelCam system offers advanced imaging algorithms to determine the best moment to take an image of the dig cycle so that quality images of the muckpile can be captured.
Since the system was released, Split Engineering has refined it to incorporate enhanced features that enable the increasingly accurate location of rock particles and identification of regions of fines.
Particle size information and data are immediately produced and integrated into user-enabled systems for review, analysis and feedback. Mine operators can compare particle data to determine the optimum sizing for run-of-mine handling and feed forward processing.